Mold costs depe…
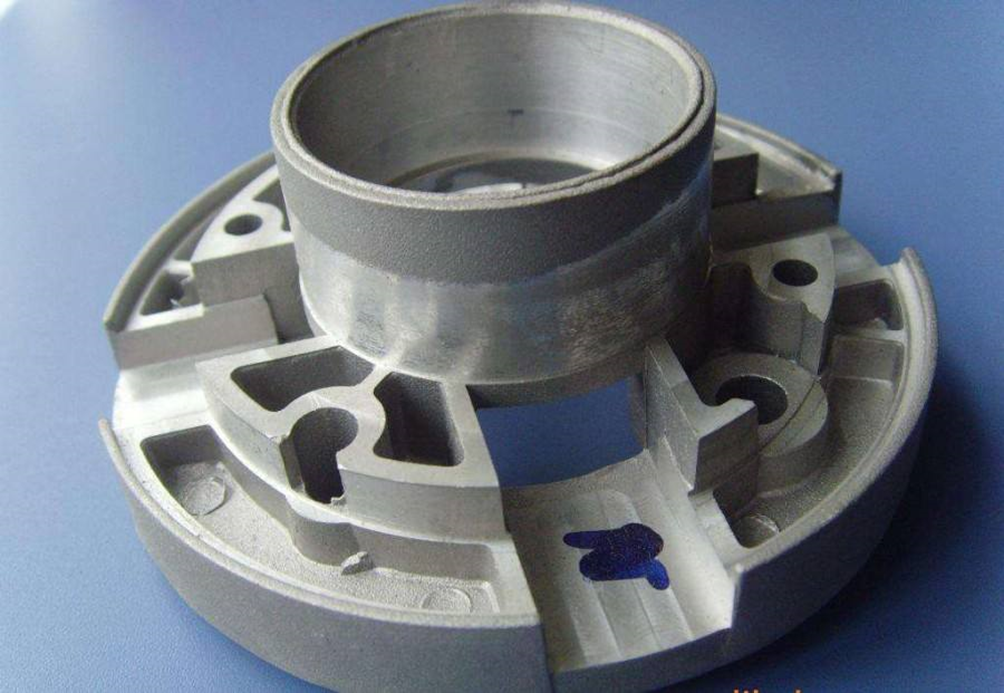
Solutions and preventive measures for 10 defects of aluminum die casting
1、 Flow marks and patterns
Visual inspection: the casting surface has stripes consistent with the flow direction of liquid metal, and has obvious non directional veins different from the color of the metal substrate, without development trend.
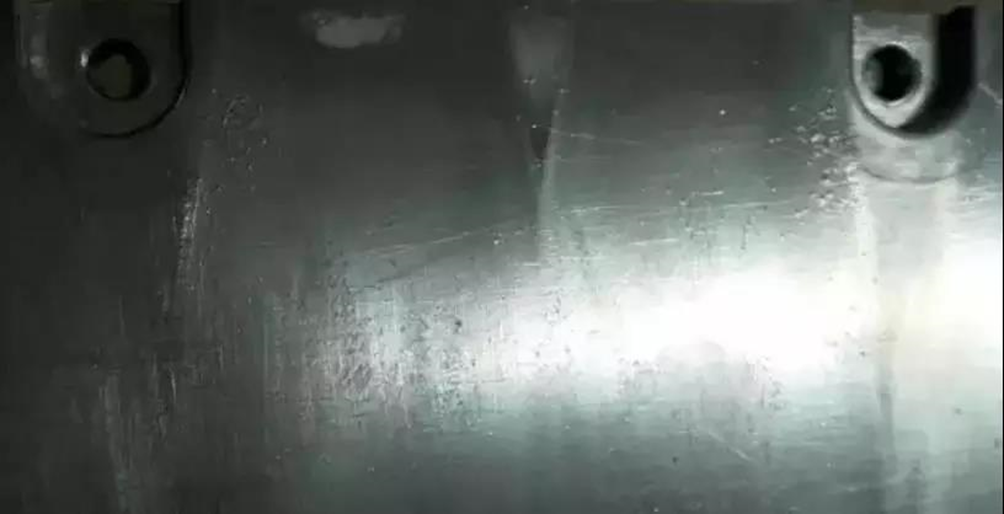
1. The causes of flow marks are as follows:
1) Too low mold temperature
2) Poor runner design and poor internal gate position
3) Material temperature is too low
4) Low filling speed and short filling time
5) Unreasonable gating system
6) Poor exhaust
7) Spray is unreasonable
2. The pattern is caused by excessive coating or poor coating quality in the mold cavity. The solutions are as follows:
1) Adjust the sectional area or position of the ingate
2) Increase mold temperature
3) Adjust the speed and pressure of ingate
4) Proper coating selection and dosage adjustment
2、 Reticulate fin (turtle crack)
Appearance inspection: there are raised or sunken marks like reticular hair on the surface of die castings, which will expand and extend with the increase of die casting times.
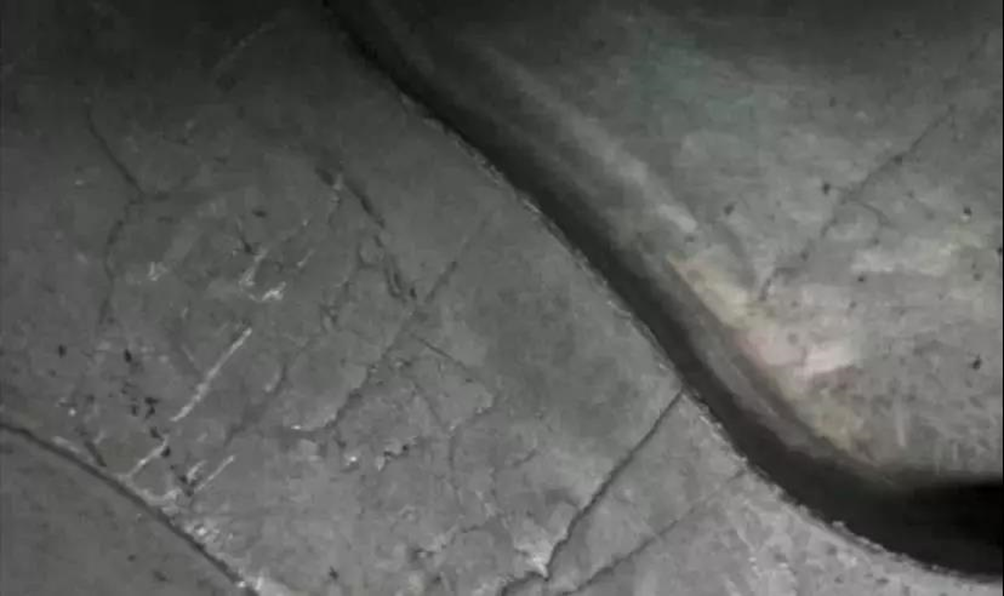
The causes are as follows:
1) There are cracks on the surface of the die-casting die cavity
2) Uneven preheating of die casting die
The solutions and prevention methods are:
1) The die-casting die shall be annealed regularly or after die-casting for a certain number of times to eliminate the stress in the cavity
2) If cracks have appeared on the cavity surface, the molded surface shall be polished to remove the crack layer
3) Mold preheating shall be uniform
3、 Cold shut
Appearance inspection: the surface of the die casting has obvious, irregular, sinking linear lines (there are two kinds of penetrating and non penetrating), small and long in shape, and sometimes the junction edges are smooth, which may break under the action of external forces.
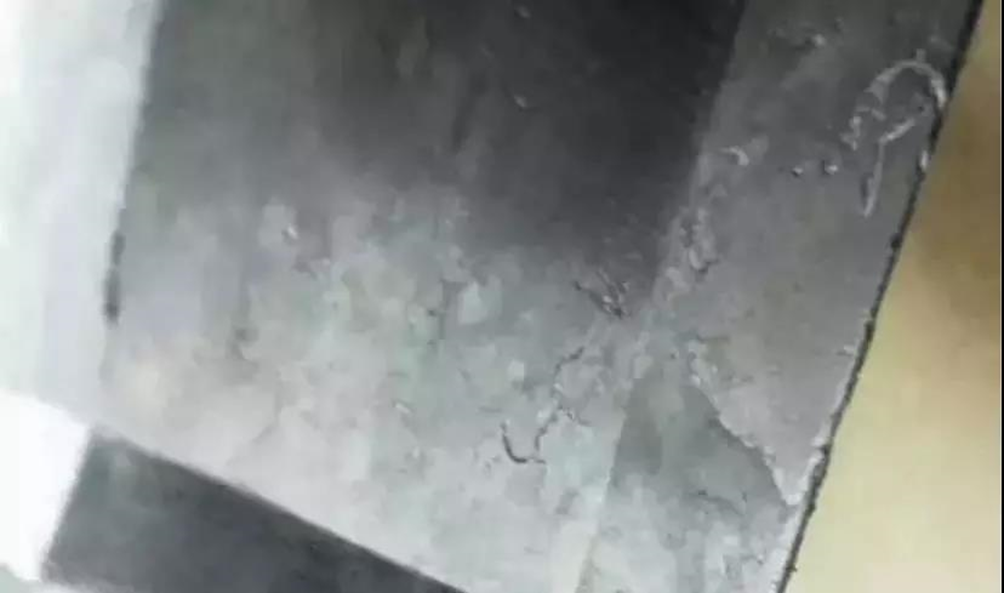
The causes are as follows:
1) The two metal streams are connected with each other, but they are not fully fused and there is no inclusion between them, and the bonding force between the two metals is very weak
2) The pouring temperature or die casting mold temperature is too low
3) Incorrect runner position or too long flow path
4) Low filling speed
The solutions and prevention methods are:
1) Properly increase the pouring temperature
2) Increase injection ratio, compress short filling time, and improve injection speed
3) Improve exhaust and filling conditions
4、 Dent
Visual inspection: there are smooth dents (like discs) on the surface of most thick die-casting parts.
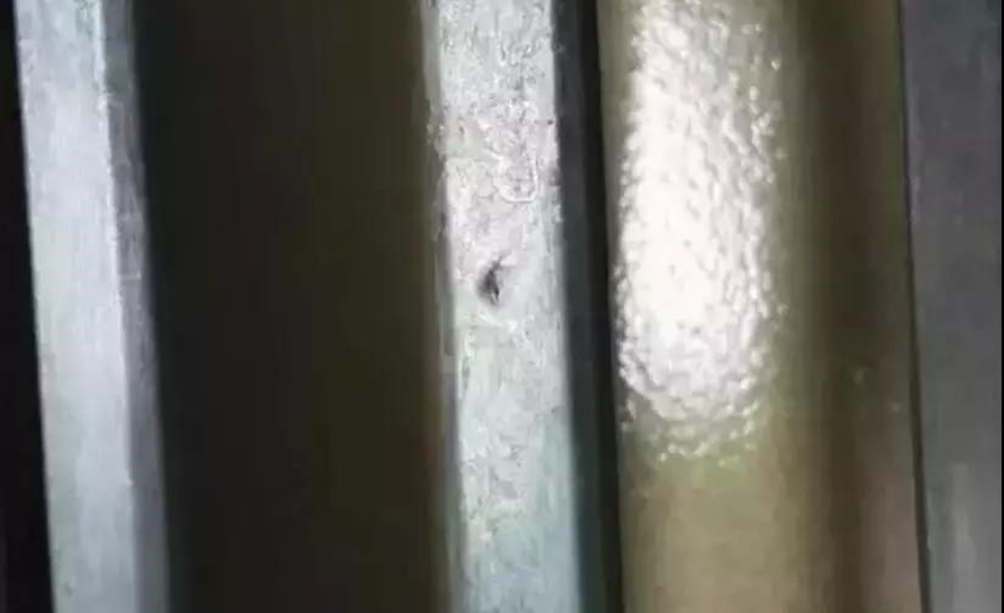
The causes are as follows:
1) Caused by shrinkage
Improper design of die castings, large wall thickness difference
Improper runner position
Pressure injection ratio is low and pressure holding time is short
Local temperature of die casting die is too high
2) Unreasonable cooling system design
3) Premature mold opening
4) Pouring temperature is too high