Mold costs depe…
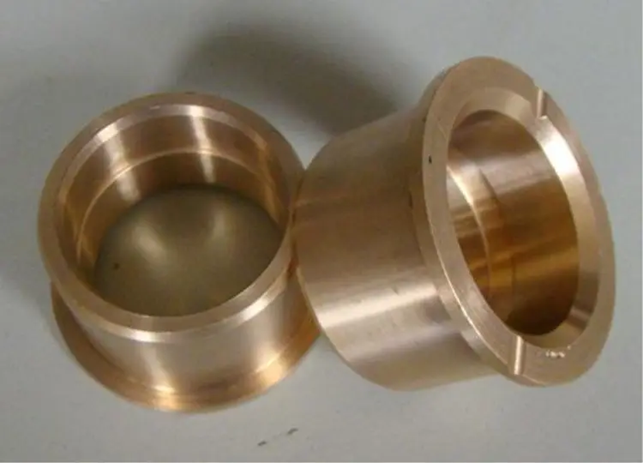
Understand various forming processes of metal materials (II): Plastic forming
2、 Plastic forming
Plastic forming: it is a process method of less cutting or no cutting by using the plasticity of materials and under the action of external forces of tools and molds. It has many kinds, mainly including forging, rolling, extrusion, drawing, stamping and so on.
(1) Forging
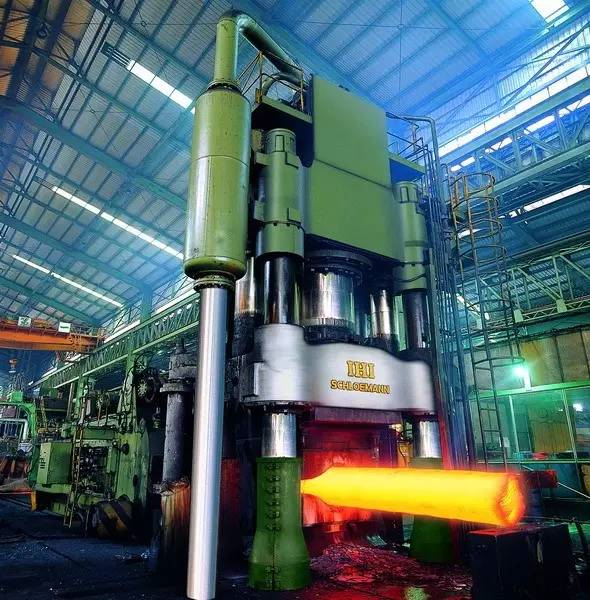
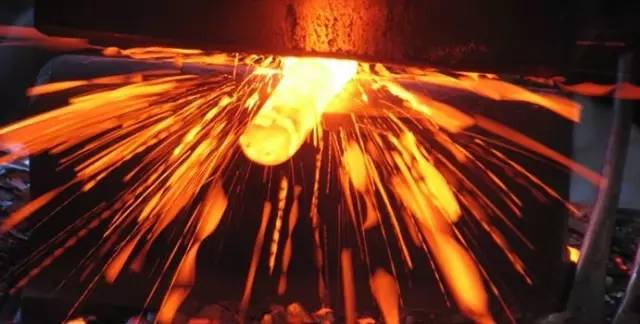
Forging: it is a processing method that uses forging machinery to exert pressure on metal blank to produce plastic deformation, so as to obtain forgings with certain mechanical properties, certain shape and size.
According to the forming mechanism, forging can be divided into free forging, die forging, ring grinding and special forging.
a. Free forging: it is generally a processing method of hammering metal ingots or blocks into the required shape and size with simple tools on hammer forging or hydraulic press.
b. Die forging: it is formed by using a die on a die forging hammer or hot die forging press.
c. Ring grinding: refers to the production of ring parts with different diameters by special equipment ring grinding machine. It is also used to produce wheel parts such as automobile hub and train wheel.
d. Special forging: including roll forging, cross wedge rolling, radial forging, liquid die forging and other forging methods, which are more suitable for the production of some special shape parts.
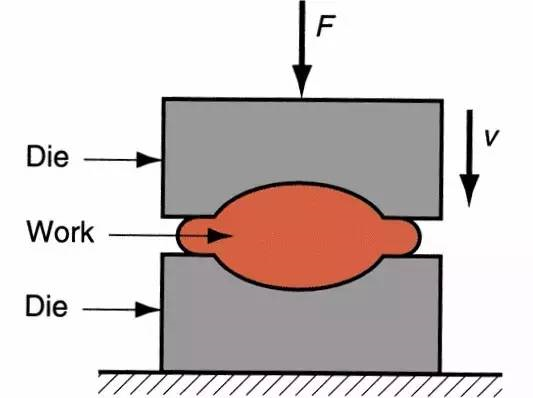
Process flow: forging billet heating → roll forging preparation → die forging forming → trimming → punching → correction → intermediate inspection → forging heat treatment → cleaning → correction → inspection
Technical features:
1. The quality of forgings is higher than that of castings, and can withstand large impact force. The plasticity, toughness and other mechanical properties are also higher than those of castings or even rolled pieces.
2. Save raw materials and shorten processing hours.
3. High production efficiency.
4. Free forging is suitable for single piece and small batch production with great flexibility.
Application: roll and herringbone gear of large steel rolling mill, rotor, impeller and retaining ring of steam turbine generator set, huge hydraulic press working cylinder and column, locomotive shaft, crankshaft and connecting rod of automobile and tractor, etc.
(2) Rolling
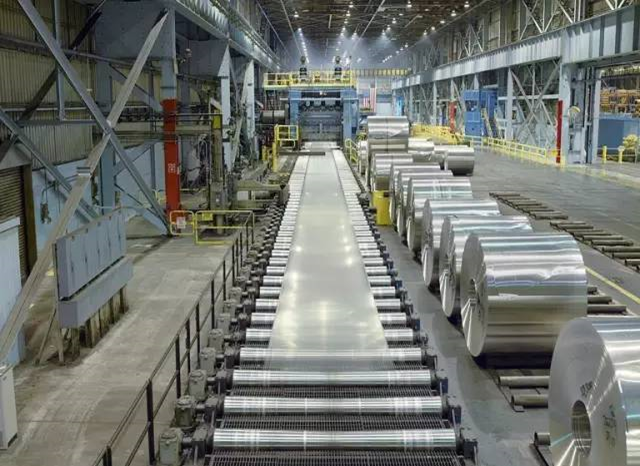
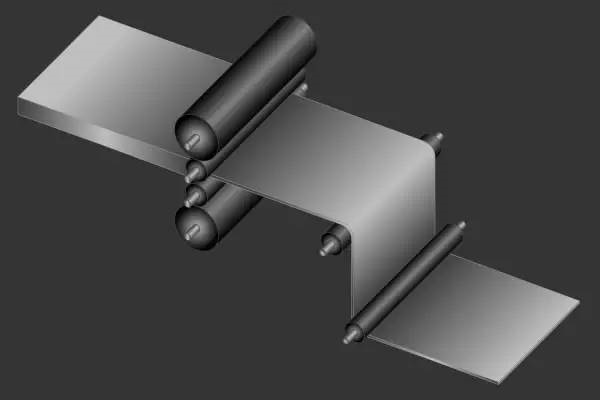
Rolling: it is a pressure processing method in which the metal blank passes through the gap (various shapes) of a pair of rotating rolls, and the material section is reduced and the length is increased due to the compression forming rolling of the rolls.
Rolling classification: according to the movement of rolled pieces, longitudinal rolling, transverse rolling and cross rolling.
a. Longitudinal rolling: the process in which metal passes between two rolls with opposite rotation directions and produces plastic deformation between them.
b. Cross rolling: the movement direction of the rolled piece after deformation is consistent with the direction of the roll axis.
c. Cross rolling: the rolled piece moves in a spiral motion, and the axis of the rolled piece and the roll is not at a special angle.
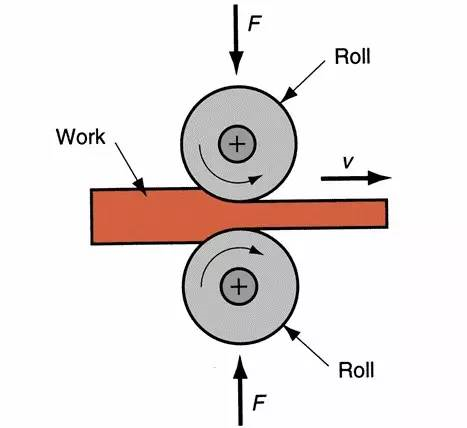
Application: mainly used in metal materials, profiles, plates, pipes, etc., as well as some non-metallic materials, such as plastic products and glass products.
(3) Extrusion
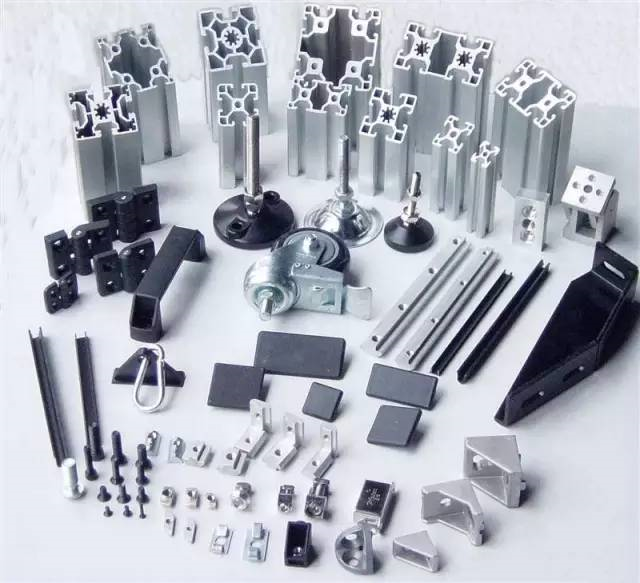
Extrusion: under the action of three-dimensional uneven compressive stress, the blank is extruded from the orifice or gap of the die to reduce its cross-sectional area and increase its length. The processing method to become the required product is called extrusion, and this processing of the blank is called extrusion molding.
Process flow: preparation before extrusion → heating of casting rod → extrusion → stretching, twisting and straightening → sawing (sizing) → sampling and inspection → manual aging → packaging and warehousing.
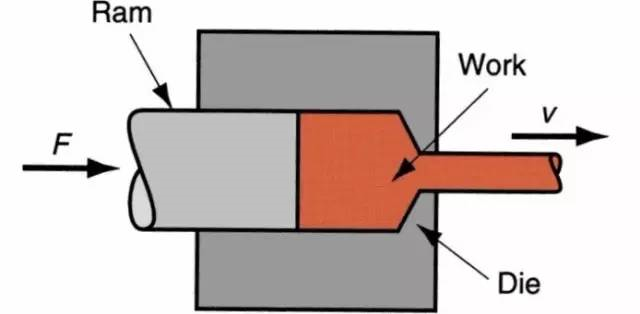
Process advantages:
1. Wide production range, many product specifications and varieties;
2. Production flexibility, suitable for small batch production;
3. The product has high dimensional accuracy and good surface quality;
4. With less equipment investment and small plant area, it is easy to realize automatic production.
Process disadvantages:
1. Large loss of geometric waste;
2. Uneven metal flow;
3. Low extrusion speed and long auxiliary time;
4. Large tool loss and high cost.
Production scope of application: mainly used for manufacturing long rod, deep hole, thin wall and special-shaped section parts.
(4) Drawing
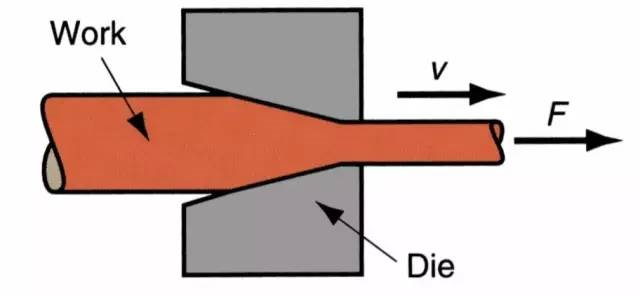
Technical advantages:
1. Accurate size and smooth surface;
2. Simple tools and equipment;
3. Continuous high-speed production of long products with small section.
Technical disadvantages:
1. The total deformation between pass deformation and two annealing is limited;
2. The length is limited.
Production scope of application: drawing is the main processing method of metal pipes, bars, profiles and wires.
(5) Stamping
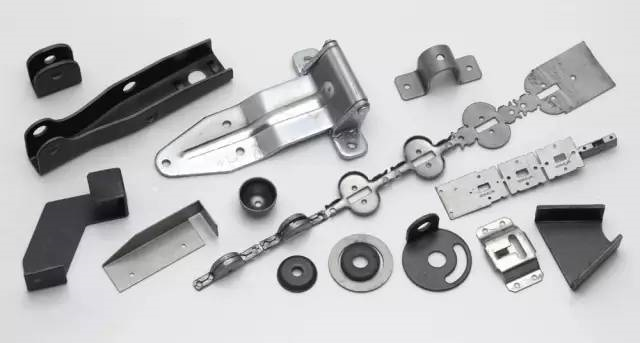
Stamping: it refers to the forming and processing method of the workpiece (stamping part) with the required shape and size by applying external force to the plate, strip, pipe and profile by the press and die to produce plastic deformation or separation.
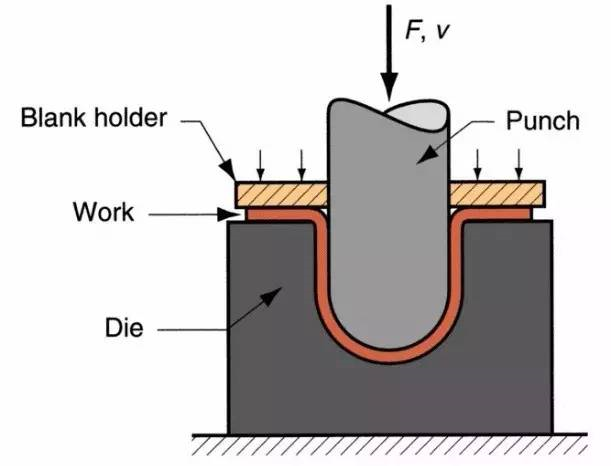
Technical features:
1. Products with light weight and high rigidity can be obtained.
2. Good productivity, suitable for mass production and low cost.
3. Products of uniform quality can be obtained.,
4. The material has high utilization rate, good shearing and recycling.
Production scope of application: 60 ~ 70% of the steel in the world are plates, most of which are made into finished products by stamping. Automobile body, chassis, oil tank, radiator sheet, boiler drum, container shell, iron core and silicon steel sheet of motor and electrical appliances are all stamped. There are also a large number of stamping parts in instruments, household appliances, bicycles, office machinery, household utensils and other products.