Mold costs depe…
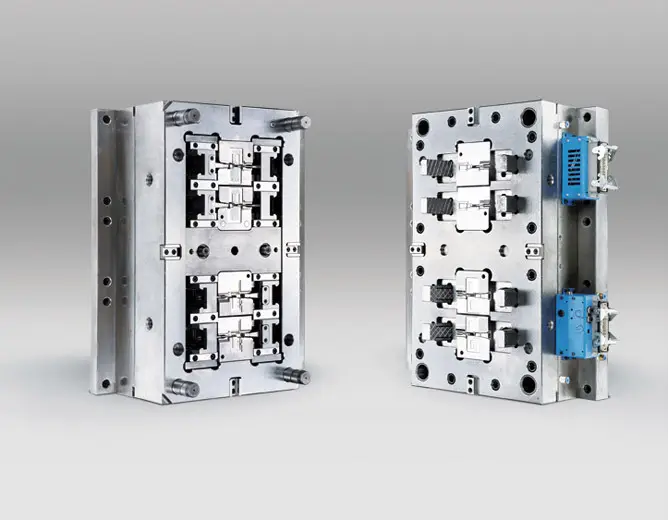
Mold knowledge points
1、 Mold kernel and mold embryo
1. Before the mold embryo is disassembled, check whether its model and size conform to the drawing, and then mark the mold number and template serial number on the diagonal of the reference angle. It is required to mark the mold number on the square iron mill of each set of mold; Each set of mold guide pillar must also be engraved with mold number with a grinder; The bottom of the guide sleeve is provided with an exhaust groove; The four corners of plate B require the skid pit to be milled, with the size of 20 * 45 ° * DP5.
2. When multiple products are in the same set of mold, the principle of large intermediate products and small peripheral products should be followed, that is, the products where the pressure is located should be placed in the middle, so that the glue of the whole set of mold is evenly distributed. Products requiring electroplating and the same products shall be concentrated together, and products requiring oil injection shall be concentrated together.
3. The parting surface shall be smooth and beautiful, and the appearance surface of the new mold shall not be scratched or rusted as much as possible to ensure that the mold is beautiful and tidy. The rear mold core shall be flat, and the CNC machining knife pattern shall not be damaged as much as possible. The front mold dart must be polished in the order of rough chiseling and fine chiseling, coarse oilstone and fine oilstone, coarse sandpaper and fine sandpaper (the patterned parts need not be polished).
4. Under the condition that the product ejection is not affected and the strength of the ejector plate is guaranteed, it is required that the die is stressed evenly and the supporting head is mainly considered in the middle of the die. Support head length: mold below 3535, support head height is square iron height plus 0.15-0.2mm; The height of the formwork head above 3535 is square iron height plus 0.2-0.3mm, and the head is generally fixed on the bottom plate or B plate.
5. After the product appearance or product assembly is completed, the place that can be touched by the operator’s hand shall not be favorable.
6. The nozzle shall be positioned and stopped, and the rubber outlet shall have a flat parting surface of 0.5-1.0mm. The length of the nozzle should be as short as possible to reduce the injection force. The nozzle locating step surface shall not contact the mold core or insert.
7. The ejector pin hole and nozzle hole of the mold must be on the same center, and the diameter of the ejector pin hole is Φ 40. There are three molds with the mold embryo above 3555 according to the injection molding machine, and the number of centers is 100. The ejector base plate is required to be evenly set with garbage nails, and the height of garbage nails must be consistent.
8. All molds must be machined with die groove, and the center distance is 7 inches, 10 inches, 12 inches. The straight body mold is required to mill the die pit, which is 25 deep, 25 wide, and the length depends on the size of the template.
9. The mold core and large insert of all molds shall be cooled and transported with water, especially where the glue level is deep and thick. The diameter of the waterway is 8.0mm, and the larger one can be Φ 10, extra large Φ 12. The safety distance is 4.0mm, and the distance from the glue position shall be at least 6.0mm. The local mold temperature shall not be too high as far as possible. Steps must be made at the copper blocking position of the water path. The mold core and the cooling water path of the insert shall be connected from the mold embryo with a waterproof ring, such as the front mold through the frame. The water pipe can be directly connected to the panel of the mold embryo through the mold core (the mold cannot be opened between the panel and the A plate). The water inlet and outlet pipes are generally set at the non side for operation. The water inlet pipes of the water pipes are engraved with ‘IN1’ and ‘IN2’, and the water outlet pipes are engraved with ‘OUT1’ and ‘OUT2’.
10. Avoid welding parts at obvious appearance.
11. When finishing the front and rear mold frames, first correct the perpendicularity between the milling machine spindle and the worktable to ensure the tolerance of ± 0.01mm; The bottom of the frame is required to be milled with a flying knife, and the corners around the frame are required to be less than or equal to Φ 12. The milling cutter shall be free of 0.1 to ensure that the bottom of the frame is flat in a large area. The front and rear die block diagrams are required to be on the same center with a tolerance of ± 0.01mm. Under the mold core, it is required to use red lead to check whether there is a large area of contact.
12. Grind the front and rear die insert with an angle ruler with a tolerance of ± 0.02 and consistent length and width; A groove is milled on the side of the mold insert, and the datum symbol DUTAM and mold number are engraved. The position corresponds to the datum angle of the mold embryo. In general, the front and rear mold core requires that the thimble and the needle hole be inserted first; After the threading hole is processed, it can be processed by CNC or wire cutting.
13. For all machined workpieces, all tools to be used for the workpieces must be prepared in advance. The fixture can be processed on the machine tool at one time. It is required that the workpieces can only be unloaded after all the workpieces have been inspected to prevent repeated machining.
14. Before electric discharge machining, all electrodes must be checked to see if their shape is consistent with the drawing (corner cleaning part), and their size must be equal to the drawing size * shrinkage spark position die saving allowance (except for the left lines). Wechat of the mold engineer: 1828765339 requires that the discharge part of the copper tool should pass 400 # sandpaper to save light, and no knife lines or molybdenum wire traces should be left; The datum position shall be smooth and flat without burrs and sharp corners.
15. All spark, wire cutting, CNC and engraving processes must be carefully checked and confirmed to be correct before the next process.
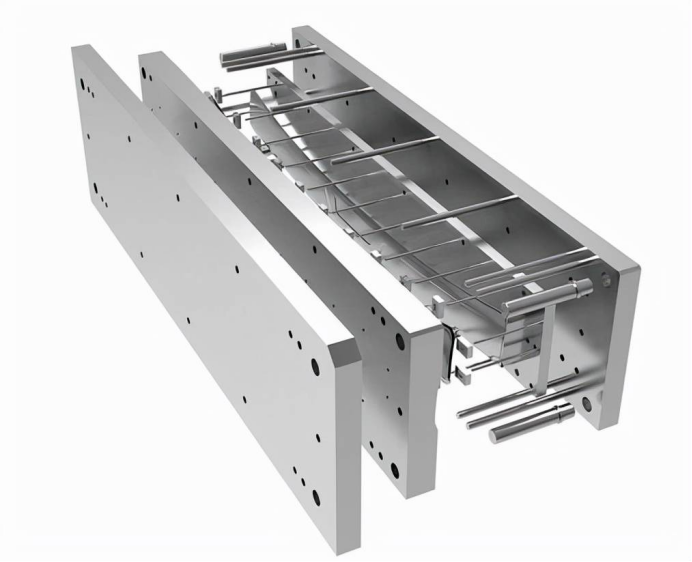
2、 Structure
1. All moving parts of the mold, such as line position, inclined roof, push block, push plate, etc., shall be provided with gradient sealant and gradient matching. Oil grooves shall be provided at the positions of mutual friction, and the hardness of steel used shall not be lower than that of the mold core.
2. All mold shovels must be machined with a grinder, and cannot be machined with a grinder. The slope of the inclined guide pillar is required to be 2 ° less than the slope of the shovel foundation, and the shovel foundation requires a backhoe.
3. If the width of large travel space exceeds 200mm, a guide mechanism shall be set in the middle, and bronze is generally used as the guide block.
4. For products formed by the collision of rows and positions, rows and positions are required to be limited by interlocking steps.
5. The guide block of the row position shall be designed on the template as far as possible, and the pressure blocks on both sides of the row position.
6. At the position where the front formwork has a relatively large wrapping force, the needle shall be uniformly set at the corresponding rear formwork position. The needle shall be positioned and all needle directions shall be consistent to facilitate demoulding.
7. The inserts shall be positioned with hanging platform or fixed with screws, and shall not be loosened after the mold is installed.
8. The R angle matching the mold core and the mold frame cannot be tightly matched, and must be kept away from the void. The bottom surface requires a milling cutter to chamfer the C angle of 2 * 45 °. The R angle matching the mold frame requires: R frame+1=R mold core.
3、 Runner
1. On the premise of ensuring the forming quality, all molds should try to shorten the travel of the flow channel and reduce the cross-sectional area as much as possible. The cold material cavity should be 1.5 times the diameter of the flow channel. All flow channels should have cold material cavities, such as the lower part of the nozzle, the end of the flow channel, and the lower part of the fine water inlet.
2. All fine nozzle molds, mold runner and nozzle needle must be polished. The rubber inlet shall be smooth, the injection pressure shall be reduced and no residue shall be left on the product.
3. The runner section of the large spout die shall be made into a circle or upper and lower ellipses, that is, the height dimension shall be 0.5-1.0 larger than the width dimension, and the front and back must be aligned. There shall be no dislocation in polishing. Under special circumstances, the single-sided runner is required to be trapezoidal.
4. The material inlet and water inlet shall not be at the obvious appearance. The glue inlet point of the electroplating product shall ensure the strength. The contact between the glue inlet point of the big water inlet and the product shall be the knife edge surface with the smallest cross sectional area. It shall be ensured that there is no residue left on the product after removal.
5. The position of the thimble or needle of the submersible rubber inlet shall be a certain distance from the rubber inlet of the parting surface, which is about 1.5 times the diameter of the runner, to ensure the toughness of the submersible rubber inlet. The submersible gate must be polished. 6. The glue inlet point of the gear die is at the bottom of the tooth surface Φ The 1.0 milling cutter shall align the sharp point of one of the teeth with a milling depth of 0.5-0.6, a width of 1.2, a depth of 1.5, and an AB plate insert. When the inserted through holes need to be processed together, if they are not inserted, they need to be divided repeatedly with the centering rod to ensure the concentricity accuracy. For the insertion of the rear die barrel pin and the front die, a drill bit smaller than the machining hole diameter must be used for roughening, so as to facilitate the copper discharge machining.
4、 Ejection system
The distribution of thimble shall be reasonable and uniform, and the thimble shall be close to the difficult demoulding position and the deeper bone position as far as possible to prevent the white deformation of the product top; The product is the thimble at the inclined plane or circular arc surface. The driver cylinder and the driver cylinder needle must have a stop structure, and the end face is parallel to the inclined plane or circular arc surface of the product. The distance between the outer circle of the thimble and the edge of the rubber position shall be 1.0-1.5 mm if the size of the thimble is within 5 mm; 5-10mm, the difference is 1.5-2.0mm; The difference is about 2.5mm above 10mm.