Mold costs depe…
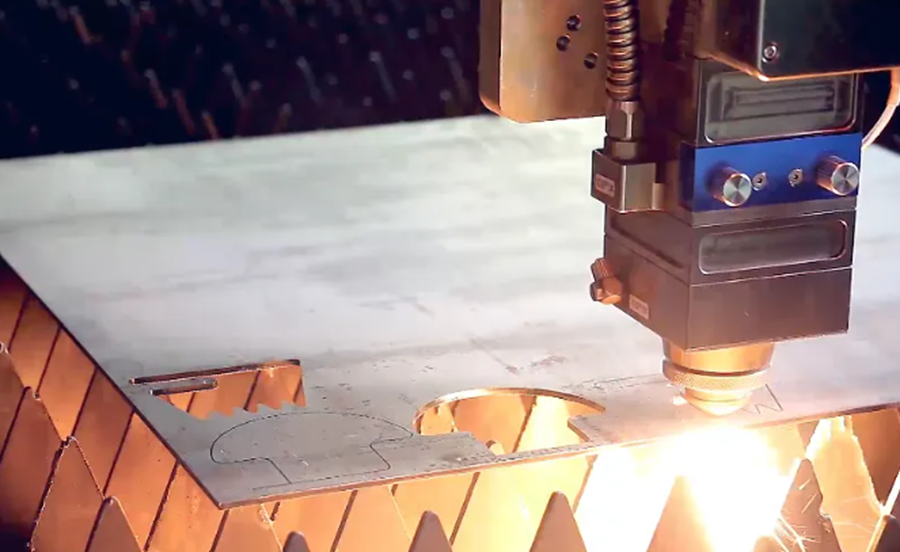
Rational Choice between Digital Impulse Machining and Laser Cutting
When a sheet metal processing enterprise has just received a new production project to prepare for investment, it will face such a choice: should it buy a laser cutting equipment or a CNC punch? As we all know, in today’s sheet metal processing industry, there seem to be ten thousand reasons to promote sheet metal processing enterprises to invest in laser cutting machines. In addition, with the increasingly vigorous development of the co processing business, many enterprises may start to consider gradually withdrawing the outsourcing processing business and plan to enter new business areas at the same time. If the enterprise happens to receive a batch of large orders with a large variety of products, then, as the decision-maker of the enterprise, have you ever hesitated about which selection conditions are the important parameters in investment evaluation? In addition, before signing the contract, how can you judge that you have made the right decision in this regard?
Based on cost and production process
In the past two years, there has been a concept on the market that is constantly being spread, and its influence is also expanding: “The digital blanking processing era has passed, and laser cutting is the future and gospel of the metal sheet processing industry.” However, in the opinion of a senior sheet metal engineer, this sentence is obviously too extreme and impetuous.
At any time, a qualified sheet metal processing manufacturer needs to properly combine and allocate different processing equipment, so as to formulate the most lean material flow in the workshop, and produce the most stable sheet metal parts at the lowest possible cost. Einstein once had a famous saying: “In this world, the most perfect machine is the machine that can effectively complete production tasks in the simplest way.” Here, we can also borrow the saying, “In this world, the most perfect process is the process that can complete the production task in the most concise and low-cost way in the fastest and most stable way.”.
Therefore, when an experienced manager of a sheet metal processing enterprise makes production planning and investment, he will include the cost of electricity, consumables and maintenance into the hourly cost one by one. After considering the flexibility and stability of production, he will certainly make reasonable judgments and decisions between the above popular concepts and the actual evaluation results.
Mr. Peter Visser, a senior application consulting expert of MATE Precision Mold Co., Ltd., has more than 25 years of industry experience and has visited more than 1000 sheet metal processing enterprises. The biggest cost control project he participated in in his career is to help a world famous manufacturer select appropriate digital blanking equipment and laser equipment for different process flows and processing requirements, thus saving massive processing costs for the enterprise.
In Mr In his career, Peter Visser has seen too many customers directly say, “This batch of work will be handed over to laser processing”, but he has never realized that different processes will have different effects on the entire manufacturing process, nor has he considered the subsequent processing bottlenecks caused by improper processes. Sometimes, the customer will process the thick plate with a few strokes, but the thin plate will be processed with a laser. In fact, it is more appropriate to exchange the two.
For example, in the field of architectural design and HVAC engineering, we will use a large number of holes to achieve design or ventilation functions. However, many customers take it for granted that they use laser cutting machines to process, resulting in extremely slow processing speed and high production costs. In order to make readers better understand the difference, we take an example: machining 1000 round holes with a diameter of 12.7mm on a 1.5mm thick steel plate. If a 12 hole group hole die is used for numerical punching, the processing time required is less than 1/4 of the laser processing time. This means that if the customer receives a large order, he or she will have to invest 4 to 5 laser cutting machines to meet the capacity equivalent to 1 digital blanking machine.
Another extremely important but often overlooked key point is that the use of digital blanking equipment can effectively avoid the secondary processing problem (Figure 1) arising from the limitations of laser processing in the entire production process, thus improving the overall production efficiency of the product. Many workshops only equipped with laser cutting machines must complete the subsequent forming processes of louvers, bulges, counterbores and other sheet parts that can significantly improve the added value on other processing equipment. Therefore, the workshop has to invest more manpower and material resources, workshop area and more and more secondary processing equipment. Sometimes, these derived secondary processing will take thousands of working hours, thus increasing a large part of the hidden production costs.
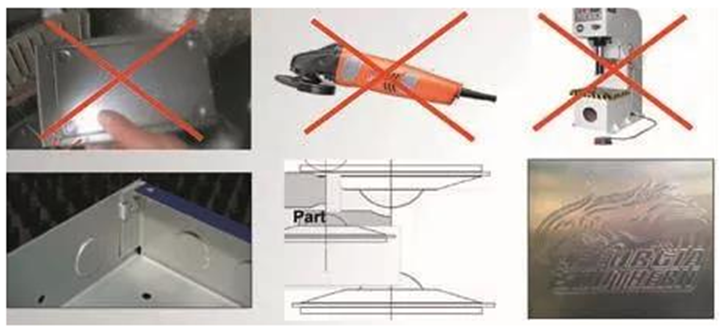
Through analysis and calculation, Mr. Peter Visser found that these manufacturers can actually purchase a new (or second-hand) digital processing equipment, which can save hundreds of thousands of hours of valuable processing time, significantly reduce their operating costs, and obtain a higher input-output ratio. In short, enterprises will gain higher profits.
Selection using boundary conditions
Now, through Mr Peter Visser experienced a classic successful case to help you further understand the importance of correctly selecting processing equipment according to boundary conditions.
One of his customers is a manufacturer of electric control cabinets. There is a laser cutting machine in the workshop, which costs about $1 million a year to spot weld semi-finished cabinets in the secondary processing stage. When the enterprise evaluated and purchased the laser cutting machine that year, the relevant equipment suppliers did not mention the production possibility of the laser cutting machine. I believe that this kind of scenario will be frequently encountered. From the perspective of drawings, their products are flat and simple. They do not even need the edge and corner chamfering process and have no forming requirements. From any technical point of view, they are ideal customers and users of laser cutting equipment.
When Mr When Peter Visser visited the enterprise due to the business of laser consumables and bending dies, the production manager of the enterprise was complaining to the boss about the technical bottleneck of spot welding and the additional costs arising therefrom. When everyone fell silent, Mr Peter Visser interposed, “I wonder if you have considered the previous process of digital blanking?” To his surprise, the equipment supplier never talked with the enterprise about the possibility of digital blanking processing from beginning to end, and certainly never compared the advantages and disadvantages of digital blanking processing and laser processing for the overall process.
After briefly introducing the finishing punching process, Mr Peter Visser held a technical seminar at the user’s place of the digital blanking machine to further discuss various processing technologies on the digital blanking machine. At the meeting, everyone reached a consensus that although laser processing is very suitable for the blanking products of the factory from the perspective of a single process, once the vision is expanded to the whole processing process, it is the digital blanking equipment that can better avoid deriving various secondary processing, and spot welding is just one of them. Based on this idea, if the laser processing is replaced by digital blanking equipment, it can save massive secondary processing costs.
Within 5 months after the meeting, the customer quickly purchased a digital processing equipment, which saved the company more than 1 million dollars in derivative processing costs in the following year. According to this rhythm, the financial department of the company concluded that the company would save nearly 15 million dollars in the next 10 years. Based on this conclusion, the company soon added a more powerful digital blanking equipment in the second year.
Other factors affecting investment
Another important factor affecting investment is the first investment cost. Generally speaking, the price of a digital pulse device is about half of that of a laser device. If properly maintained, the service life of the equipment and its residual value in the secondary market are much higher than those of laser equipment. In addition, the maintenance time and corresponding downtime of the digital impulse equipment, even the floor space, are usually far less than the laser equipment. Therefore, for a small processing plant that is still in the initial stage, the first consideration is often to purchase digital impulse equipment, rather than laser equipment that seems easy to use, so as to ensure the low budget and high stability of the plant, and greatly reduce its technology and cost risks in the early start-up stage.
Thanks to Mr Peter Visser has also been involved in the purchase of laser cutting machines. He knows that in general, the sales personnel of laser cutting machines will tell customers that the consumption cost of laser processing is getting lower and lower, even lower than that of several strokes. Some sales personnel of laser cutting machines even mislead customers and claim that the digital blanking die is a huge expense, which will raise the overall cost of digital blanking processing to an astonishing level.
But the fact is, according to our experience data, the annual die expense of each punching machine, even considering some special forming processes, is only more than 10000 dollars. The invisible costs of laser cutting are far more than these, such as:
⑴ Helium gas used to supply CO2 laser source;
⑵ Nitrogen, oxygen, compressed air, focusing mirror and nozzle used for cutting;
(3) Various optical lenses for conducting CO2 laser beam;
(4) Various sensor cables used to transmit measurement signals;
⑸ Protective mirror used to prevent splashing during optical fiber laser processing;
(6) Time for cleaning rack and removing slag and debris;
(7) A large number of other services and maintenance work that can be classified as the cost of laser processing.
In fact, we only need to consider some of the above factors to support our view: in the laser cutting process, the total processing cost of customers is still far higher than that of digital blanking. Instead of what some salespeople claim, operating costs have dropped to a level that makes people fascinated.
Another controversial point is the delivery date of the mold. There is no doubt that laser processing is much faster than digital processing in proofing and rapid production organization. However, many readers already know that many mold manufacturers have greatly shortened the delivery time of molds through continuous lean transformation in the past 20 years. The delivery time of a large number of standard molds has even been shortened to the same day. For MATE’s overseas customers, the mold has actually arrived at the airport of the corresponding region within two to three days after the order is placed. In many cases, the customer’s local cumbersome customs clearance procedures are the biggest obstacle to the mold delivery, not the mold manufacturing itself.
For MATE’s users in North America and Europe, the fast mold delivery date, all kinds of special-shaped molds, and the processing capacity of solid blanking are enough to kill the laser cutting machine for a day or two in advance.
Another factor worth considering is that according to the cutting quality of different cutting gases and equipment, there will be a lot of slag on the inner holes of parts after the completion of laser cutting, which is not suitable for powder spraying or painting. In this case, the customer either invests in a deburring device or organizes several people to perform subsequent derived deburring.
Of course, the digital blanking can also produce burrs, but when the product shape is appropriate, the digital blanking equipment can also complete the ball deburring of large holes, completely/partially replacing a large number of deburring processes. Similarly, tapping, solid blanking, forming, budding, etc. can be processed on the digital blanking equipment through one-time clamping, as shown in Figure 2.
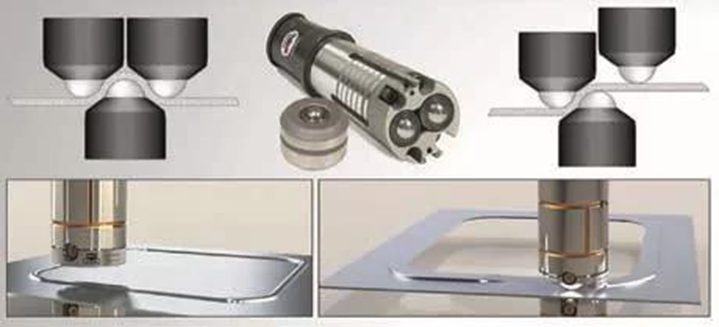
rational choice
It should be emphasized that this article is not intended to guide customers to abandon laser processing and completely adopt digital blanking processing. We hope that readers will not misunderstand. As we all know, laser is a high-tech processing technology, which can complete many processes that cannot be completed by digital blanking process, such as laser welding, pipe cutting, laser marking, etc. With the continuous progress of laser technology, laser equipment is definitely worth buying and using for the processing of appropriate thickness and plate type.
The main idea of this paper is to hope that customers can keep rational manufacturing thinking in the turbulent laser procurement boom, examine their own economic strength, customers’ processing requirements, the types of plates used and the processing process of the whole factory, and choose the appropriate processing technology instead of learning to walk in Handan, so as to avoid copying.
At the end of this article, the author also has a small suggestion: before the enterprise decision-maker takes out $500000 to $1 million to purchase laser cutting equipment, it is advisable to consult with a third-party enterprise that has nothing to do with equipment manufacturing but is still committed to punching, cutting and folding technology. Perhaps more inspiration and suggestions can be obtained from it, so as to avoid falling into regret when buying.