Mold costs depe…
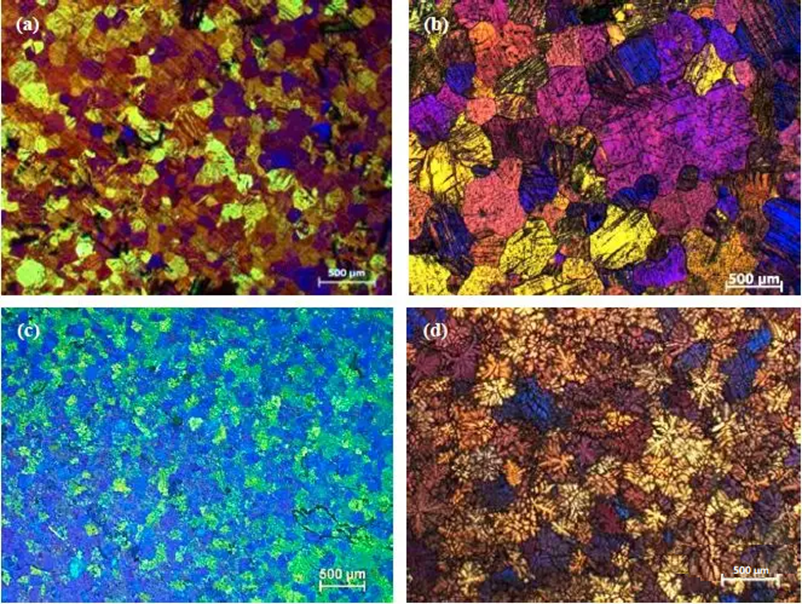
Summary of Measures to Solve the Coarse Grain of Castings
The casting grain coarseness refers to the defect that shows the grain structure is too coarse to be suitable for application when the machinist or the fracture inspection is carried out. This kind of coarse grain structure may be distributed throughout the whole casting, or may occur locally. In essence, coarse grain defect is a metallurgical defect. Based on many years of production practice and referring to relevant information, the author talks about the causes of coarse grain defects in castings and preventive measures.
1 Casting structure and process design
(1) If the section difference of the casting is too large, the grains in the thicker section will be coarse due to slow cooling. Metals such as gray cast iron, which are very sensitive to changes in cross section, are more likely to produce such defects. The effective way to prevent such defects is to avoid excessive disparity of casting section size, which is sometimes beyond the power of the casting workers. Therefore, in terms of the casting itself, the occurrence of such problems can be reduced and the severity of such defects can be reduced by setting the chill, controlling the pouring temperature or selecting the appropriate pouring system. The cooling rate of the thicker section of the casting can be accelerated by using cold iron; If the pouring temperature is too high, this kind of problem will be more serious and should be avoided; By adjusting and modifying the design of the gating system, the molten metal with low temperature is located at the thicker section of the casting, and the most effective riser is designed at the thick section of the casting to minimize the size of the riser.
(2) For castings with holes, the process designer sometimes fails to use the core that can reduce the effective section size, so that the section without core is too thick, which causes this defect. Therefore, during the process design, sand cores should be set in the thicker section as much as possible.
(3) In some cases, the casting section is not too thick, but because a narrow depression or core forms a heat sink section in the casting, the result is the same as that of a thick section. For example, a core may need to be set at a columnar umbilical in the deeper part of the casting, which will cause slow cooling. If the design cannot be modified, the best solution is to set cold iron at the core or mold section, unless the metal temperature can be reduced or the gate can be replaced.
(4) Excessive machining allowance in process design not only increases the cost of cutting, but also cuts off the surface layer of the denser casting and exposes the loose part with slower central cooling. This design has no merit because it is unreasonable from the perspective of casting or machining. The solution is to change the design of castings. If it is not allowed to change the design, the correct method is to use cold iron, control the pouring temperature and adjust the pouring system.
(5) Improper core design at the thick section, incorrect core support, or other technologies that cause core deflection will cause changes in the casting section, resulting in coarse grains.
2 Gating and riser system
(1) Failure to achieve sequential solidification The gating system fails to achieve sequential solidification well, which is usually the cause of coarse grains. For castings with sharp section changes, attention must be paid to the number and location of ingates. For feeding, keeping hot molten metal in the action zone of the riser will reduce the cooling rate of the thick section to the extent of producing coarse grains. Improper riser design, such as too long riser neck, improper riser pad design, or too large riser size, will cause excessive heat collection at the thicker section.
(2) Similarly, in order to feed the thick section, excessive heat collection is often caused in local areas. For example, because the side riser will cause overheating of the thick section and slow down the cooling rate, it is sometimes not convenient to use in actual operation. In actual production, it is necessary to reduce the size of the riser as much as possible through reasonable riser design.
(3) The short inner gate or riser neck of local hot spot caused by the connection between the inner gate or riser and the casting is beneficial to feeding, but it will make the runner or riser too close to the casting and slow down the cooling speed of this part. Increasing the neck of riser will bring problems to feeding. Therefore, the best measure is to take effective riser design, reduce the size of the riser as much as possible, and prevent the runner and riser from being too close to the key section that is easy to form coarse particles. The runner and riser are properly set to achieve feeding.
(4) The number of internal gates is insufficient. The number of internal gates is too small, which is not only easy to cause sand washing, but also can cause local hot spots and coarse grain structure. This phenomenon generally exists in all cast metals, even for aluminum alloys with low pouring temperature. In some cases, shrinkage defects may occur due to too few gates. This shrinkage porosity defect may cover up the defect of coarse grains caused by the same reason. In fact, when the coarse grain defect seriously deteriorates, it becomes a shrinkage defect. Therefore, the prevention measures for these two defects are often the same.
3 Molding sand
Only when the displacement of mold wall caused by molding sand is enough to increase the section size of the critical section (the section easy to form coarse grains), the mold fineness is a factor causing coarse grain defects. As the mold wall movement at the thick section may be the largest, this kind of defect may still occur. At this time, the coarse grain defect is related to sand expansion.
4 Core making
Oil sand cores that are not thoroughly baked or air hardened should be avoided in production, because such cores may produce exothermic reactions, resulting in excessive heat collection. This may occur in large castings or in thick and large cores with exothermic adhesives. In a sense, this core acts as an efficient insulator and slows down the cooling rate of the molten metal to a dangerous level.
5 Shape
(1) The lack of vent that can accelerate the cooling rate As for the thicker casting section, the cooling rate of the casting is related to the rate of heat dissipation through the molding sand. The sufficient exhaust will help the water vapor to be discharged quickly, thus producing a cooling effect.
(2) The failure to set cooling nails or cold iron is usually caused by carelessness.
6 Chemical composition
In essence, the coarse grain size and the chemical composition of the metal are related to the coordination of the cooling rate, so it is very important to choose this coordination. If the cooling rate is difficult to adjust, the coarse grain structure must be due to the improper chemical composition of the metal. Due to the importance of metal composition, each metal is briefly described as follows.
(1) Grey iron and malleable iron
If the carbon equivalent is too high, the mathematical calculation of carbon and silicon effects can generally be summarized as: CE=C+1/3Si. The coarse grains may be caused by excessive carbon or silicon, or excessive carbon and silicon. Compared with silicon, the effect of carbon is three times that of silicon, so the change of carbon is much more dangerous than the same change of silicon. This effect of carbon and silicon affects both malleable cast iron and gray cast iron. For malleable cast iron, the coarse grains do not appear as black or pock marks representing primary graphite, but in the form of general coarse grains, which is due to the high content of carbon or silicon, or both. Phosphorus also affects the grain size. When wp=0.1%, it will aggravate the shrinkage cavity defect, especially the coarse grain defect at the section with slow cooling.
(2) Cast steel
In the melting and deoxidation operation of cast steel, some elements that will delay grain growth are added, so compared with forged steel, cast steel is not easy to form coarse grains. Steel castings with coarse grain due to composition can be refined by annealing or normalizing.
(3) Aluminium alloy
Iron impurities will make the aluminum castings coarse and brittle. Most of these defects are caused by improper melting operation. In aluminum alloys, especially those requiring overheating, it is necessary to add an appropriate amount of fine grain alloy elements.
(4) Copper alloy
The defects of coarse grains in copper alloys are often covered by pinholes, pores or shrinkage porosity. Due to the composition change of copper alloy, the product grain will be coarse, but usually pinholes, pores or shrinkage porosity will appear first.