Mold costs depe…
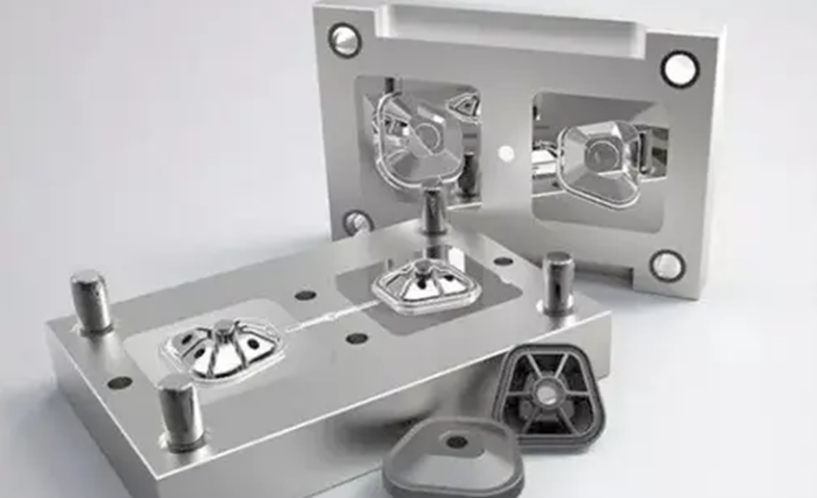
Mold temperature in injection molding easily affects the molding cycle and quality
During injection molding, the mold temperature is easy to affect the molding cycle and molding quality. In actual operation, it is set from the lowest appropriate mold temperature of the material used, and then adjusted appropriately according to the quality status. Die temperature refers to the temperature on the surface of the die cavity when forming is being carried out. In terms of die design and the setting of forming engineering conditions, it is important not only to maintain an appropriate temperature, but also to make it evenly distributed. Uneven mold temperature distribution will lead to uneven shrinkage and internal stress, so that the forming mouth is prone to deformation and warping.
The following effects can be obtained by increasing the mold temperature:
① The crystallinity and more uniform structure of the additive products.
② The molding shrinkage is sufficient and the post shrinkage is reduced.
③ Improve the strength and heat resistance of molded products.
④ Reduce residual internal stress, molecular alignment and deformation.
⑤ It can reduce flow resistance and pressure loss during filling.
⑥ Make the appearance of the formed products shiny and good.
⑦ Increase the chance of forming product burrs.
⑧ Increase the chance of near gate and reduce the chance of depression in far gate.
⑨ Reduce the degree of apparent binding line
⑩ Increase the cooling time. Injection molding mold temperature