Mold costs depe…
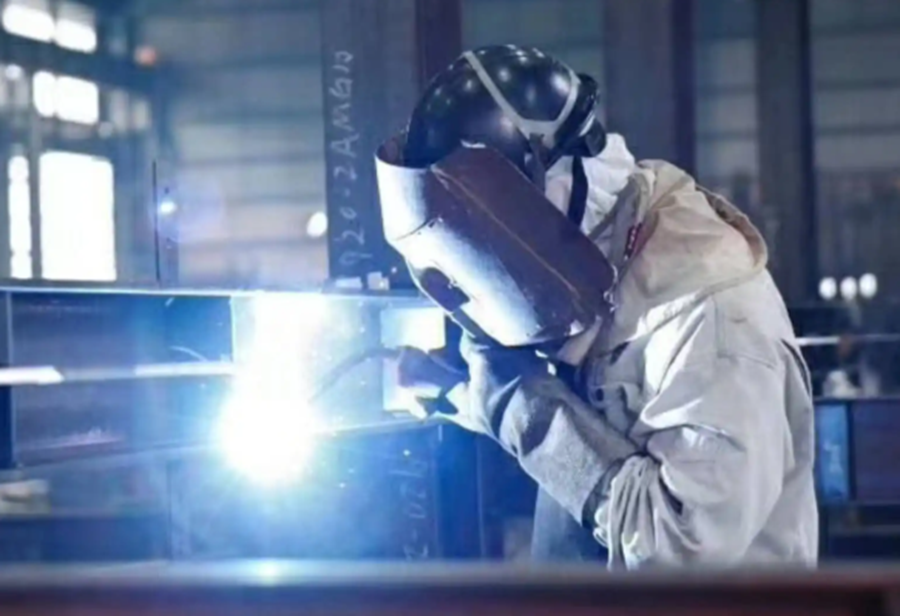
Prevention method of welding deformation of steel structure
As the main technology of steel structure fabrication and connection, welding has been widely used in the fabrication and installation of steel structures. However, the deformation problem generated in welding not only affects the appearance and service performance of steel structures, but also even leads to the scrapping of weldments if it is serious, causing direct economic losses to enterprises. Especially in the welding of large steel structures, this problem is particularly prominent. In view of this, it is necessary to comprehensively analyze the different types and causes of welding deformation, and take effective measures to control the amount of welding deformation, so as to ensure continuous improvement of production efficiency and steel structure engineering quality, and reduce enterprise production costs.
Analysis of basic types and causes of welding deformation
Basic types of welding deformation:
The so-called welding deformation refers to the deformation caused by the high temperature of the welding arc during the welding process of the steel structure and the residual deformation in the component after welding. In these two types of deformation, welding residual deformation is the main factor affecting the welding quality, and is also the most destructive type of deformation. The influence of welding residual deformation on different levels of structure can be divided into global deformation and local deformation; According to the different characteristics of deformation, it can be divided into angular deformation, bending deformation, shrinkage deformation, twist deformation, wave deformation and staggered deformation. Among these deformation types, angular deformation and wave deformation belong to local deformation, while other types of deformation belong to global deformation. The deformation type of steel structure is overall deformation.
Analysis on causes of welding deformation:
Steel structure stiffness: stiffness refers to the resistance of the structure to tensile direction and bending deformation. The rigidity of steel structure mainly depends on the shape and size of the structure section. For example, the deformation of I-beam section and longitudinal truss mainly depends on the chord section size of its cross-sectional area. For another example, the bending deformation of I-shaped, T-shaped or other shapes of section steel mainly depends on the bending stiffness of the section. Position and quantity of welding joint: when the steel structure stiffness is insufficient, the position and quantity of welding joint shall be symmetrically arranged in the structure, and the welding sequence is reasonable, and the members can only produce linear deformation; When the welds are arranged asymmetrically, most of them are bending deformation. Welding process: the welding current is too large and the electrode diameter is too thick, which makes the welding speed slow and may lead to large welding deformation; When welding thick steel plate, the deformation caused by manual welding method is smaller than that caused by automatic welding method; When multi-layer welding process is adopted, the weld shrinkage deformation of the first layer is the largest, and the welding deformation of the second and third layers is 20% and 5% of that of the first layer respectively? 10%。 In other words, the more layers of multi-layer welding, the more obvious welding deformation; The shrinkage deformation of intermittent weld is smaller than that of continuous weld; The transverse shrinkage deformation of butt weld is 2 to 4 times larger than the longitudinal shrinkage deformation; When the welding sequence is improper or the partial components are not properly welded, the overall assembly and welding will easily lead to welding deformation. Therefore, in order to prevent welding deformation, reasonable process measures must be formulated during welding construction.
Prevention of welding deformation of steel structure
1 Structural design of welded joints
Control the number and size of welds. The number and size of steel structure welds are large, the heat input during welding is more, and the welding deformation is larger. Therefore, in the structural design of welded joints of steel structures, the number and size of welds shall be controlled to minimize welding deformation. ② Select the appropriate shape and size of the weld groove according to the welding process. The reasonable selection of weld groove formation and size shall ensure the full bearing capacity of the steel structure as a whole. Proper groove shape and size can further reduce the welding deformation of the structure by reducing the sectional area. ③ The position of the welded joint shall be at the symmetrical part of the member section. The position of the welding node of the neutral axis of the structure shall be as symmetrical as possible in the neutral axis of the member section, or as close to the neutral axis as possible, and at the same time, it shall be avoided in the high stress zone. ④ For the selection of joint form, the joint form with small rigidity shall be selected. The nodes shall be avoided at the intersection of two-way and three-way, so as to avoid high temperature and weld stress concentration caused by weld concentration, thus reducing welding deformation.
2 Process measures
Assembly and welding sequence. The steel structure shall be fabricated and assembled on a standard horizontal plane. The platform shall ensure that the degree of dead weight pressure it is subjected to is large enough to avoid instability and sinking of steel members, so as to meet the basic requirements of member assembly. The welding of small components can be completed at one time, that is, after the fixed position is welded, the assembly is completed with appropriate welding sequence. However, the assembly and welding of large steel structures need to complete the welding of small parts before the final assembly and welding. During the assembly of components, in order to prevent excessive production during the assembly process.