Mold costs depe…
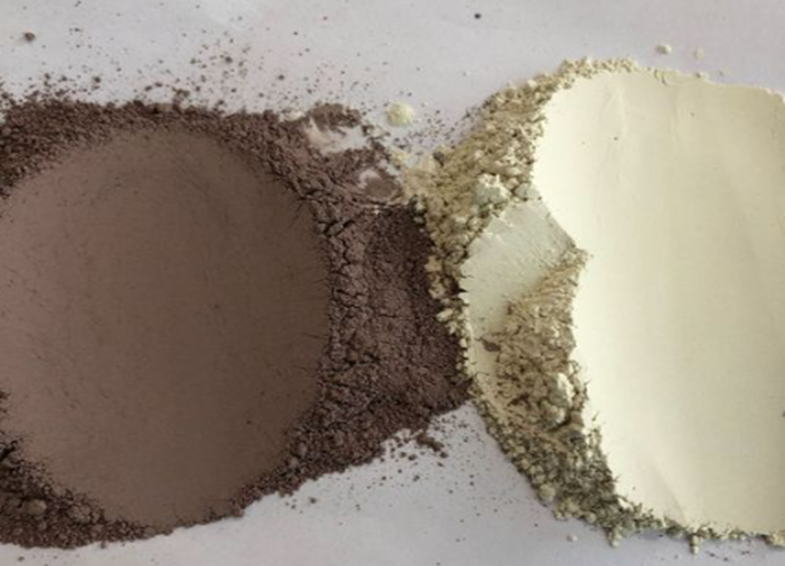
Summary of ten solutions to casting coating problems
What to do if the paint strength is insufficient?
There are two cases of insufficient coating strength: one is the normal drying strength, the other is the strength after high temperature washing. The two cannot be replaced. The normal drying strength is high ≠ the high temperature strength, and accidents will occur if misunderstood.
1. There are three reasons for insufficient drying intensity
First, the performance of additives is insufficient; second, the amount of additives is insufficient; third, there is a problem with aggregate powder. The former two are easy to understand, while the latter may not be universally and truly understood. The following focuses on the problem of aggregate powder.
① The same coarse and fine aggregate powder will affect the strength of the coating after drying, and the best selection range is 180~250 meshes.
② The strength of lightweight aggregate powder (with light specific gravity) is often not as high as that of larger aggregate powder, because the coating density formed by it is slightly poor, and its volume and coverage are obviously different under the same weight.
③ Some aggregate powder will seriously weaken the dry strength of the coating because it contains some harmful elements, such as CaO, MgO, and even some inexplicable ingredients. The larger the content is, the lower the coating strength will be, and the longer the slurry is stored, the more obvious the strength will be.
2. Insufficient high temperature strength due to poor additive performance
Almost all the casting coatings commonly used in the world have a fatal commonality – they can not withstand the high temperature scouring for a long time, and they can not withstand the temperature above 1600 ℃ for more than 40 seconds, so what kind of ceramic pipe runner is used. The real solution to this problem is not the refractoriness of aggregate powder, but the key lies in the high temperature strength of additives: Guilin No.5 coating, which is 1~2mm thin, can be scoured for a long time at 1600 ℃ or above. The strength is not only unchanged, but also the higher the temperature is, the stronger the harder it is. This is called high temperature vitrification, which is better than the high temperature performance of ceramic tubes.
What if there are bubbles in the paint slurry?
Bubbles are produced for the following reasons – if the cause is unknown, wars will be fought:
① There are components in the coating that produce bubbles through chemical reaction, such as olivine powder and bauxite containing CaO, etc
② Paint slurry is easy to ferment and generate bubbles. Such bubbles are due to the fact that additives have no antiseptic ability and the additives themselves produce bacteria in the water and ferment
③ Improper mixing operation causes that the gas in the gap of additive powder cannot be discharged and bubbles are generated
Solution – understand the source of bubbles, and the direction of elimination is simple:
① The aggregates containing many harmful substances such as CaO should be used with caution – they should be soaked with water first and then mixed with additives
② All kinds of “composite additives” without anti-corrosion ability shall be used with caution or not. Guilin No.5 Yimatong additive does not contain any chemical preservatives, but the prepared paint slurry will not ferment even if it is kept for a month in a hot summer day. This is another major invention of Professor Liu Yuman who overcame an international problem in 2013.
③ “Thick” stirring is very helpful to eliminate bubbles. Thick mixing is similar to rolling, which is essentially to increase the friction and extrusion between the wetted powder particles (clusters), so as to strengthen the wetting of water to the powder. If the powder is 100% saturated, there is no gas hiding place. When it is completely stirred evenly, add water to adjust the required concentration, and it is not easy to retain bubbles in the slurry. In case of “thin” stirring, once the additive and water form a colloid first, the gas in the “powder” cannot be discharged.
The slurry is colloidal, and a large bubble of mung bean is surrounded by a colloid with high adhesion. It is not easy to talk about how the antifoaming agent can break through the “colloid” to get the small bubbles out. The paint slurry is non Newtonian fluid, so don’t do such useless work, and the antifoaming agent stinks. The so-called defoamer introduced in many articles is nothing more than n-butanol, n-amyl alcohol and the like. Adding it to the paint slurry can not defoamer, but it seriously deteriorates the performance of the paint, and there is a highly irritating odor. The use of the so-called defoamer should not go astray.
What should I do if the paint cracks after drying?
In addition to the poor strength and crack resistance of additives, which can not overcome the drying shrinkage, there are several other factors worth noting:
① The aggregate powder is too fine or the harmful ingredients are excessive (such as bauxite raw materials, etc.)
② The shrinkage rate of aggregate powder soaked with water is too large when drying (such as bentonite)
③ The drying temperature is not stable (for example, it is shady and cool when exposed to the sun)
④ The thickness of the coating is very different (for example, the corner is very thick, while the straight faces on both sides are very thin, which is similar to the hot spot shrinkage crack of the casting)
⑤ The foam is not fully matured and deformed for three times during drying
⑥ Too fast hot air flow leads to the difference of drying stress in various parts (such as strong wind under the hot sun or high temperature and strong convection in the drying room)
Anti crack measures:
① Improve the crack resistance of additives (such as increasing the content of crack resistant fiber)
② Reduce the shrinkage of additives (adjust the formula reasonably)
③ The aggregate powder shall not be too fine or the air permeability shall not be too low
④ The temperature in the drying room is balanced, and the utilization of solar energy should not be simplified
⑤ The slurry at the corner of the white mold shall not flow too much and too thick (soft brush treatment or change the slurry flow direction)
⑥ The white mold must be fully dried and matured
⑦ The drying temperature shall be controlled below 60 ℃
⑧ If necessary, 2-3% silica sol can be added to increase crack resistance
⑨ Do not randomly select unknown additives, adhesives and other materials
What if the paint doesn’t hang?
If the mold is not hung, the coating performance is poor. The causes of poor coating performance should be investigated from various aspects:
① The coating additive itself has poor coating performance, which is easily accepted;
② The same additive, such as coarse mesh of aggregate, must have poor coating performance;
③ For the same additive and aggregate, too thin concentration will inevitably lead to poor coating performance;
④ For the same aggregate mesh but different aggregate specific gravity, it is inevitable that the coating property is poor when the aggregate ratio is significant;
⑤ The paint should be used in the agitated or flowing state, and the coating performance of the paint in the static state after a long time is necessarily worse than that in the flowing or stirring state;
⑥ The coating that has been fermented and deteriorated for a long time or dehydrated and layered must have poor coating performance.
Therefore, when the coating coating is not ideal, first investigate the reason and then make countermeasures. Don’t make a vague conclusion, and then make a vague adjustment. It may be worse if you make more adjustments.
In terms of the specific gravity of aggregates, many people neglect or one-sided understanding. For example, the specific gravity of Baozhu sand is 4~4.2g/cm3, while the specific gravity of quartz powder is only 2.2~2.4 g/cm3. Obviously, if Baozhu sand powder accounts for 100% of the aggregate powder, the result must be very poor coating performance. Therefore, it is appropriate that the proportion of Baozhu sand does not exceed 35% when preparing coatings.
One misconception that we should not fall into is our understanding of Baumedo. Baume degree=144.3-144.3/d, where d is the density of paint slurry. Different aggregate powders or different meshes of the same aggregate powder have completely different water adaptability, so different Baume degrees must be obtained. Therefore, each factory has its own Baume degree, and there is no unified parameter. Do not follow suit, let alone mislead.
What about paint dehydration (desizing)?
Paint dehydration refers to the “shrinkage dehydration” of paint slurry, also known as “slurry separation”. Its manifestation is the precipitation of a layer of water on the surface of paint slurry or on the interface between the paint slurry and the wall of the material pool.
Dehydration reason:
The main reason is that the suspension system of the coating is unstable, and the volume of its own reticular cementitious structure shrinks after being placed for a period of time. In particular, the coating with a large amount of sodium based bentonite is more prone to this dehydration and desizing phenomenon.
terms of settlement:
① The composition of coating components shall be strictly controlled, and components such as sodium bentonite shall be used less or not. Many articles recommend that sodium bentonite be used as suspension agent, which is one-sided. Most sodium bentonite is composed of soda ash and ordinary bentonite, which is not natural sodium base. The anti dehydration effect of attapulgite added in the coating is better.
② Improve the powder to liquid ratio of the coating and appropriately increase the concentration
③ Reduce the proportion of excessive density appropriately
④ The particle size of aggregate powder should not be too coarse
⑤ Add a small amount of appropriate activator to improve the dispersion of aggregate
⑥ Dehydrated coatings are often prone to “water breaking” (flow ditch) defects during coating and hanging. When dehydration is serious, they should be stirred in time and used in the mixed state, or used as soon as possible after adding appropriate components and adjusting properly, instead of being left for a long time. The paint with excessive slurry separation and dehydration should not be used. A certain amount of additives should be added to make it qualified before use. If it has deteriorated, it should be scrapped.
What should I do if the coating is not shelled after cleaning?
According to the traditional theory, there are two conditions for coating shelling: one is that the inner coating does not adhere to sand (chemical sand, thermochemical sand, mechanical sand – permeable sand), and the other is that the entire coating can be sintered into hard chips.
Professor Liu Yuman has put forward a new coating theory – porcelain coating at high temperature, which is an innovation and development of the coating sintering theory.
According to the traditional theory, excessive FeO on the surface of molten steel seeps into the coating layer to reduce and improve the sintering degree of the coating layer, forming a “Guoba layer”. For the reduced aggregate coating, it is not easy to produce excessive FeO on the surface of molten iron, so it cannot be sintered into a “pot layer”, and it cannot be shelled in pieces. Professor Liu’s research and invention is that the addition of additives can make the coating ceramic rapidly above 1000 ℃, so as to form a shellable hard chip. This additive is the replacement product of Guilin No.5 produced by Zhongnan Casting and Metallurgy since August 2013.
The new generation of Guilin No.5 is used to produce steel castings. Even if the aggregate powder is 100% quartz powder, it can be ideal for shelling. The use of “modified quartz powder” is obviously more beautiful.
According to the traditional theory, it is extremely difficult to shelling in pieces when either quartz powder or graphite powder with the strongest sand resistance is used as aggregate, because graphite powder does not sinter at high temperature. When a new generation of Guilin No.5 is used in combination with graphite powder, a little addition of quartz powder can realize high-temperature ceramic self shelling, or graphite powder is used for the inner aggregate, and quartz powder is used for the outer layer, then composite ceramic chips are formed inside and outside at high temperature, which is very easy to shelling, which is the secret of ceramic automatic shelling of the coating layer.
Whether it is an ideal sintered layer or a high temperature ceramic layer, the same prerequisite is required if the surface does not self desquamate – the inner layer of the coating is free of sand, so the scientific selection of additives and aggregate powder in the inner layer cannot be ignored.
Serious scouring and sand sticking at the gate interface of coating patching
First of all, it should be clearly pointed out that it is absolutely wrong to coat the interface with water paint (or cement bar) when packing, and it is not allowed. Otherwise, when pouring high temperature molten steel here, it must produce “water vapor” explosion, which will cause the coating to crack or loosen and wash. Once the gap is broken, the molten steel will directly wash the dry sand layer, which is really like a mountain of defeat, and there must be a lot of sand holes in the casting.
The runner, such as the throat, is the only channel for molten steel to enter the mold cavity, and it has the highest temperature, the longest scouring time, and the greatest impact. Therefore, no matter what is used to repair the bonding interface of the runner, the first runner should be coated with a coating that can withstand long-term high-temperature scouring. For example, although Guilin No.5 coating is 1~2mm thin in thickness, even 3~5t castings do not need a ceramic runner at all. On the premise that the entire runner is resistant to high temperature and scouring, the bonding interface during packing must be patched with porcelain based coating paste (mud like) with the same high temperature resistance, and it is not allowed to simply and conveniently use cement to casually wipe things off.
Many people mistakenly believe that “the adhesives in alcohol based fast drying coatings, such as resin and rosin, are not resistant to high temperature, and they will be easily washed off if they are repaired”. The various alcohol based coatings on the market really use resin and rosin as the binder, and the high-temperature molten steel melts quickly. This alcohol based coating cannot be used to patch the gate. On the contrary, Guilin No.5 porcelain based alcohol based coating can rapidly harden and porcelain in a few seconds under high temperature. The so-called porcelain transformation is a ceramic transformation, which becomes as resistant to high temperature and erosion as ceramic flakes. The usage of this alcohol based coating is very simple: 100g of alcohol based No. 5 powder+1000g of aggregate powder+300g of alcohol with a concentration of about 90%, mix and stir it into a muddy shape and smear it on the interface.
What if the coating bulges and falls off easily?
The coating bulge is often the size of a fingernail or larger area, which often occurs after the last layer of paint is brushed and dried, and it is easy to touch and fall off. Why does this happen? How to solve it?
This phenomenon is mostly due to operation problems. The root cause is that when the first layer of coating is applied, the slurry fails to fully soak with the white mold surface, and the gas in the micro grooves on the white mold surface cannot be fully removed. During the drying process, the gas in the micro grooves is heated and agglomerated to expand. Since the first layer of coating is very thin and can be breathable, there is often no obvious bulge phenomenon. However, the second or third layer is different. When the second or third layer is applied, the water seeps to the first layer, while the gas in the groove below the first layer still exists. After the third layer is applied, the coating thickness increases, and the drying degree of the inner and outer layers is different. The slurry of the outer layer first forms a film in the drying room, while the inner layer is still wet. At this time, the permeability is the worst. After the inner layer is wetted by the water penetrated from the outer layer, The adhesion with the white mold is also the weakest. At this time, when the gas under the inner layer expands when heated, it will bulge the local (fingernail size) coating (about 1-2 mm), which is the root cause of the “blister”.
Of course, the source of “air blowing” has a lot to do with the amount and type of release agent remaining on the white mold surface. Its existence itself weakens the permeability and adhesion of the paint slurry, and it is easy to volatilize when heated to produce gas, which is often ignored.
terms of settlement:
① The first layer of paint must rub with the white mold surface as much as possible – hand friction, repeated spraying, brushing, flow state dipping, etc. are effective.
② For the phenomenon that the white mold surface is polluted by release agent, it is advisable to wipe the white mold surface with detergent or alcohol.
③ Properly improve the adhesion and permeability of the coating, and it is effective to add 2-3% silica sol. It is easy to find out the cause of its formation and the source of qi, and eliminate it. This phenomenon is common throughout the country, but it is not difficult to solve it.
What should I do if pinholes appear in the paint layer?
Pinholes are different from bubbles. Bubbles usually refer to “bubbles” larger than 1mm, and pinholes (pinholes) refer to micropores smaller than 1mm. Pinholes in the coating layer are usually 0.5~1mm, which affect the compactness of the coating and the surface roughness of the casting.
Causes of pinholes:
① Chemical reaction between relevant components in the coating produces micro gas
② The powder is not fully wetted by water, and there is gas adsorbed in the surface grooves or internal micropores that is closed by the coating slurry colloid. When the slurry is left standing for a certain period of time, it will aggregate into micro “bubbles”, leaving micropores when drying.
③ When the white mold is dipped and coated, the speed is too fast. The gas adsorbed on the rough white mold surface cannot be discharged in time and is dispersed under the slurry coating, forming micropores during the drying process
④ Air is drawn into the slurry due to improper operation during coating mixing
Pinhole elimination method:
① Quick dipping and insufficient friction between the paint slurry and the white mold surface are common overlooked operation mistakes, which can be called “jerry building”
② High speed mixing — quick, too high baking temperature — quick, fast, not good, otherwise
③ Three kinds of aggregates that are easy to produce micropores should be used with caution: bauxite (with micropores inside), forsterite powder (not only with micropores but also with a small amount of CaO), and kaolin are also similar to bauxite after calcination. If these aggregates are selected, first of all, the proportion should be appropriate. Second, it is better to soak them with water for a period of time before mixing. Before the formation of the slurry colloid, the gas in the micropores should be discharged so that CaO can fully react with water.
The coating layer falls off in wet state during drying
The coating layer falls off in wet state in drying process in some units, especially the thicker the coating is, the more likely it is to fall off in wet state. The first layer falls off rarely, and the second or third layer falls off frequently. Obviously, it is the gravity of the coating itself that exceeds its adhesion to the surface of the white mold that causes the flakes to fall off, and it is completely certain that the white mold falls off at the part with the plane facing down, not the coating on the upper surface.
In this case, the following operations should be corrected:
① After the coating is dried and thickened, do not immerse the pattern in the slurry tank again