Mold costs depe…
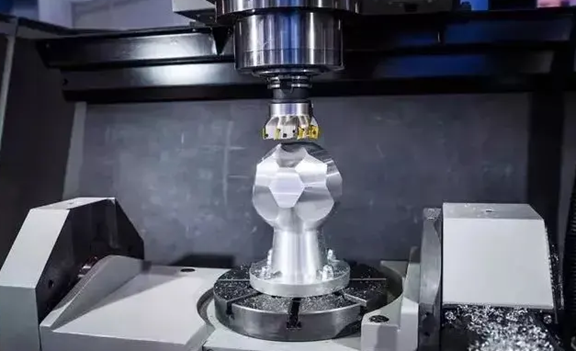
What is the CNC technology of CNC machining?
“CNC” refers to the numerical control technology of computerized numerical control (numerical control for short). Traditional machining is operated by hand with ordinary machine tools. When machining, shake the mechanical tool by hand to cut metal, and measure the accuracy of products with caliper and other tools by eyes. Modern industry has long used computer digitally controlled machine tools for operation. CNC machine tools can automatically process any products and parts directly according to the program compiled by technicians in advance.
It is a method of using digital information to control the movement and machining process of machine tools. The machine tools that implement machining control with numerical control technology, or the machine tools equipped with numerical control system, are called numerical control (NC) machine tools. Among them, the numerical control system includes: numerical control device, programmable controller, spindle driver and feed device. CNC machine tool is a highly integrated product of machine, electricity, liquid, gas and light. To realize the control of the machine tool, it is necessary to use geometric information to describe the relative motion between the tool and the workpiece, and use process information to describe some process parameters that the machine tool must have, such as feed speed, spindle speed, spindle forward and reverse rotation, tool change, coolant switch, etc. These information are formed into processing files (i.e. NC processing programs in normal terms) in a certain format and stored on the information carrier (such as magnetic disk, perforated paper tape, magnetic tape, etc.), and then read in by the NC system on the machine tool, or input directly through the keyboard of the NC system, or input through communication, and decode them, so as to make the machine tool act and process parts Modern CNC machine tool is a typical product of mechatronics. It is the technical basis of a new generation of production technology and computer integrated manufacturing system.
The development trend of modern CNC machine tools is high-speed, high-precision, high reliability, multi-function, compound, intelligent and open structure. The main development trend is the research and development of intelligent full-function general numerical control devices with open structure in both software and hardware. Numerical control technology is the basis of machining automation and the core technology of numerical control machine tools. Its level is related to the national strategic position and the level of national comprehensive strength. It develops with the development of information technology, microelectronics technology, automation technology and detection technology.
CNC machining center is a kind of CNC machine tool with tool magazine, which can automatically change tools and carry out a variety of machining operations on workpieces within a certain range. The characteristics of machining parts on the machining center are: after the machined parts are clamped once, the NC system can control the machine tool to automatically select and replace the tools according to different processes, automatically change the spindle speed, feed rate of the machine tool, the motion track of the tool relative to the workpiece and other auxiliary functions, and continuously carry out multi process machining such as drilling, spot facing, reaming, boring, tapping and milling on each machining surface of the workpiece.
Because the machine tool can adjust and store the workpiece in a centralized way, it can greatly reduce the processing time and measurement efficiency, and greatly improve the efficiency of machining and automatic processing. Machining centers can be divided into vertical machining centers and horizontal machining centers according to the position of the spindle in space.