Mold costs depe…
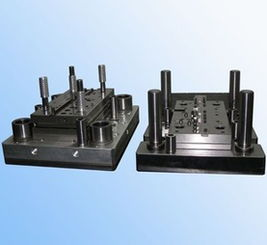
Principles for daily maintenance of stamping dies
The products manufactured by the same mold have the same size and shape. When the products have size differences, they must be repaired to restore the original state. If the design is wrong, the design must be changed. Mold maintenance is based on this principle.
[1] Measure the finished products, check the inspection standards to determine the variation, check whether the project size is the same as the mold drawing, and whether the size is different, if necessary, measure the relevant projects before and after to determine the variation and the reason, and then take countermeasures to solve it. [2] When it is impossible to judge or propose countermeasures, it is required to consult others’ opinions, and it is not allowed to make arbitrary decisions.[3] Excessive hairiness
(1) Blade wear: regrind
(2) Excessive clearance: Most of the side surfaces are light strips with low brightness, so the clearance is reduced.
(3) The clearance is too small: the secondary shear plane increases the clearance.
(4) Aligning cut mark: change the degree of engagement or make segment difference or reduce the gap.
(5) Over sharp à: the product à degree is less than 75 degrees to change the work or gap.
(6) The material is too hard: replace the material or increase the clearance.
(7) Die breakage: regrind.
(8) Improper mold shell: local hair or bruise. Re calibrate or modify the die.
[4] Die biting
(1) Mold looseness: the movement of the punch or die exceeds the unilateral clearance. Adjust the combined clearance.
(2) Die inclination: the straightness of the punch or die is not correct, or there are foreign matters between the formworks, so that the formworks cannot be flat. Reassemble or grind for correction.
(3) Formwork deformation: the hardness or thickness of the formwork is not high, or the formwork is deformed due to impact of external forces. Replace with a new template or correct the disassembly method.
(4) Deformation of mold base: the thickness of mold base is uneven or the force is uneven, and the straightness of guide pillar and guide sleeve varies. Grind and correct, or re inject plastic steel, or replace the mold base or make the force average.
(5) Die interference: whether the size and position of the punch or die are correct, whether the positioning of the upper and lower dies has deviation, whether they will become loose after assembly, whether the accuracy of the punch is not correct, and whether the frame die is not correct.
(6) Punching shear deflection: the punch strength is not high, the big and small punches are too close, the lateral force is not balanced, and the punch is half inclined. Strengthen the guide and protection function of the stripping plate, or increase the punch, shorten the small punch, increase the heel length, support and guide in advance, and pay attention to the feeding length.
[5] Dimensional variation
(1) Tool edge wear: the burr is too large or the size becomes larger (cutting profile); Smaller (punching); Poor flatness. Regrind or replace the die.
(2) No guide: the guide pin or other positioning devices do not work, the feeder is not loosened or the guide pin diameter is not flat, and the guide cannot be corrected. The positioning block is worn and the feeding distance is too long.
(3) The die is too short: the bending degree becomes larger, and the reverse is not completely formed.
(4) Escape hole: not squeezed, scratched or deformed. Clean the escape hole or increase the escape hole and depth.
(5) Ejection failure: the feeding is not smooth, the strip is bent, the stripping is not good, the upper die is pulled, and the ejection is extended.
(6) Improper ejection: the ejector pin is improperly prepared, the spring force is inappropriate or the ejection is too long. Adjust the elasticity or change the position or the number of pins; Pin grinding short fit.
(7) Poor guide: the guide plate is not long, or the guide gap is too large, or the die and the discharger are inclined, or the distance between the die and the feeder is too long.
(8) Blanking deformation: part of the bending parts cannot be allowed to overlap and must fall each time, or the dished strain can be overcome by pressure pad or shearing.
(9) Bending deformation: extruding at upper bending; The proximity hole is deformed under tension, and the bending force is uneven à The inclined punch is not long enough.
(10) Punching deformation: the material is distorted unevenly, the size increases or the eccentricity is asymmetric.
(11) Impact deformation: The product is impacted and deformed due to too strong blowing pressure or gravity falling.
(12) Floating chip extrusion: scrap floats up or fine chips remain on the die surface or foreign matters and other extrusion variations.
(13) Improper material: improper material width or plate thickness, material or material hardness will also cause defects.
(14) Poor design: poor engineering arrangement and poor clearance setting are difficult to overcome unless the design is changed.
[6] Mold damage
(1) Hot burying: the quenching temperature is too high or not high, the tempering times, temperature and time are not appropriate, and the quenching method and time are not grasped; The problem occurred after a period of use.
(2) Stamping and stacking: the sheet overlaps and continues to be stamped, usually because the stripping plate is broken.
(3) Waste blocking: blanking hole is not drilled or the size is not consistent or it falls on the bed table and is not cleaned in time, so punch and lower formwork are more damaged.
(4) Drop of punch: the punch is not fully fixed or suspended, or the screw is too thin and the strength is not good, or the punch is broken.
(5) Hole escape: the hole escape size or depth of the punch press plate is not enough, and the hole escape of the punch and stripper is usually damaged by the stripper.
(6) Foreign matter entering: The lower die, stripping plate, punch and guide post may be damaged if the products are blown out and spring back, die parts are broken and fall off, screws protrude from the die surface or other items enter the die.
(7) Assembly error: damaged due to wrong position and direction of parts.
(8) Spring factor: the peeling plate inclines due to the spring force is not strong or broken, or the height of the contour sleeve is unequal, or the spring is not often prepared, resulting in overlapping punching and damage to the parts.
(9) Improper stamping: the working height is adjusted too low, the guide pillar loses oil, the strip is sent by mistake or half punched, the peripheral equipment, such as the feeding, discharging and receiving machine is damaged, the air pipe is not installed or opened, and the punch is abnormal.
(10) Improper maintenance: the above points are caused by the replacement but not replaced, or the screws are not locked or not restored as they are