Mold costs depe…
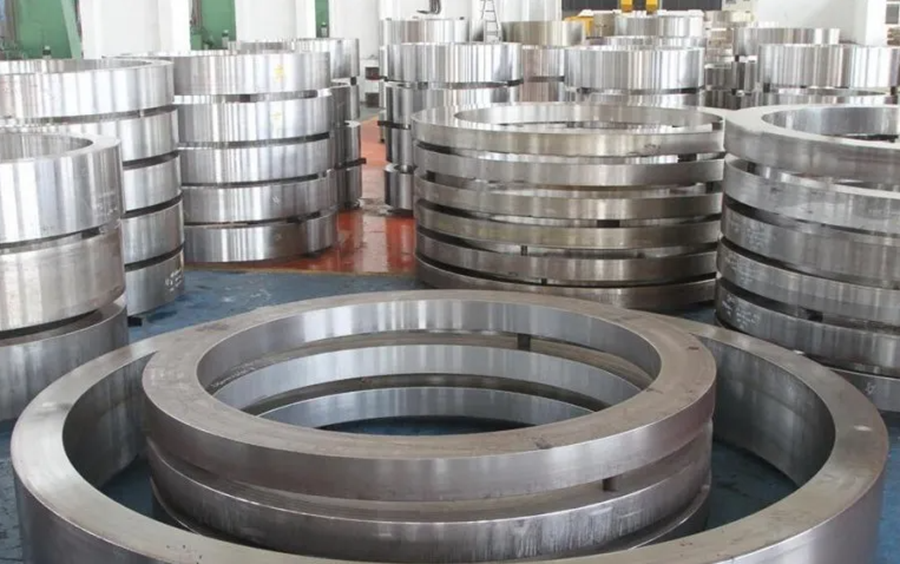
Steel for heavy forgings – forging process
Steel for heavy forgings – forging process
Large ingots are required for smelting and forging large forgings. The single weight of large ingots ranges from 30 to several hundred tons. The larger the ingot is, the more serious the metallurgical defects such as segregation are. Therefore, the smelting requirements of steel for large forgings are very strict. In order to ensure the casting of extra large steel ingots, it is generally necessary to use more than two smelting furnaces for casting, so it is not necessary to increase the capacity of a single furnace and reduce the erosion of refractory materials and the reduction of molten steel temperature due to long casting time. Raw materials must be carefully selected during smelting, and harmful elements such as boron, copper, tin, antimony and arsenic that are difficult to remove during smelting must be strictly controlled. Large basic electric arc furnace and large converter can be used for the initial smelting of steel. The molten steel must be refined outside the furnace and degassed in vacuum to minimize the sulfur, phosphorus and gas content in the steel, so as to obtain high purity steel with sulfur and phosphorus lower than 0.005%, hydrogen lower than 2%, oxygen lower than 30%, and nitrogen lower than 40%. In order to reduce segregation and defects, new pouring technologies such as rotary casting, hollow ingot casting and directional solidification casting should be adopted for the casting of large steel ingots.
The purpose of forging process is mainly two: one is to economically forge the ingot into the required shape blank, that is, forming; The second is to improve the metal structure, destroy the as cast structure of the ingot through forging, homogenize the structure, refine the grain, and weld defects such as porosity, porosity, shrinkage cavity. Generally, large ingots are directly heated from the smelting workshop to the forging workshop. In order to weld the defects, the forging of large forgings is generally carried out on the hydraulic press with great pressure, mainly using the free forging process.
Due to the influence of size effect, the heat treatment of large forgings has its own characteristics. Full consideration must be given to the metallurgical characteristics of large forgings, the transient stress and residual stress generated by large forgings during heat treatment, the influence of phase change latent heat on heating and cooling processes, temper brittleness and fabric refinement. There are mainly two kinds of heat treatment for large forgings: the first heat treatment and the second heat treatment.
The first heat treatment, also known as post forging heat treatment, is mainly aimed at preventing white spots, improving the uniformity of chemical composition, refining the structure, eliminating mixed crystals, etc., creating internal organizational conditions for ultrasonic flaw detection and final performance, and creating conditions for reducing hardness, eliminating stress and facilitating rough machining. If the hydrogen content in steel drops below 2% during smelting, the first heat treatment will mainly consider grain refinement and elimination of mixed grains.
The second heat treatment is the final performance heat treatment. Its main purpose is to make the rough machined large forgings obtain the best structure required to ensure the good comprehensive performance of large forgings. The second heat treatment usually adopts quenching and tempering, normalizing plus tempering, normalizing plus aging, etc. For forgings requiring high hardness, such as large cold rolls, the final heat treatment shall be quenching and low temperature tempering to meet the requirements.