Mold costs depe…
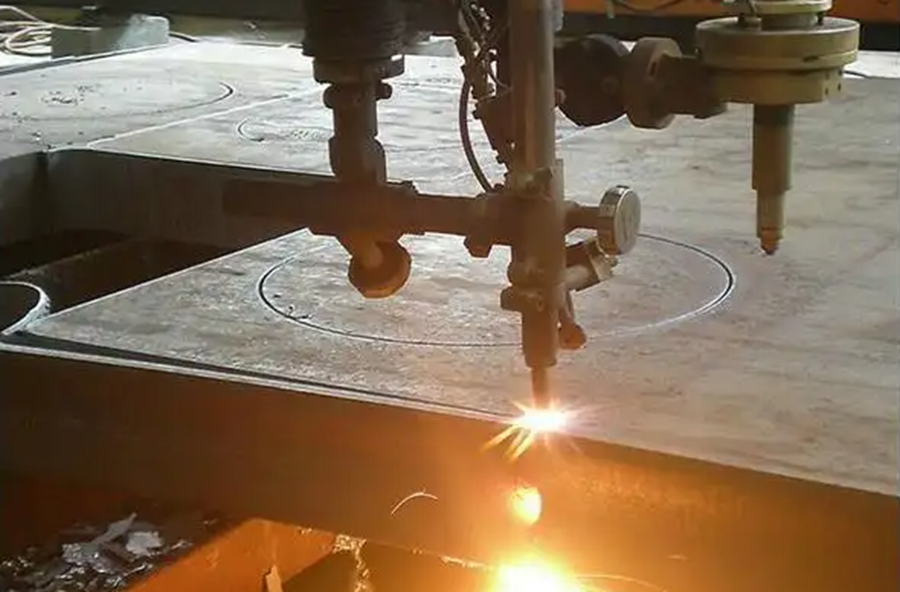
Three control technologies to prevent cutting deformation of steel plate
During later processing, the steel plate will be deformed after cutting due to warping, resulting in scrapping of workpieces, affecting the normal use of users, and causing economic losses to the enterprise.
The analysis shows that there are residual stresses in the internal and upper and lower surfaces of the steel plate after hot rolling. If the residual stresses are distributed unevenly along the width and length of the steel plate, a moment will be generated on the steel plate section, which will cause the steel plate to warp after cutting. The control measures are:
1. TMCP technology
The new TMCP technology refers to the process of rolling under continuous large reduction when the final rolling temperature is ≥ 950 ℃, followed by ultra fast cooling at a cooling rate of up to 300~400 ℃/s.
The continuous large deformation strain accumulation in the steel plate using the new TMCP technology makes the austenite hardened, and then ultra fast cooling is carried out. On the one hand, the hardened austenite is kept unchanged, that is, the hardened austenite is “frozen”. On the other hand, the ultra fast cooling also promotes the precipitation of a large number of fine particles below 20 nm, and with the continuous reduction of the ultra fast cooling temperature, the particle distribution is more dispersed.
Because of the ultra fast cooling, the nucleation rate is improved and the ferrite grains are refined. Keep the ultra fast cooling state to stop cooling near the phase change point, and then control the cooling path to obtain the steel plate with excellent performance. At the same time, continuous rolling at normal temperature makes the accumulated dislocations slip and precipitate, and the high energy state stress can be released.
2. Cooling temperature
The imbalance of internal stress caused by laminar cooling is mainly caused by three types of uneven cooling: (1) severe uneven transverse cooling; (2) Asymmetrical cooling in the thickness direction; (3) The transverse and thickness directions are cooled unevenly.
It is necessary to control the transverse uniformity of cooling and the symmetry of thickness direction to control the flatness of medium and thick plates and reduce the internal stress. The lateral cooling side injection scheme achieves the uniformity of laminar cooling temperature control by improving the horizontal angle of the lower header and the water retention point.
3. Cold straightening
Straightening can improve the residual stress distribution of the steel plate. When there is uneven stress distribution on the cross section of the steel plate, roll bending measures can be taken to increase local deformation to compensate for uneven length of longitudinal fibers, so as to eliminate wave bending and homogenize the internal stress of the steel plate.
Adjusting the transverse crown value of the straightener is also an important measure to improve the residual stress distribution of the steel plate.
To sum up, the new TMCP process is adopted to improve the uniformity of laminar cooling speed and control temperature, and the steel plate is cold straightened to promote the homogenization of the internal stress of the steel plate. When the steel plate is further sliced, the deformation problem is controlled.