Mold costs depe…
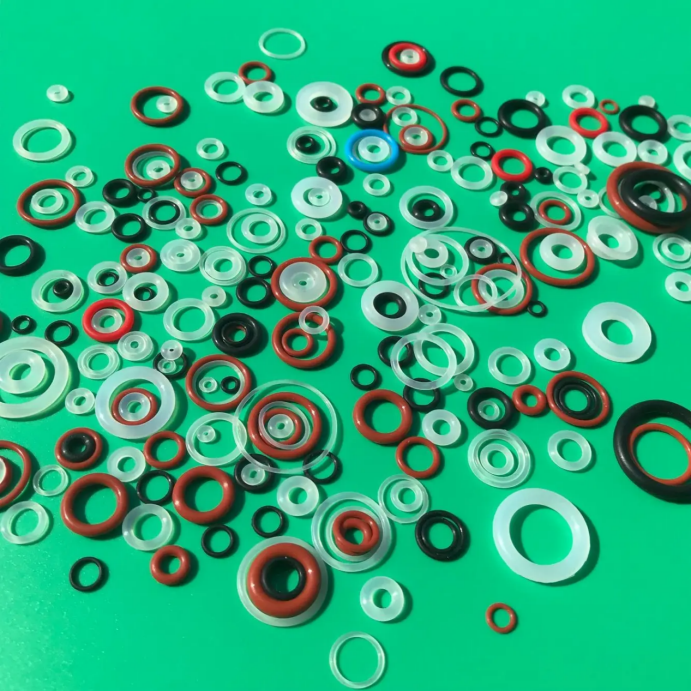
Principle and application of rubber sealing ring damping pad
Natural rubber and neoprene rubber are generally used as rubber damping pads. Nitrile rubber is required for oil resistance, silicon rubber is required for high and low temperature resistance, and butyl rubber is required for high damping.
The manufacturing process of rubber shock pad products is similar to model products except that rubber air springs are similar to tires. It is usually made into supports or connectors and widely used in various vehicles, ships, machinery, instruments, bridges and buildings to eliminate or mitigate the adverse consequences of vibration.
Rubber is characterized by both high elasticity and high viscosity. The elasticity of rubber is generated by the change of the conformation of its crimped molecules. The interaction between rubber molecules will hinder the movement of molecular chains, and it also shows viscosity characteristics, so that the stress and strain are often in an unbalanced state. The curly long chain molecular structure of rubber and the weak secondary force between molecules; The rubber material has unique viscoelastic properties, so it has good shock absorption, sound insulation and cushioning properties. Rubber parts are widely used to isolate vibration and absorb impact, because they have the characteristics of hysteresis, damping and reversible large deformation.
The hysteresis and internal friction characteristics of rubber are usually expressed by loss factors. The greater the loss factor, the more significant the damping and heat generation of rubber, and the more obvious the damping effect.
The loss factor of rubber material is not only related to the structure of rubber itself, but also related to temperature and frequency. At room temperature, the loss factors of natural rubber (NR) and cis polybutadiene rubber (BR) are small, the loss factors of styrene butadiene rubber (SBR), neoprene rubber (CR), ethylene propylene rubber (EPR), polyurethane rubber (PU) and silicone rubber are in the middle, and the loss factors of butyl rubber (HR) and nitrile butadiene rubber (NBR) are the largest.
There are generally 5 kinds of rubber materials used for shock absorption, namely NR, SBR and BR are ordinary rubber materials; NBR is used for oil resistant vulcanizates; CR is used for weather resistant vulcanizates; IIR is used for high damping vulcanizate; EPR is used for heat resistant vulcanizates. Although the loss factor of NR is small, it has the best comprehensive performance, excellent elasticity, good fatigue resistance, low heat generation, small creep, good adhesion with metal parts, cold resistance, electrical insulation and processing performance. Therefore, NR is widely used for shock absorption purposes. When low temperature resistance or weather resistance is required, it can be used in combination with BR or CR or modified by blending. Nishiue and other shock absorbers made of NR, BR and metal salts containing – OH group organic acid with carbon atom number greater than 4 have good durability at 70 ℃ × 22h and 40 ℃ × The compression set at 148h is 17.0% and 11.7% respectively.
Rubber shock absorption products mainly include rubber shock absorption pads, rubber air springs, rubber fenders (see the color picture), sponge and cork rubber shock absorption pads, elastic couplings and flexible pipes. For example:
① Rubber shock pad. Most of them are rubber and metal composite products, including double plate, cylindrical, sheet and other forms, which are used for shock absorption and sound insulation of various machinery, instruments, axles and pipelines.
② Rubber air spring. It has better shock absorption and impact resistance than metal spring and is mainly used for vehicles. Its structure is similar to that of tubeless tire. The tire cord is used as the pressure resistant layer, with an air tight rubber layer inside and an oil resistant and aging resistant protective rubber layer outside.
③ Rubber mount. It is made of rubber sheet and rigid material (steel plate, steel wire mesh, canvas). The latter can improve the compressive strength of the bearing, but has little effect on the shear strength. Rubber bridge bearings can transfer bridge loads to piers and abutments, adapt to bridge deformation and reduce vibration. Rubber building support can reduce the impact of subway and surrounding vehicles and earthquake on buildings.