Mold costs depe…
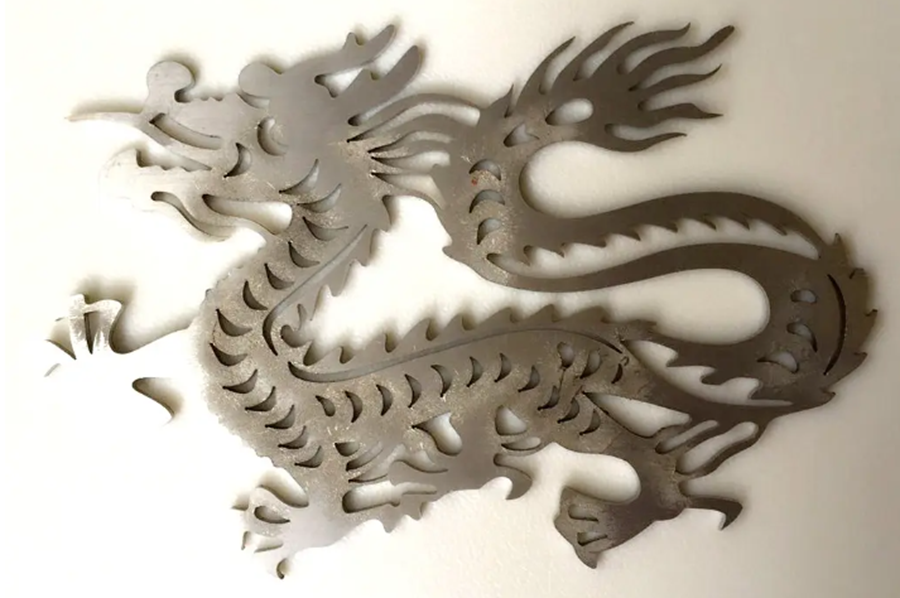
The role of laser processing technology in sheet metal industry
The sheet metal industry is one of the most important application markets of laser processing. The huge potential market in China also provides a broad space for large-scale application of laser processing machine tools in the sheet metal industry. With the intensification of competition, the profit space of each stage of the sheet metal industry chain is being compressed, and the space for price reduction is decreasing. The competition in China’s sheet metal market will turn into the competition of high-quality and high-tech products. In order to comply with the development trend of the international market, the sheet metal processing industry must have the transformation trend of processing technology. As a new process, laser processing technology is the product of modern scientific development. Laser cutting technology, laser welding technology, laser drilling technology and laser forming technology are increasingly used in sheet metal processing.
Sheet metal is a comprehensive cold working process for sheet metal (usually less than 6mm), including shearing, punching/cutting/compounding, folding, welding, riveting, splicing, forming (such as automobile body), etc. Its remarkable feature is that the thickness of the same part is consistent.
Laser cutting machine is a technological revolution in sheet metal processing, and is the “processing center” in sheet metal processing; The laser cutting machine has high flexibility, fast cutting speed, high production efficiency and short production cycle, which has won a wide market for customers. The effective life of this technology is long. At present, most of the plates with a thickness of more than 2mm abroad use laser cutting machines. Many foreign experts agree that the next 30-40 years will be the golden age for the development of laser processing technology. Laser cutting machines are widely used in modern life and production. At present, there are three main types of laser cutting machines: optical fiber laser cutting machines, CO2 laser cutting machines, and YAG laser cutting machines.
China has gradually become an international processing and manufacturing center. With the continuous increase of foreign investment, the demand for metal processing is increasing. In the metal processing industry, electrical control boxes, machine shells, etc. are generally sheet metal parts, so the demand for sheet metal processing capacity is also increasing. As a result, the complexity of the process is relatively high, even some parts have dozens of processes, It also puts forward higher requirements for sheet metal processing in terms of precision.
People say that the optical fiber laser cutting machine is a progress standing on the shoulders of giants. It first started to rise in developed countries abroad, driving the rapid development of its related manufacturing industries. China has begun to catch up in recent years, and has come from behind in the field of optical fiber laser cutting machines. This achievement shortens the gap between China’s high-end manufacturing and foreign high-end equipment manufacturing, and may even enable China’s high-end equipment manufacturing to catch up with the pace of foreign high-end equipment manufacturing technology. Fiber laser cutting machine helps China’s manufacturing industry achieve leapfrog development. In recent years, optical fiber laser cutting machine has been flourishing in the field of sheet metal processing. The laser cutting industry is a main force in the sheet metal industry.
Traditional sheet metal processing process: shearing punching bending welding process or flame plasma cutting bending welding process. In the face of orders with multiple varieties, small batch, customization, high quality and short delivery time, it has obvious shortcomings:
① (CNC) shearing machine can only be used for sheet metal processing that only requires linear cutting because it is mainly used for linear cutting;
② (CNC/brick tower) punch has restrictions on cutting steel plates with a thickness of more than 1.5mm, and the surface quality is poor, the cost is high, and the noise is loud, which is not conducive to environmental protection;
③ As the original traditional cutting method, flame cutting is only suitable for rough machining because of its large thermal deformation, wide kerf, waste of materials and slow processing speed;
④ High pressure water cutting process is slow, causing serious pollution and high cost.
The new sheet metal cutting equipment and process – laser cutting is a technological revolution in sheet metal processing and a “machining center” in sheet metal processing. Laser cutting technology has the advantages of flexibility and high flexibility. In view of the problems existing in the traditional sheet metal cutting at this stage, the demand for laser cutting is also increasing.
The advantages of the new sheet metal cutting process are:
① Laser cutting has the advantages of high flexibility, fast cutting speed, high production efficiency and short product production cycle. No matter simple or complex parts, laser can be used to achieve rapid prototyping cutting at one time;
② Narrow cutting seam, good cutting quality, high degree of automation, simple operation, low labor intensity, no pollution;
③ It can realize automatic cutting layout and nesting, improve the utilization rate of materials, no tool wear, and good material adaptability;
④ The production cost is low and the economic benefit is good.