Mold costs depe…
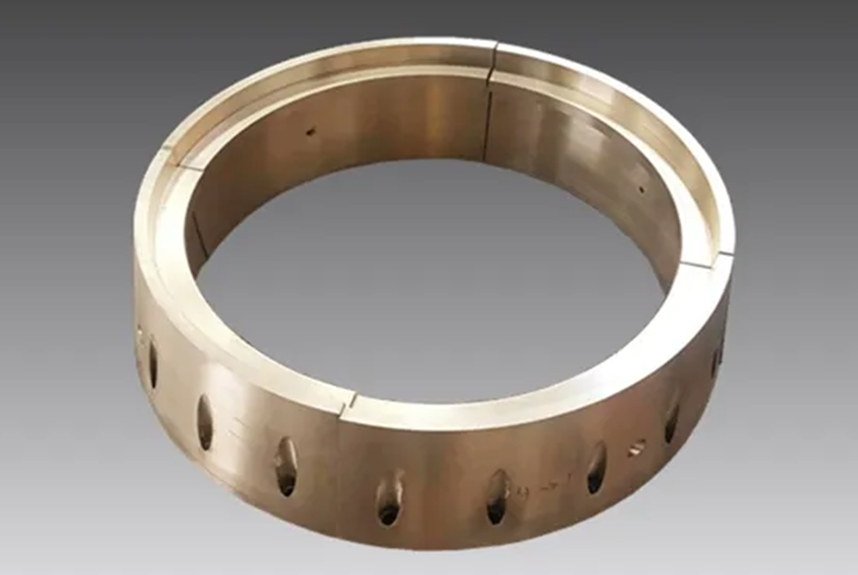
Two main factors determining the production cost of castings
The manufacturing costs of different castings in each process are not completely the same, but some links have very small differences, which can be calculated according to the average level. We should pay attention to those factors that have a greater impact on the cost of castings. The main factors leading to the cost difference in the casting production process are as follows:
1. Process yield. Process yield, also known as yield, is the percentage of the actual casting weight in the pouring weight. For specific castings, the process yield is equal to the percentage of the total casting weight in the tree weight in the same tree. It is related to the casting structure and tree formation scheme, and may vary from 30% to 60%, usually between 40-50%. The relationship between the front section cost and the process yield is that the front section cost per kilogram of casting=the front section cost per kilogram of pouring weight The front section cost per kilogram of casting is inversely proportional to the process yield. The lower the process yield, the higher the front section cost per unit weight of casting, and the lower the process yield, the more significant the impact.
2. The number of shell making layers varies with the shape and structure of the casting.
The cost of pickling and hardening of castings is about 0.3 yuan/kg. Although the carbon steel parts do not need pickling and hardening, the cost difference can not be distinguished because of the need to buckle the box after pouring, the difficulty of sand removal after the box is buckled, and the need for rust prevention and other factors for finished products.
(1) Shaping: The castings that are easy to deform need to correct their deformation. The difficulty of reshaping depends on the casting structure, deformation degree and the customer’s requirements for size and geometric tolerance. The cost of reshaping shall be accounted for separately. Objectively speaking, casting surface defects are unavoidable. Different customers or castings for different purposes have different requirements for surface quality. It is very important for the supplier and buyer to determine a reasonable quality acceptance standard based on the characteristics of castings and possible surface defects before receiving orders. If the customer has high requirements for surface quality, the repair cost will be relatively high. The repair cost is mainly affected by the casting quality requirements and the first pass rate of castings. The former needs to be considered in pricing while the latter depends on internal quality control. The renovation cost can be adjusted by multiplying the average post-treatment cost by the appropriate quality grade coefficient.
(2) Sand cleaning: Some castings with narrow slots or long and thin holes are difficult to clean, and can only be cleaned by sand drilling, acid biting, sand blasting or alkali blasting. For such castings, the cost of sand removal shall be estimated separately.
(3) Renovation: The casting production process is a special production process, and there are many factors affecting the casting quality.
The cost difference of post-treatment mainly comes from three aspects: sand cleaning, deformation correction and renovation. The cost depends on the casting structure and technical requirements. The cost difference should be considered when determining the price.