Mold costs depe…
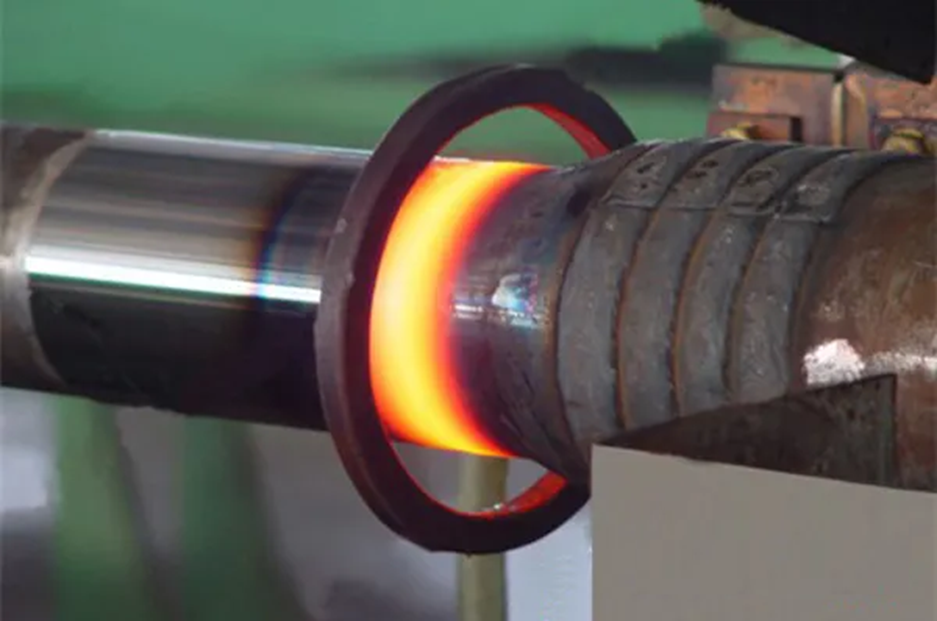
Testing Method for Hardness of Surface Heat Treated Workpieces
The surface heat treatment is divided into two categories, one is surface quenching and tempering heat treatment, and the other is chemical heat treatment. The hardness test methods are as follows:
1. Surface quenching and tempering heat treatment
The surface quenching and tempering heat treatment is usually conducted by induction heating or flame heating. The main technical parameters are surface hardness, local hardness and effective hardened layer depth. The Vickers hardness tester, Rockwell or Superficial Rockwell hardness tester can be used for hardness testing. The selection of test force (scale) is related to the effective hardened case depth and workpiece surface hardness. Three types of hardness testers are involved here.
Vickers hardness tester is an important means to test the surface hardness of heat treated workpieces. It can use a test force of 0.5~100kg to test the surface hardened layer as thin as 0.05mm. Its accuracy is the highest, and it can distinguish the small difference in the surface hardness of heat treated workpieces. In addition, the effective depth of the hardened layer is also measured by a Vickers hardness tester. Therefore, it is necessary to equip a Vickers hardness tester for units that perform surface heat treatment or use a large number of surface heat treated workpieces.
The surface Rockwell hardness tester is also very suitable for testing the hardness of surface quenched workpieces. There are three scales for the surface Rockwell hardness tester to choose from. Various surface hardened workpieces with effective hardening depth exceeding 0.1mm can be tested. Although the accuracy of the surface Rockwell hardness tester is not as high as that of the Vickers hardness tester, it can meet the requirements as a testing method for quality management and qualification inspection in the heat treatment plant. Moreover, it also has the characteristics of simple operation, convenient use, low price, rapid measurement, direct reading of hardness value, etc. The surface Rockwell hardness tester can be used for rapid and nondestructive inspection of batches of surface heat treated workpieces piece by piece. This is of great significance for metal processing and machinery manufacturing plants.
When the hardened layer of surface heat treatment is thick, Rockwell hardness tester can also be used. When the thickness of heat treatment hardening layer is 0.4~0.8mm, the HRA scale can be used; when the thickness of hardening layer exceeds 0.8mm, the HRC scale can be used.
Vickers, Rockwell and surface Rockwell hardness values can be conveniently converted to the hardness values required by standards, drawings or users. The corresponding conversion tables have been given in the international standard ISO, American standard ASTM and Chinese standard GB/T. These three conversion tables can be found in the technical information column of Shenyang Tianxing website.
2. Chemical heat treatment
Chemical heat treatment is to infiltrate atoms of one or several chemical elements into the workpiece surface, thus changing the chemical composition, structure and properties of the workpiece surface. After quenching and low temperature tempering, the surface of the workpiece has high hardness, wear resistance and contact fatigue strength, while the core of the workpiece has high strength and toughness.
The main technical parameters of chemical heat treatment workpiece are the depth of hardened layer and surface hardness. The depth of hardened layer shall be tested by Vickers hardness tester. Detect the distance from the workpiece surface to the point where the hardness drops to 50HRC. This is the effective hardening depth
The surface hardness test of chemical heat treated workpieces is similar to that of surface quenched heat treated workpieces, which can be tested by Vickers hardness tester, surface Rockwell hardness tester or Rockwell hardness tester. However, the nitriding thickness is relatively thin, generally no more than 0.7mm, so Rockwell hardness tester can no longer be used.
3. Local heat treatment
If the local hardness of parts is required to be high, local quenching heat treatment can be carried out by means of induction heating, etc. Such parts usually need to be marked with the location and local hardness value of local quenching heat treatment on the drawing. The hardness test of parts shall be carried out in the designated area. Rockwell hardness tester can be used to test HRC hardness value. If the heat treatment hardening layer is shallow, surface Rockwell hardness tester can be used to test HRN hardness value.
History of Heat Treatment Technology
1. Ancient heat treatment
Material heat treatment has a long history in China. Compared with other regions in the world, the development of ancient heat treatment technology in China has obvious regional characteristics. In some aspects, China’s heat treatment technology lags behind other regions, but there are also many inventions and technologies that are far ahead in the history of world heat treatment. Many of these achievements have also spread to all parts of the world, playing a direct role in promoting the progress of world heat treatment technology.
The development of material heat treatment technology in China is similar to other technologies. The traditional heat treatment technology has experienced a process from germination, establishment, development, prosperity to decline, and finally the introduction, digestion and development of modern technology. Referring to the stages in ancient China, we can think that in ancient times, the heat treatment in China began to sprout, and in ancient times, the traditional heat treatment technology in China began to be initially established; In the Middle Ages, China’s traditional heat treatment technology was further developed; In recent ancient times, China’s traditional heat treatment technology reached its peak. In modern times, China’s traditional heat treatment technology gradually weakened, while modern technology began to establish and develop.
2. Progress in modern heat treatment
Heat treatment is a very important basic process in the machinery industry, which plays an important role in improving the internal quality and service life of mechanical and electrical products and strengthening the competitiveness of products in domestic and foreign markets. But it took a long time and a great price to realize this. Because heat treatment affects the internal quality of the product, it generally does not change the shape of the product, does not make people intuitively feel its necessity, and it will be seriously distorted and cracked if it is not properly done; Destroy the surface quality and dimensional accuracy of the products, resulting in the abandonment of previous achievements in the manufacturing process. Therefore, there has been a long-term phenomenon of “heavy cold (cold processing) light hot (hot processing)” in China’s manufacturing industry, so that this industry has been in a backward state.
Due to the weakness of the industrial base and the damage suffered in the war, the heat treatment in China in the 1940s was only a workshop type production and had not yet formed a substantive industry. There is no special subject of heat treatment in engineering colleges and universities, so there is a lack of high-level professional and technical personnel. At that time, most of the heat treatment operations were family skills, shrouded in a mysterious atmosphere, and were in a very backward position.
China’s heat treatment industry originated from 156 enterprises aided by the Soviet Union in the early 1950s. The mechanical plants are equipped with heat treatment workshops and sections. We have purchased a large number of Soviet made heat treatment equipment, including box type, well type, salt bath and other resistance heating furnaces of the 1930s and 1940s, and established the first batch of electric furnace plants to produce these types of equipment according to Soviet drawings. Some engineering colleges and universities have established the heat treatment specialty included in the mechanical manufacturing technology department after the adjustment of the colleges and departments, and trained the first batch of formal graduates of the heat treatment specialty from 1954 to 1956. In the late 1950s and early 1960s, there were also a group of international students studying heat treatment from the Soviet Union. Some scientific research institutions and colleges established in succession can basically carry out the research and development of heat treatment foundation and application technology in accordance with the pace of material and application development, and a series of scientific research achievements have emerged. As a result, a relatively complete professional system has been initially formed in terms of personnel training, research and development, production technology innovation and equipment manufacturing.
Due to the disjunction between scientific research and production application, the neglect of the innovation of production equipment and the short-term vision caused by long-term isolation, the heat treatment production technology of mechanical and metallurgical plants in the 1960s and 1970s did not show significant progress. Until the 1980s, communication with the international community was realized, and advanced technology and equipment were introduced. The production technology of some large backbone enterprises had significantly improved.