Mold costs depe…
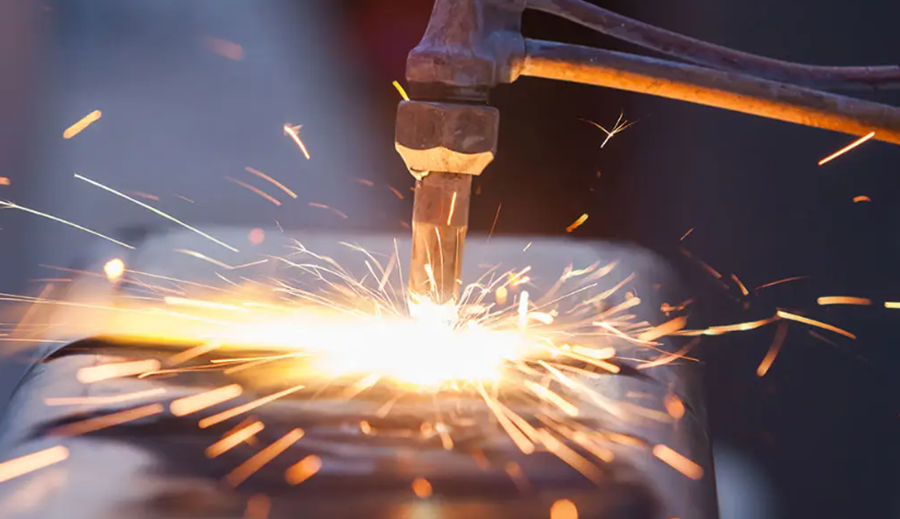
Super complete welding knowledge (I)
1. Brazing
The energy source of brazing can be either chemical reaction heat or indirect heat energy. It uses a metal with a melting point lower than the melting point of the material to be welded as the filler metal. After heating, the filler metal is melted. The capillary action moves the filler metal into the gap of the joint contact surface, wets the surface of the metal to be welded, and makes the liquid phase and solid phase mutually diffuse to form a brazed joint. Therefore, brazing is a solid and liquid phase welding method.
Characteristics and Application of Brazing
The alloy with a melting point lower than that of the base metal is used as the filler metal for brazing. When heated, the filler metal melts and is filled and kept in the joint gap by wetting and capillary action. While the base metal is in solid state, the brazing joint is formed by mutual diffusion between the liquid filler metal and the solid base metal. Brazing has little impact on the physical and chemical properties of the base metal, and the welding stress and deformation are small. The dissimilar metals with large differences in weldability can complete multiple welds at the same time. The joint appearance is beautiful and neat, the equipment is simple, and the production investment is small. However, the strength of the brazed joint is low and the heat resistance is poor.
Applications: carbide tools, drilling bits, bicycle frames, heat exchangers, conduits and various containers; Brazing is even the only possible connection method in the manufacture of microwave waveguides, electronic tubes and electronic vacuum devices.
Solder and flux
The filler metal is the filler metal for forming the brazed joint, and the quality of the brazed joint depends on the filler metal to a large extent. The filler metal shall have proper melting point, good wettability and joint filling ability, be able to diffuse with the base metal, and have certain mechanical properties and physical and chemical properties to meet the service performance requirements of the joint. According to the different melting points of filler metals, brazing can be divided into two categories: soft soldering and brazing.
① Soldering: Soldering with the melting point of filler metal below 450 ℃ is called soldering. The common filler metal is tin lead filler metal, which has good wettability and conductivity and is widely used in electronic products, electric motors and automobile accessories. The joint strength of soft soldering is generally 60~140MPa.
② Brazing: Brazing with the melting point of filler metal higher than 450 ℃ is called brazing, and the commonly used filler metals are brass filler metal and silver based filler metal. The joints using silver based solder have high strength, conductivity and corrosion resistance. The solder has low melting point and good processability, but the price of solder is high. It is mostly used for weldments with high requirements. Generally, brass solder is used for weldments. Brazing is mainly used for brazing of steel and copper alloy workpieces with large force and tools. The joint strength of brazing is 200 ~ 490MPa,
be careful:
The contact surface of base metal shall be clean, so soldering flux shall be used. The function of brazing flux is to remove oxides and oil impurities on the surface of base metal and brazing filler metal, protect the contact surface between brazing filler metal and base metal from oxidation, and increase the wettability and capillary fluidity of brazing filler metal. The melting point of the flux shall be lower than that of the filler metal, and the corrosion of the flux residue on the base metal and joints shall be less. The commonly used brazing flux is rosin or zinc chloride solution, and the commonly used brazing flux is a mixture of borax, boric acid and basic fluoride.
According to different heat sources or heating methods, brazing can be divided into flame brazing, induction brazing, furnace brazing, immersion brazing, resistance brazing, etc. As the heating temperature is relatively low during brazing, it has little influence on the properties of the workpiece material, and the stress and deformation of the weldment are also small. However, the strength of brazed joints is generally low and the heat resistance is poor.
Brazing heating method: almost all heating sources can be used as brazing heat sources, and brazing can be classified according to this.
① Flame brazing: heated by gas flame, used for brazing carbon steel, stainless steel, hard alloy, cast iron, copper and copper alloy, aluminum and aluminum alloy;
② Induction brazing: resistance heating weldments using alternating magnetic field to generate induction current in parts, used for weldments with symmetrical shape, especially for brazing of pipe shafts;
③ Immersion brazing: immerse the weldment partially or wholly into the molten salt mixture or filler metal melt, and realize the brazing process by the heat of these liquid mediums, which is characterized by rapid heating, uniform temperature, and small deformation of the weldment;
④ Brazing in furnace: the weldment is heated by a resistance furnace, which can protect the weldment by vacuuming or using reducing gas or inert gas.
In addition, there are soldering iron brazing, resistance brazing, diffusion brazing, infrared brazing, reaction brazing, electron beam brazing, laser brazing, etc.
Brazing can be used to weld carbon steel, stainless steel, superalloy, aluminum, copper and other metal materials, and can also connect dissimilar metals, metals and nonmetals. It is suitable for welding joints under low load or at normal temperature, especially for precision, micro and complex weldments with multiple brazing seams.
2. High frequency welding
High frequency welding takes solid resistance heat as energy source. During welding, the resistance heat generated by high-frequency current in the workpiece is used to heat the surface layer of the welding area of the workpiece to the molten state, and then the upsetting force is applied (or not applied) to achieve metal bonding. Therefore, it is a solid resistance welding method.
High frequency welding can be divided into contact high frequency welding and induction high frequency welding according to the way that high frequency current generates heat in the workpiece. When contacting high-frequency welding, high-frequency current is transmitted to the workpiece through mechanical contact with the workpiece. In induction high frequency welding, the high frequency current generates induction current in the workpiece through the coupling effect of the external induction ring of the workpiece. High frequency welding is a highly specialized welding method, and special equipment shall be provided according to the product. High productivity, welding speed up to 30m/min. It is mainly used for welding the longitudinal seam or spiral seam when manufacturing pipes.
3. Explosive welding
Explosive welding is another solid state welding method using chemical reaction heat as energy source. But it uses the energy generated by explosive explosion to realize metal connection. Under the action of the explosion wave, the two metals can be accelerated and impacted in less than a second to form metal bonding. Among various welding methods, explosive welding can weld the widest range of heterogeneous metal combinations. Explosion welding can be used to weld two metals that are incompatible in metallurgy into various transition joints. Explosive welding is usually used to cover flat plates with large surface area, which is an efficient method to manufacture composite plates.
4. Ultrasonic welding
Ultrasonic welding is also a solid state welding method using mechanical energy as energy source. When ultrasonic welding is carried out, under low static pressure, the high-frequency vibration from the sound electrode can make the joint surface produce strong crack friction and heat to the welding temperature to form a joint. Ultrasonic welding can be used for the welding between most metal materials, and can realize the welding between metals, dissimilar metals and metals and nonmetals. It can be applied to the repeated production of metal wire, foil or sheet metal joint of 2~3mm or less.