Mold costs depe…
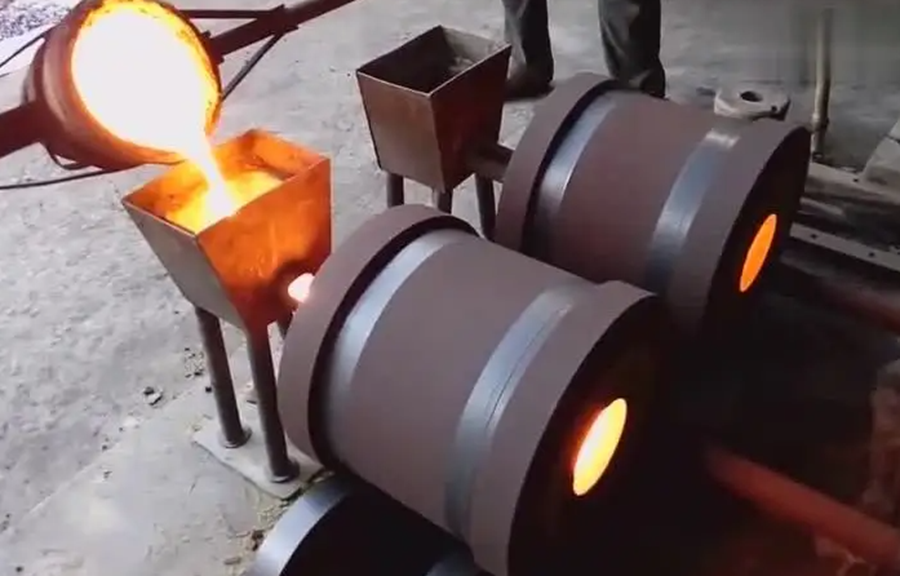
Process Flow of Water Cooled Metal Mold Centrifugal Casting
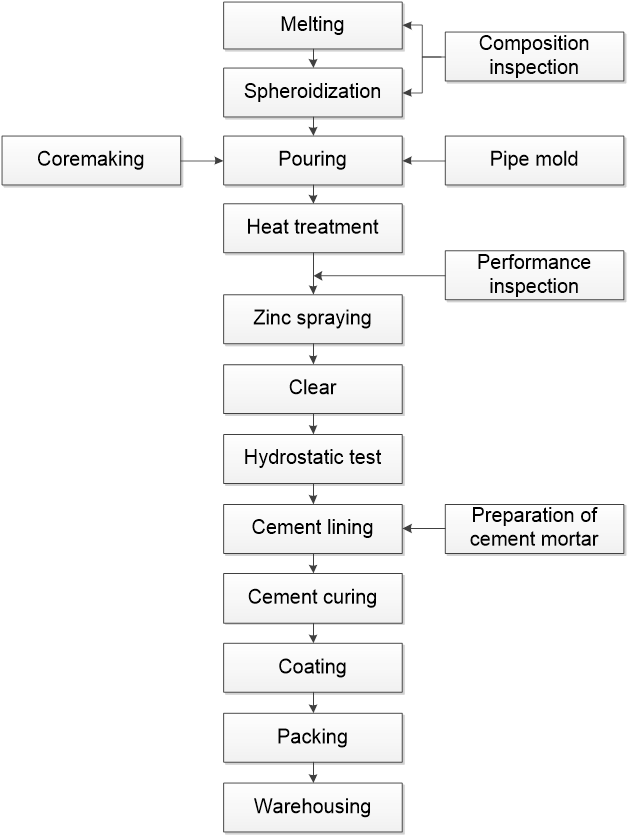
melting
Add raw materials (scrap steel, pig iron, recycled materials, etc.) into the melting furnace (induction furnace or cupola) and adjust their composition. When the composition meets the process requirements, pour molten iron into the frequency conversion holding furnace for spheroidizing. If the sulfur content in molten iron exceeds the standard, desulfurization treatment shall be carried out first.
Spheroidization
When the composition and temperature of molten iron meet the process requirements, the spheroidizing agent is added to the molten iron to change the flake graphite in the molten iron into spherical graphite, which is sent to the centrifugal casting section for pouring.
Centrifugal casting
Install the bell mouth core on the centrifuge, pour the qualified molten iron into the ration ladle, set the amount of inoculant and pipe mold powder, the rotating speed, traveling speed of the centrifuge and the turnover speed of the ration ladle according to the process requirements, pour the molten iron into the rotating pipe mold with the turnover of the ration ladle and the walking of the centrifuge, and solidify it into a pipe. When the temperature of the pipe in the pipe mold drops below 600 ℃, The pipe puller pulls the pipe out of the mold and sends it to the heat treatment department.
heat treatment
The tubes produced by centrifugal casting have a large amount of cementite in the metallographic structure, so that the mechanical properties of the tubes can not meet the requirements of ISO2531 standard. Therefore, the pipe shall be annealed to eliminate the cementite and change its basic structure into ductile iron pipe based on ferrite, so that its performance can meet the requirements of ISO2531 standard.
Zinc spraying
In order to further enhance the corrosion resistance of the ductile centrifugal cast iron pipe, it is necessary to spray zinc on the external surface of the pipe. In order to ensure the quality of zinc spraying, the best effect should be achieved when the pipe body still has a certain temperature after the heat treatment process is completed.
clear
To ensure the surface quality of the pipe and the installation size of the socket, the socket and inner wall of the pipe need to be polished and cleaned to ensure the installation of the pipe and the requirements of the next process.
Hydrostatic test
In order to ensure the delivery quality of pipes and the reliability of installation during the use of pipe network, the pipes shall be subject to hydrostatic test and inspection one by one according to the standards specified in ISO2531.
Cement lining and curing
In order to ensure the water delivery sanitation of the pipe, prevent the scaling on the inner wall surface of the pipe from increasing the water delivery resistance and reducing the service life of the pipe network, the water delivery pipe shall be lined with cement. Mortar lining shall comply with ISO2531 and ISO4179 standards. The cement lining shall be cured to make the lining have a certain strength before it is sent to the coating process.
Coating and packaging
To prevent the pipe from being corroded underground and prolong the service life of the pipe network, the external surface of the cast pipe shall be coated with a layer of asphalt paint, and then packaged for warehousing.