Mold costs depe…
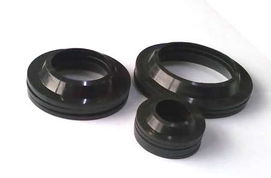
Rubber frozen trimming
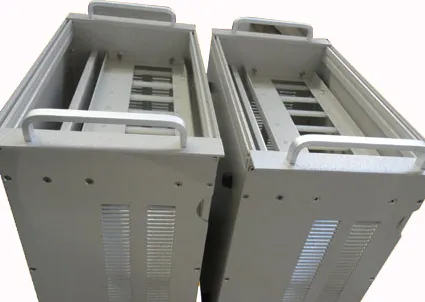
1、 Process introduction
The spray type freezing trimming machine is fully called the automatic spray type freezing trimming machine. The freezing trimming theory originated in Europe and the United States in the 1970s, and was later improved by Japan. The equipment is mainly used to remove burrs from rubber molded parts, precision injection molding and die-casting products instead of manual processing. Such equipment has been widely used in developed countries since the late 1970s, After 2000, it was gradually promoted in China and became one of the necessary equipment for the next process in the rubber and plastic industry.
2、 Working principle of low-temperature freezing treatment
The freezing trimming machine uses the freezing effect of liquid nitrogen to embrittle the burr of rubber, plastic, zinc, magnesium and other die-casting products under extreme cold conditions, and in this state, the burr of products can be removed with high quality by spraying the burr of products with high-speed plastic projectiles
TA: feeding temperature
T E: Product embrittlement temperature
TC: Set temperature of trimming machine
T1: Brittleness start time of flash
T2: Starting time of product embrittlement
Δ T=t1-t2: processing time period
3、 Development and evolution
Frozen trimming first appeared in the 1950s, and has roughly experienced four development stages since then.
(1) With the drum as the working container, dry ice was initially selected as the refrigerant. Install the parts to be repaired into the drum, or add some working medium that can play the role of friction. The temperature in the barrel shall be controlled within the range where the overflow edge is brittle and the product body is not brittle. In order to achieve this goal properly, the thickness of the overflow edge should be ≤ 0.15 mm. The drum is the main part of the equipment, which is octagonal. The key point is to control the falling point of the spraying medium so that the tumbling can be carried out repeatedly. The drum rotates in a counterclockwise direction, and the material falls along the line 1-2 under the action of gravity, and then circulates in order to reach even turning. After a period of time, the overflow edge becomes brittle, and finally the trimming is completed evenly. The disadvantage of the first generation technology is that it is not thorough, especially on both sides of the parting surface, residual overflow is easy to occur. The reason is that the mold design is improper, or the rubber layer at the parting surface is too thick (more than 0.2mm).
(2) The second generation of freezing trimming machine has made three improvements on the basis of the first generation.
① Refrigerant shall be changed to liquid nitrogen. Because the vaporization point of ice is – 78.5 ℃, it is not applicable to some rubber types (such as silicone rubber) with low brittleness temperature. The boiling point of liquid nitrogen is only – 195.8 ℃, which can cover all kinds of rubber
② Improvement of containers for products to be repaired. The drum is replaced by the trough conveyor belt as the carrier. In this way, because the products to be repaired can roll round and round in the groove, the occurrence of dead corners is greatly reduced. It not only improves the work efficiency, but also improves the precision of trimming.
③ Instead of simply relying on the friction between the parts to be repaired to remove the edges, a fine-grained spray medium is introduced. Granular metal or hard plastic pellets with particle size of 0.5~2mm are used to shoot at the surface of the object to be repaired at a linear speed of 25~55m/s, resulting in a great impact force, which greatly shortens the cycle.
(3) The third generation of freezing trimming machine is improved on the basis of the second generation, and the container of parts to be repaired is changed into a basket with four walls and holes. These holes are distributed all over the four walls of the basket, and the hole diameter is about 5mm (larger than the diameter of the shot to allow the shot to fall through the hole smoothly). After being recycled to the top of the equipment, they can be used for the second time. This arrangement can not only expand the effective capacity of the container, but also reduce the storage of the impact medium (projectile). The internal structure design of the third generation freezing trimming machine focuses on: the hanging basket is not vertically placed, but with a certain gradient (40o~60o). Its advantage is in the process of punching and repairing. Due to the superposition of the two forces, it turns violently. The first force is the rotation force provided by the basket chassis; The second force is the centrifugal force caused by the impact of the projectile. When these two forces are combined, 360 ° omnidirectional motion will be generated, resulting in uniform and thorough turning, thus shortening the processing cycle.
(4) The fourth generation of freezing trimming machine The third generation of freezing trimming machine has the advantages of even turning and fast processing, but it also has two disadvantages.
First, limited by the volume of the hanging basket, it is not suitable for large products with a diameter ≥ 200mm;
Second, due to the limit of the hanging basket volume, only batch operations can be carried out, and each batch change and startup requires repeated consumption of liquid nitrogen, which increases the cost. For this reason, a continuous production line capable of flow production has emerged. After the parts to be repaired enter the working area, they run forward with the help of the annular conveyor belt, and then they are cooled in the liquid nitrogen freezing area and shot blasted in the impact area to complete the impact edge removal, and then the finished products that have been trimmed can be taken off the line. If large and small specifications are mixed, they can be sorted. After the impact medium is recycled, it returns to the repository through external circulation.
3、 Treatment process of low-temperature freezing treatment:
Set parameter=> Product release=> Equipment cooling=> Automatic processing=> Product discharge
4、 Application field and scope of low-temperature freezing treatment:
Applicable products: electronics, automobile, aerospace, computer, communication, household appliances and other industries
Applicable materials: rubber and plastic, zinc alloy, magnesium alloy, etc.
5、 Equipment characteristics
The spray type freezing trimming machine is a stainless steel body, and the main parts are imported equipment. The man-machine interface design is simple, simple, safe, and efficient. It occupies less space, has low use cost, and has obvious economic benefits. It is the best technology and best effect deburring equipment in the market.
Technical features:
“Deep cold” freezing trimming machine is the most advanced freezing trimming machine model in China, which has introduced the latest freezing trimming technology from abroad.
① “Deep Cold” frozen trimming machine is applicable to products made of different materials such as zinc alloy, magnesium alloy, rubber, precision injection molding, etc.
② All core components are high-end imported brand equipment.
③ The main body of the equipment is made of high quality SUS to ensure a long service life.
④ The efficient thermal insulation materials in the equipment can effectively block the heat exchange, reduce the temperature faster and lower the use cost compared with similar products.
⑤ The equipment power proportioning system, sorting system, sealing system and other major technical links are in an absolute leading position.
⑥ The equipment has fast cooling, tight sealing, low noise, no pollution, energy saving and environmental protection.
⑦ The protective device for equipment and products can effectively avoid the appearance damage to the treated products during the processing.
Efficacy characteristics:
1. The operation is simple. Ordinary workers can operate the machine normally after half an hour of training. The advanced automatic control system can prevent misoperation and eliminate potential safety hazards.
2. The production efficiency is high. The average daily (8 hours) processing capacity of a freezing trimming machine is equivalent to the trimming (burr) workload of 50-80 skilled workers (each skilled worker can handle 4000 parts per day, which can greatly reduce your management costs).
3. It is especially suitable for processing high-precision products. The trimming precision is high. It can remove very small and hidden burrs, and is not limited by the product shape (up to 1/100mm precision). The qualification rate is high, the trimming quality is stable, and the qualification rate of finished products remains above 98%. (It can greatly reduce your product scrap rate).
4. It can remove the flash of small rubber and plastic products, polyurethane products and magnesium, zinc alloy and magnesium alloy castings with complex structure and any shape.
5. It will not damage the surface of products, and can improve the appearance quality of your products and increase the service life of alloy products.
6. It takes only 10 square meters for a freezing trimming machine and auxiliary equipment, which can save your valuable workshop area.
7. It can improve the corporate image and product competitiveness.