Mold costs depe…
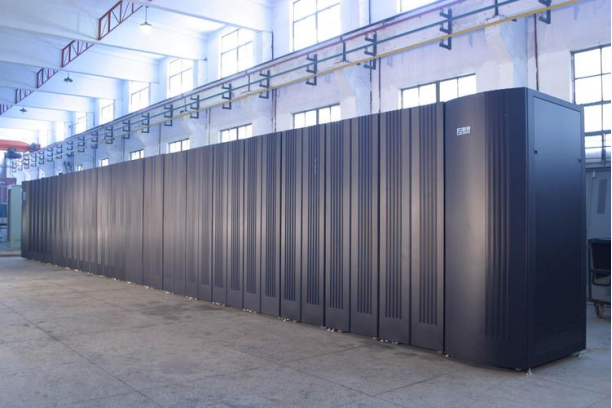
Thermal knowledge of server cabinet processing technology
As the shell of the server, the cabinet has also been greatly developed with the eruption of cloud products in China, and the market demand is growing year by year.
According to the data released by the Information and Communication Development Department of the Ministry of Industry and Information Technology, from 2017 to 2019, the number of server cabinets in use nationwide was 1.66 million, 2.262 million and 3.145 million respectively. In the future, with the maturity of 5G and other network technologies, the server cabinet market will continue to show a steady growth trend.
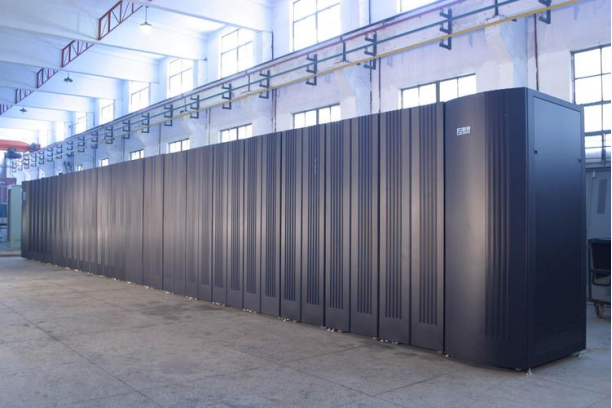
Requirements for server cabinet
The server cabinet is composed of a frame and a cover plate (door), which generally has a rectangular shape and is placed on the ground. The cabinet structure should have good stiffness and strength, as well as good electromagnetic isolation, grounding, noise isolation, ventilation and heat dissipation performance.
In addition, the server cabinet shall be resistant to vibration, impact, corrosion, dust, water and radiation, so as to ensure the stable and reliable operation of the equipment. Therefore, the industry has relatively high requirements for finished products.
Server cabinets are divided into standard cabinets and non-standard cabinets. Standard cabinet refers to that the main structure of the cabinet has formed a fixed form in the industry, and the production standards and structural dimensions have certain industry standards or national and international standards.
At present, standard cabinets include network cabinets (19 inch rack structure), DC screen protection cabinets (mainly used in the power industry, with 19 inch and 21 inch rack structures inside), high-voltage power cabinets, low-voltage power cabinets (such as GGD cabinets, power distribution cabinets), etc.
Processing method of non-standard cabinet
In addition to standard cabinets, many customers also put forward personalized requirements for cabinets based on product characteristics.
This kind of non-standard cabinet generally belongs to the category of sheet metal processing. According to the product specifications, models and quality parameters given by customers, it is processed through thermal cutting, mechanical cutting, stamping, bending, assembly and other processes before surface treatment, so as to produce a personalized service cabinet.
Thermal cutting of chassis and cabinet
For the materials that can not be removed by the shearing and punching processes, or the plates with high hardness that are easy to damage the mold, such as the fillets, or the shapes required for stamping without the ready-made mold, laser cutting can be used to complete the forming of materials before bending.
Because of the high requirements for server cabinets, plasma cutting or laser cutting are generally used in the industry. However, the quality of laser cutting is better. This is a very fast and accurate cutting method, which can ensure good results
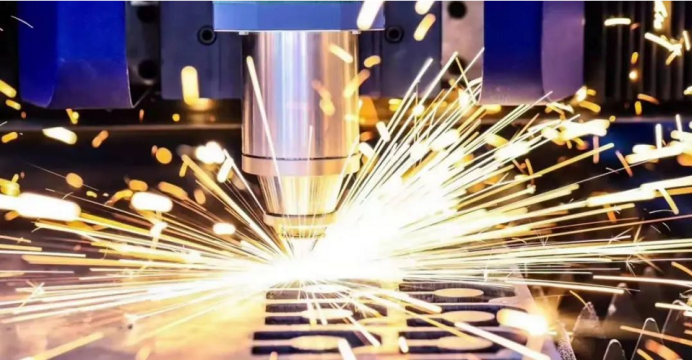
Mechanical cutting of chassis and cabinet
Cutting or die cutting of chassis and cabinet refers to the process of cutting without burning or melting sheet metal, which is essentially not different from cutting clothes with scissors. In the shearing process, the punch presses the workpiece on the fixed mold or blade, and the gap between the two makes the workpiece unable to pass, thus completing the shearing.
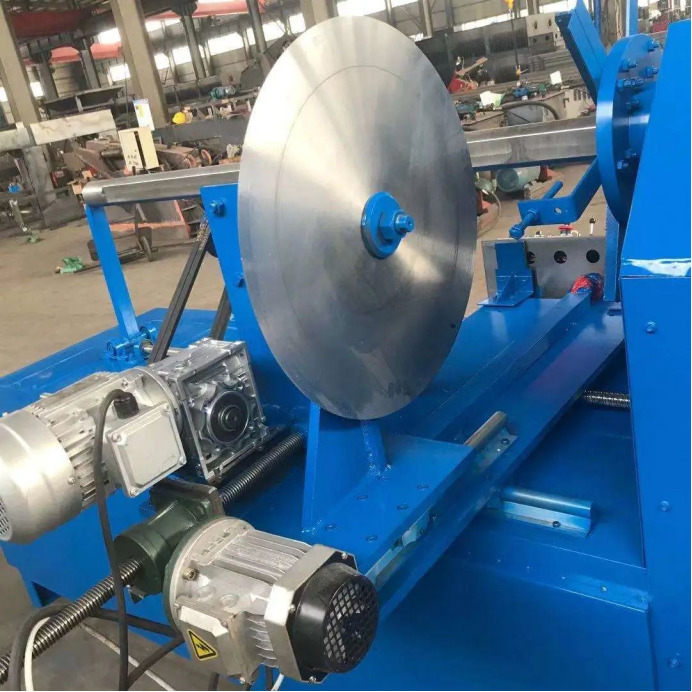
Stamping of chassis and cabinet
The equipment of stamping process is a punch, which can further process and shape the cut materials. Different dies are required for stamping various shapes. Common dies include round holes, oblong holes, bosses, etc., with high accuracy requirements. This process is suitable for large-scale production, but it is not cost-effective for small batch production.
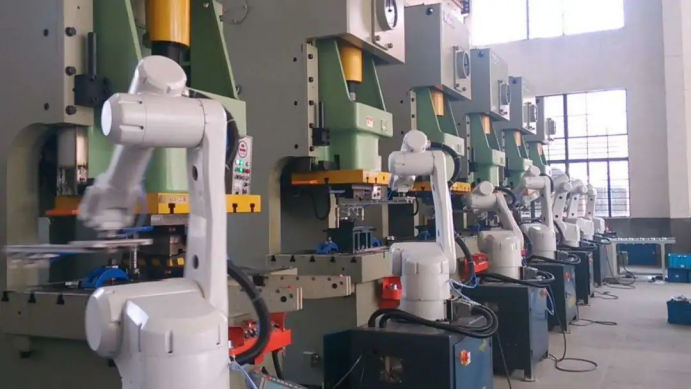
Chassis cabinet bending
The process of forming the required shape by cold pressing the metal sheet with the upper and lower knives of the bending machine is called bending. Due to the complexity of bending, this may be the most difficult step in metal manufacturing of chassis and cabinet sheet metal processing. The engineer must be very familiar with the bending properties of metal.
Most bending machines have certain restrictions on bending:
Unilateral height: the size of the bending machine and the height of the upper tool. The solution can be to bend at large angles on multiple sides.
Double side height: not greater than the maximum height of one side. In addition to all the restrictions on the height of one side, it is also limited by the bottom edge: bending height<bottom edge.
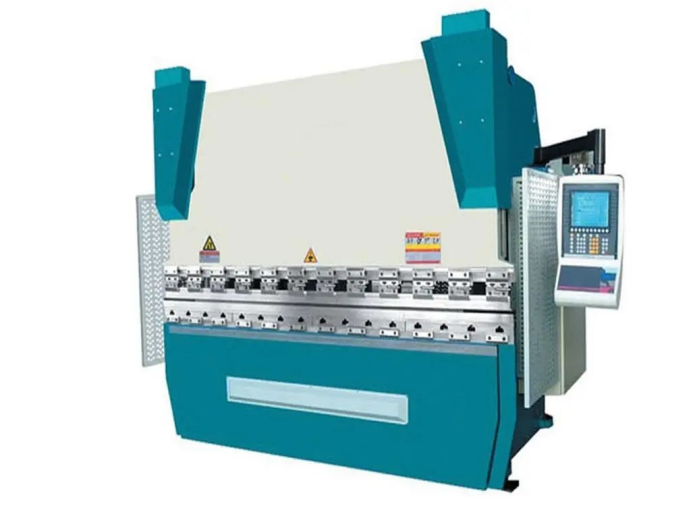
Chassis and cabinet assembly
The assembly of chassis and cabinet is usually the last or penultimate step of product completion. If the assembly includes welding process, the parts of chassis and cabinet must be clean. If the parts have been powder coated, other methods such as riveting and bolting are usually used for assembly.
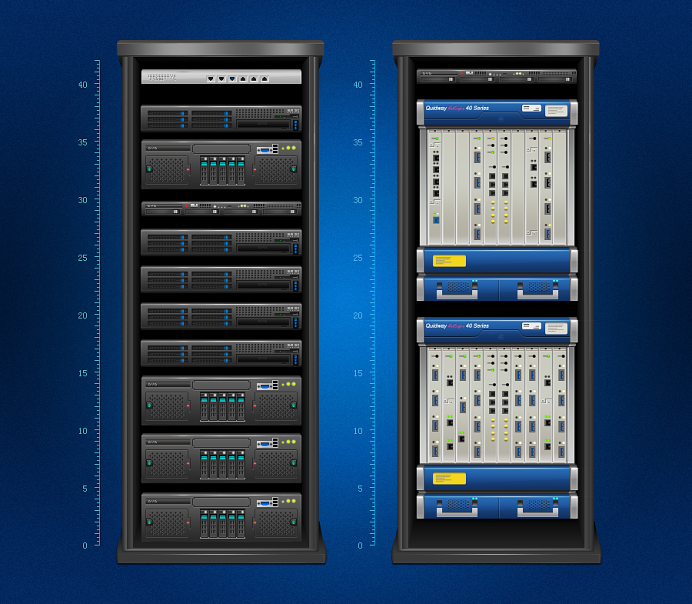
Surface treatment of server cabinet
When there are no special requirements (such as acid environment), electrostatic powder spraying is the preferred surface treatment method for cabinet sheet metal processing. Electrostatic powder spraying: the coating is a small solid particle, which is fed into the spray gun by the powder supply system through compressed air. When the powder is sprayed from the gun nozzle, it forms charged coating particles, which are attracted to the workpiece with opposite polarity by the electrostatic force.
With the increase of powder sprayed, the charge accumulates more. When it reaches a certain thickness, due to electrostatic repulsion, it will not continue to adsorb, thus forming a film with uniform thickness. Then the powder is melted, leveled and solidified by heat, forming a hard film on the surface of the chassis and cabinet.
Because customer requirements and processes are different for sheet metal cabinet processing, and the processes have advantages and disadvantages, we need to consider carefully when placing orders or producing.
In addition to the above processes, sheet metal processing also includes grinding, cutting, bending, spraying, surface treatment, etc. When selecting, you can choose the appropriate sheet metal cabinet processing process according to your own needs, so as to obtain high-quality sheet metal cabinet processing parts.