Mold costs depe…
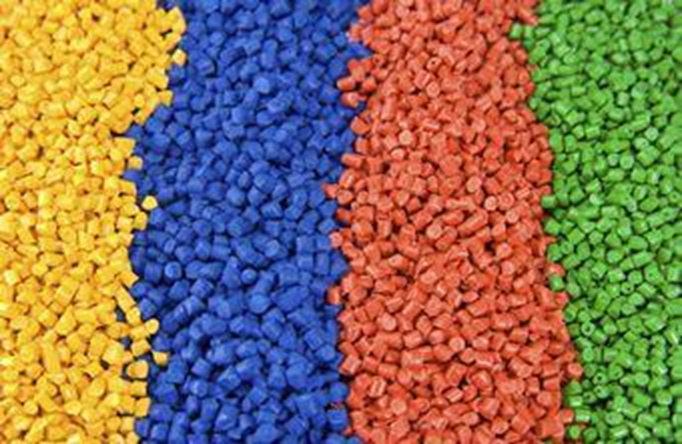
Molding process of PPO plastic raw materials
1) Amorphous materials have low moisture absorption, and the water absorption of PPO is very low. However, the moisture will cause defects such as silver wire and bubble on the surface of the product. Therefore, the raw materials can be put in an 80~OOC oven and dried for 1-2 hours before use.
2) The molecular bonds of PPO are rigid, the glass transition temperature is high, and it is difficult to orient, but it is difficult to relax after forced orientation. Therefore, the residual internal stress in the product is relatively high, which generally requires post-processing.
3) PPO is an amorphous material, and its rheological property in molten state is close to Newtonian fluid, but it deviates from Newtonian fluid to a greater extent with the increase of temperature.
4) The viscosity of PPO melt is large, so the temperature should be increased and the injection pressure should be appropriately increased during processing to improve the filling ability.
5) The recycled PPO can be reused for 3 times, and its performance is not significantly reduced.
6) For PPO melt, screw injection molding machine should be used, and straight through nozzle is preferred, with hole diameter of 3-6mm
7) During PPO injection molding, high pressure and high speed injection should be adopted, and the pressure holding and cooling time should not be too long.
8) The main runner of the mold should adopt a larger taper or a draw hook, and the runner should be short and thick.
9) The gate should be direct, fan-shaped or flat, and the diameter should be appropriately increased when needle shaped gates are used. For long gates, the hot runner structure can be used.
10) The molding shrinkage of PPO is small, generally 0.2% – 0.7%, so the dimensional stability of products is excellent.
11) Poor fluidity, similar to Newtonian fluid, viscosity is sensitive to temperature, and the product thickness is generally above 0.8mm. It is easy to decompose, and corrosive gas is generated during decomposition. The molding temperature should be strictly controlled, the mold should be heated, and the feeding system should have little resistance to the material flow.
12) The water absorption rate of polyphenylene oxide is very low about 0.06%, but a small amount of water will lead to silver wire and other unsmooth phenomena on the surface of the product. It is better to dry the product, and the temperature should not be higher than 150 degrees, otherwise the color will change.
13) The molding temperature of polyphenylene oxide is 280-330 ℃, and the molding temperature of modified polyphenylene oxide is 260-285 ℃. PPO plastic raw material injection molding process Melting temperature: 270-290 ℃
Constant temperature of barrel: PPO has high heat resistance, thermal decomposition temperature reaches 350C, and there is no obvious thermal degradation within 300C. Generally, the barrel temperature is controlled at 260~290C, and the nozzle temperature is about lOC lower than the barrel temperature.
Mold temperature: Due to the high viscosity of PPO melt, higher mold temperature should be adopted during injection molding. Generally, the mold temperature is controlled at 100~15OC. When the mold temperature is lower than 1 ℃, the thin-walled plastic parts are prone to underfill and delamination; When it is higher than 15OC, bubbles, silver wire, warpage and other defects are easy to appear.
Injection pressure: increase the injection pressure, which is conducive to the filling of molten materials. Generally, the injection pressure is controlled at 100-14OMPao. Pressure maintaining pressure: 40% – 60% of the injection pressure
Back pressure: 3-10 MPa (30-100bar)
Injection speed: products with long runner need rapid injection; However, in this case, ensure that the membrane has sufficient aeration.
Screw speed: medium screw speed, converted into linear speed of 0.6m/s
Metering stroke: 0.5-3.5D
Residue amount: 3-6mm, depending on metering stroke and screw diameter.
Pre drying: drying at 110 ℃ for 2h.
Recovery rate: the material can be recycled and processed as long as the recycled material does not undergo thermal degradation.
Shrinkage: 0.8% – 1.5%
Gate system: point type or latent gate shall be used for small products, otherwise, straight gate or wafer gate shall be used; The heating system can be shut down during the shutdown period of the hot runner machine; Under the back pressure of the bottom screw, operate several metering cycles, and empty the barrel like an extruder.
Barrel equipment: standard screw, check ring, straight nozzle.