Mold costs depe…
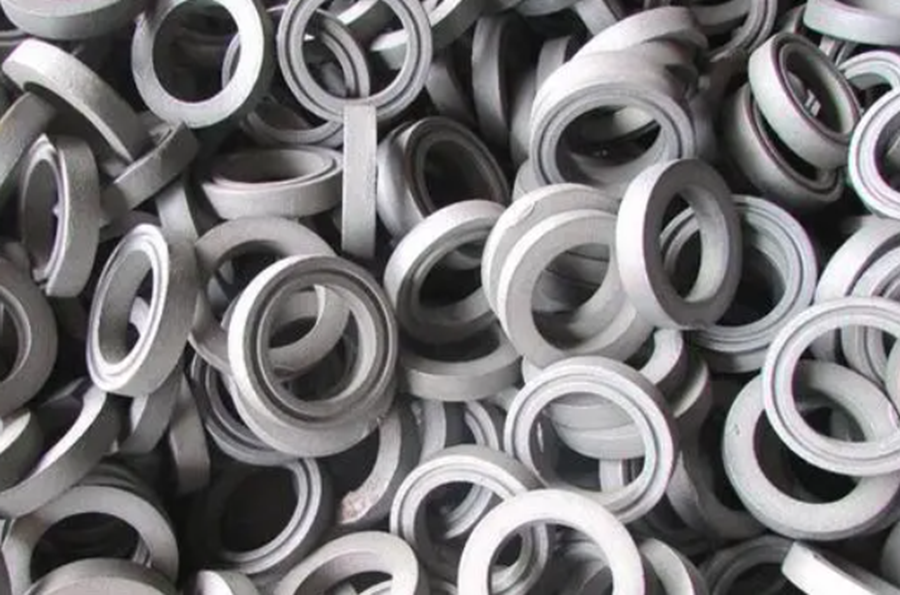
Resin sand casting 15 questions if you answer?
1. Why is phosphoric acid mostly used as the curing agent of high nitrogen furan self hardening resin, but rarely used as the curing agent of low nitrogen furan self hardening resin?
This is due to the low nitrogen and high furfuryl alcohol resin. When acid is used as the curing agent, the curing speed is slow, the demoulding time is long, and the strength is very low. The necessary hardening rate can be obtained by using phosphoric acid as curing agent for high nitrogen and low furfuryl alcohol resin. Moreover, high nitrogen and low furfuryl alcohol resin can obtain good final strength by using phosphoric acid as catalyst.
This result is mainly due to the poor mutual solubility of phosphoric acid and furfuryl alcohol, and the high affinity with water, which makes it difficult for the water contained in the resin and catalyst and the water generated by the resin in the polycondensation reaction to diffuse and discharge, while the water droplets generated with phosphoric acid as the core remain in the resin film, destroying the compactness of the resin film, so the strength is low. However, the high nitrogen resin has good mutual solubility with water. It is not easy for all kinds of water to concentrate as water droplets with phosphoric acid as the core. The resin membrane has good structure and high strength.
2. Why is the hard permeability of phenol urea self hardening resin better than that of furan self hardening resin sand?
Because the curing process of phenol urea resin is polymerization reaction, there is no small molecule of water generated during the curing process, and there is no problem that the internal and external curing speed is inconsistent due to the different volatilization speed of water inside and outside the mold, while the curing process of furan self hardening resin is polycondensation reaction, and water is generated during the reaction process. Because the water evaporation speed inside and outside the mold core is different, the internal and external curing speed is different, so its hard permeability is poor. This is also the reason why the curing speed of furan self hardening resin sand is greatly affected by the relative humidity of the air.
3. Why can high nitrogen furan resin be used to produce aluminum castings and copper castings?
As aluminum and copper metal liquids can hardly dissolve nitrogen, nitrogen generated by resin decomposition during casting will not be absorbed by aluminum and copper metal liquids, and nitrogen pores will not be formed due to nitrogen precipitation during solidification, even if high nitrogen resin is used. Therefore, the production of aluminum and copper castings can select high nitrogen resin for the need of collapsibility.
4. Why is it suitable for self hardening resin sand to produce heavy castings and the gating system is made of ceramic pipes?
The self hardening resin sand molding is adopted. When producing heavy castings, the resin sand will collapse prematurely and lose its strength due to the long pouring time of the gating system under the long-term thermal action of high temperature molten metal, resulting in sand washing defects. Therefore, for heavy castings, the gating system should be made of ceramic pipes, and the problem that the gating system, especially the sprue, is not easy to be coated has been solved.
5. When self hardening resin sand is used for molding and core making, how to determine whether the service time of resin sand meets the requirements?
When intermittent sand mixer is used, the usable time of resin bonded sand is longer than the time from mixing and unloading to using up; When the continuous sand mixer is used for molding and core making, the available time of resin bonded sand shall be longer than the time from the initial sand release position at the sand outlet of the sand mixer to the continuous sand release position again.
6. Why is the mold pulling angle of the pattern for self setting resin sand larger than that of clay sand?
The resin sand core has a certain hardening strength when pulling out the mold, without yielding. Generally, it is not possible to loosen the mold or sand core wall by knocking the mold and core box frame, and the friction is large when pulling out the mold; The resin sand mold and sand core have poor repairability. When the mold is lifted, it is difficult to repair the sand mold and sand core once they are incomplete.
7. Why should fewer shrinkage risers and more outlet risers be set for the production of cast iron by resin sand process?
The resin sand mold has good rigidity and high sand mold strength at the beginning of pouring, which makes it possible to effectively eliminate shrinkage cavity and porosity defects by making use of graphitization expansion in the solidification process of cast iron, so as to realize less riser and no riser casting of gray iron and nodular iron castings. However, the gas yield of resin sand is. In order to facilitate the smooth discharge of a large amount of gas in the medium cavity during the pouring process, more gas risers must be set up. In principle, it is required that Σ F is greater than Σ F.
8. Why is the final strength of furan self hardening resin containing 70%~80% furfuryl alcohol the highest at room temperature?
Theoretically, the higher the proportion of urea formaldehyde resin in the furan resin, the greater the final strength at room temperature. Therefore, when the furfuryl alcohol content is greater than 70%~80%, the higher the furfuryl alcohol content, that is, the lower the nitrogen content, the lower the final strength at room temperature. However, with the increase of urea formaldehyde resin, the water content of furan resin increases relatively, and the hardening rate and final strength will be reduced. When the furfuryl alcohol content is lower than 70%~80%, the decreasing trend of the final strength of the resin exceeds the increasing trend. Therefore, in general, when the furfuryl alcohol content is 70%~80%, the final strength of furan self hardening resin sand at room temperature is the largest.
9. Why use the curing agent with too strong catalytic activity and too much curing agent. Will the final strength of resin sand decrease?
The use of curing agents with too strong catalytic activity or too many curing agents will result in too short the pre curing stage, and the irregular coiled curve cluster prepolymer in the resin will be blocked in the body structure by the crosslinked prepolymer before it is fully extended and ordered, so that a large number of active groups in the coil can not participate in the reaction, and cannot form a polymer with a large degree of polymerization. Therefore, although resin bonded sand hardens faster and has higher initial strength, it will inevitably lead to a significant reduction in final strength.
10. Why should phosphoric acid not be used as curing agent when used sand of self hardening resin sand needs to be recycled?
After casting the sand mold and core with phosphoric acid as the curing agent, the phosphoric acid can not be decomposed and destroyed under the thermal action of the molten metal, but the generated phosphate is deposited on the surface of the sand particles, which is difficult to be removed through regeneration, resulting in a lot of decrease in the strength of the resin sand prepared by the recycled sand, an increase in mold expansion, and an increase in the sand inclusion tendency.
11. Why should organic acid with low free acid content and high total acid be used as curing agent for acid hardened phenolic resin self hardening sand, instead of inorganic acid?
Due to the high water content in acid hardened phenol formaldehyde resin, a large amount of water will be released in addition to the water generated from the condensation of the resin itself during the cross-linking reaction, which will play a role in diluting the hardener, making the reaction very slow. Increasing the free acid content of the hardener will speed up the hardening speed, but will reduce the strength of the self hardening sand a lot. Therefore, to ensure the hardening speed without reducing the strength of the resin sand significantly, only the total acid value of the hardener can be increased. Since the free acid of inorganic acid is generally high, the organic acid with high total acidity and low content of free acid should be selected as the curing agent for acid hardened phenolic resin.
12. Why should the amount of curing agent added to acid cured phenol formaldehyde resin sand be expressed as a percentage of resin?
This is because acid curable phenol formaldehyde resin is formed by condensation of benzoic acid and formaldehyde under the action of basic catalyst. Before leaving the factory, neutralize the basic catalyst with acid and make it weak acidic. Therefore, the resin is not as sensitive to acid hardener as furan resin, and crosslinking reaction occurs only when the acid concentration is quite high. In addition, the water content of this resin is very high, generally 15% or more in some aspects. When the cross-linking reaction occurs, in addition to the water generated by the resin itself, a lot of mutually soluble water will be released. The water will dilute the hardener. The more resin is added to the self hardening sand, the stronger this dilution effect will be. Therefore, to maintain the same curing speed, it is necessary to increase the amount of hardener. Therefore, it is appropriate to calculate the addition amount of hardener in proportion to the resin for the self setting sand of alpha phenolic resin, that is, the addition amount of hardener for acid hardened alpha phenolic resin sand should increase with the increase of the resin addition amount.
13. Why is it not appropriate to immediately paint the mold core and the newly repaired part?
Because the resin hardening reaction in the mold and the newly repaired mold and core is still in the initial stage, the normal process of hardening will be affected if the water (solvent) in the water-based coating is encountered (for the phenol urea alkyl self hardening resin, the unreacted two-component polyisocyanate can react with the water and become invalid); If alcohol based coating is used, it shall be ignited immediately after coating, which will also cause over burning of unreacted resin. These will affect the surface stability of the mold and core.
14. Why is it difficult to regenerate the used sand of alkaline phenolic resin sand?
Because the alkalinity of alkaline phenolic resin is very high (the basic PH value is generally 11-13), the resin contains more alkali (generally potassium hydroxide). During pouring, the alkali in the resin is easy to react with silica sand to generate low melting point silicate, and the molten silicate is firmly adhered to the sand particles, which is difficult to remove, resulting in more difficult removal and more difficult regeneration of old sand.
15. When selecting the type of resin, what factors should be considered for the casting?
When selecting the type of resin, the following factors of castings shall be considered:
(1) The material of the casting. When the material of castings (steel castings and high alloy iron castings) tends to produce nitrogen porosity, low nitrogen or nitrogen free resin should be selected; When the material of castings (nodular iron castings, gray iron castings) is a ferrous metal with a small tendency to produce nitrogen pores, medium nitrogen resin can be selected; High nitrogen resin shall be selected for nitrogen insoluble copper and aluminum parts.
(2) Weight, wall thickness and pouring temperature of castings. When the casting is heavy, the wall is thick and the pouring temperature is high, the resin with high furfuryl alcohol content and low urea formaldehyde content should be selected to make the high temperature strength of the core meet the needs; Low pouring temperature, light weight, thin-walled castings require low high temperature strength, so resin with higher urea formaldehyde content can be selected to reduce cost.
(3) Structure of the casting. The casting is prone to hot cracking, so the resin with high temperature and low temperature should be used as the binder first. For steel castings prone to hot cracking, alkaline phenolic resin should be used instead of furan nitrogen free resin as the binder; Castings are prone to cold cracking, and the binder with good collapsibility should be selected.