Mold costs depe…
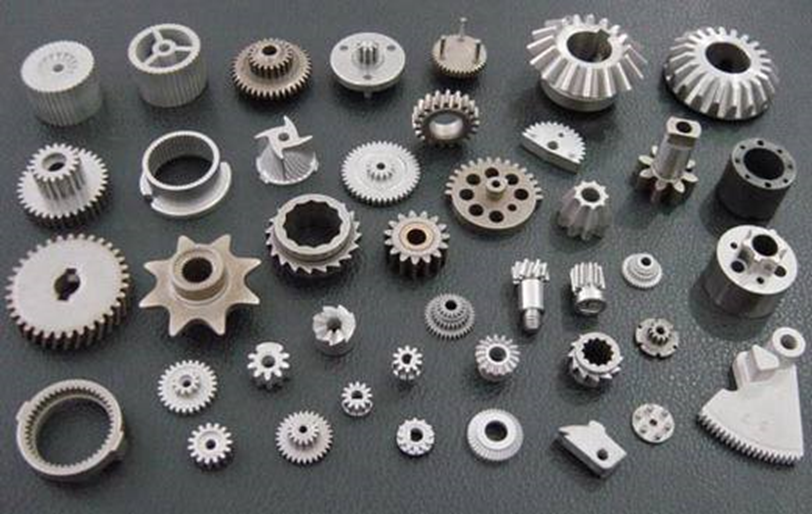
Metal powder injection molding technology (MIM for short)
Metal Powder Injection Molding (MIM) is a new powder metallurgy near net shape forming technology that introduces modern plastic injection molding technology into the field of powder metallurgy. The basic technological process is as follows: first, the solid powder and organic binder are uniformly mixed, then granulated, injected into the mold cavity with an injection molding machine under the heating and plasticizing state (~150 ℃) for curing and forming, and then the binder in the forming blank is removed by chemical or thermal decomposition methods, and finally the final product is obtained through sintering and densification. Compared with the traditional process, it has the characteristics of high precision, uniform organization, excellent performance, low production cost, etc. Its products are widely used in electronic information engineering, biomedical equipment, office equipment, automobiles, machinery, hardware, sports equipment, clocks, weapons, aerospace and other industries. Therefore, it is generally believed internationally that the development of this technology will lead to a revolution in the forming and processing technology of parts and components, known as “the hottest part forming technology today” and “the forming technology of the 21st century”.
Parmatech, a company in California, USA, invented the technology in 1973. In the early 1980s, many European countries and Japan also invested a lot of energy in the research of the technology, which was rapidly promoted. Especially in the mid-1980s, this technology has achieved rapid development since its industrialization, increasing at an alarming rate every year. So far, more than one hundred companies in more than ten countries and regions, such as the United States, Western Europe and Japan, have been engaged in the product development, development and sales of this technology. Japan is very active and outstanding in competition. Many large companies have participated in the promotion of the MIM industry, including Pacific Metal, Mitsubishi Steel, Kawasaki Steel, Kobe Steel, Sumitomo Mine, Seiko Epson, Datong Special Steel, etc. At present, there are more than 40 companies specializing in the MIM industry in Japan, and the total sales value of their MIM industry products has already exceeded that of Europe and directly followed the United States. So far, more than one hundred companies have been engaged in the product development, research and sales of this technology in the world. Therefore, MIM technology has become the most active frontier technology field in the new manufacturing industry. It is a pioneering technology in the world’s metallurgical industry and represents the main direction of powder metallurgy technology development.
Metal powder injection molding technology is a product of the penetration and intersection of many disciplines, such as plastic molding technology, polymer chemistry, powder metallurgy technology and metal materials science. It can use mold to inject and shape blanks and rapidly manufacture high-density, high-precision, three-dimensional complex structural parts through sintering. It can quickly and correctly materialize design ideas into products with certain structural and functional characteristics, and can directly produce parts in batches, It is a new change in the manufacturing technology industry. This process technology not only has the advantages of less conventional powder metallurgy processes, no cutting or less cutting, and high economic benefits, but also overcomes the shortcomings of traditional powder metallurgy products, uneven materials, low mechanical properties, difficult to form thin walls, and complex structures. It is especially suitable for mass production of small, complex and metal parts with special requirements. Technological process: binder → mixing → injection molding → degreasing → sintering → post-treatment.
Powder metal powder
The particle size of metal powder used in MIM process is generally 0.5~20 μ m; Theoretically, the finer the particles are, the larger the specific surface area is, which is easy to form and sinter. The traditional powder metallurgy process uses more than 40 μ M coarse powder.
organic adhesive
The function of the organic adhesive is to bond the metal powder particles, so that the mixture has rheological and lubricating properties when heated in the barrel of the injection machine, that is, the carrier that drives the powder activity. Therefore, the choice of adhesive is the carrier of the whole powder. Therefore, the selection of adhesion is the key to the whole powder injection molding. Requirements for organic adhesives:
1. Less dosage and less adhesive can make the mixture have better rheology;
2. No reaction, no chemical reaction with metal powder in the process of removing adhesive;
3. It is easy to remove and there is no carbon residue in the products.
Mixture
The metal powder and the organic adhesive are uniformly mixed together to make various raw materials become the mixture for injection molding. The homogeneity of the mixture directly affects its mobility, thus affecting the injection molding process parameters, even the ultimate material density and other properties. The process of injection molding in this step is consistent with that of plastic injection molding in principle, and its equipment conditions are basically the same. In the injection molding process, the mixture is heated into a plastic material with rheological property in the barrel of the injection machine, and is injected into the mold under appropriate injection pressure to form the blank. The injection molded blanks shall be uniform in microcosm, so as to make the products shrink uniformly in the sintering process.
extraction
Before sintering, the formed blank must remove the organic binder contained in the blank. This process is called extraction. The extraction process must ensure that the adhesive is gradually discharged from different parts of the blank along the micro channel between the particles without reducing the strength of the blank. The elimination rate of binder generally follows the diffusion equation. Sintering and sintering can make porous degreased blanks shrink to densification and become products with certain structures and properties. Although the properties of products are related to many process factors before sintering, in many cases, the sintering process has a great, even decisive influence on the metallographic structure and properties of the final products.
Post processing
For parts with relatively precise size requirements, necessary post-processing is required. This process is the same as the heat treatment process of conventional metal products.
Characteristics of MIM process Comparison between MIM process and other processing processes
The particle size of raw material powder used by MIM is 2-15 μ m. However, the particle size of traditional powder metallurgy raw powder is mostly 50-100 μ m。 The high density of finished products in MIM process is due to the use of fine powder. The MIM process has the advantages of the traditional powder metallurgy process, but the high degree of freedom in the shape can not be achieved by the traditional powder metallurgy process. Traditional powder metallurgy is limited to the strength and filling density of the mold, and the shape is mostly two-dimensional cylindrical.
The traditional precision casting drying process is an extremely effective technology for making products with complex shapes. In recent years, the finished products with narrow slots and deep holes can be completed with the aid of ceramic cores. However, due to the strength of ceramic cores and the limitation of the mobility of casting liquid, this process still has some technical difficulties. Generally speaking, this process is more suitable for manufacturing large and medium-sized parts, while the MIM process is more suitable for small and complex shaped parts. Compare the project manufacturing process MIM process Traditional powder metallurgy process Powder particle size( μ m) 2-1550-100 Relative density (%) 95-9880-85 Product weight (g) is less than or equal to 400g 10 – hundreds of three-dimensional complex product shapes.
Mechanical properties of two-dimensional simple shape
Comparison between MIM process and traditional powder metallurgy die-casting process is used for materials with low melting point and good casting liquid activity, such as aluminum and zinc alloys. The strength, wear resistance and corrosion resistance of the products produced by this process are limited due to the limitation of materials. MIM process can process many raw materials.
Although the precision and complexity of the investment casting process have improved in recent years, it is still inferior to the dewaxing process and the MIM process. Powder casting is an important development and has been applied to the mass production of connecting rods. But generally speaking, the cost of heat treatment and the service life of the mold in the casting engineering still have problems, which need to be further solved.
The traditional mechanical processing method, which has recently improved its processing ability by relying on automation, has made great progress in effect and accuracy, but the basic program is still inseparable from the gradual processing (turning, planing, milling, grinding, drilling, polishing, etc.) to complete the part shape. The machining accuracy of the machining method is far better than that of other machining methods. However, due to the low effective utilization rate of materials, and the completion of its shape is limited by equipment and tools, some parts cannot be machined. On the contrary, MIM can effectively use materials without restrictions. For the manufacturing of precision parts with small and difficult shapes, MIM process is less costly and more efficient than mechanical processing, and has strong competitiveness.
MIM technology does not compete with traditional processing methods, but makes up for the shortcomings of traditional processing methods in technology or cannot be made. MIM technology can play its specialty in the field of parts made by traditional processing methods. MIM technology has the technical advantage in parts manufacturing, which can form highly complex structural parts.
The injection molding process technology uses the injection machine to inject the product blank, ensuring that the materials are fully filled with the mold cavity, which also ensures the realization of the highly complex structure of the parts. In the past, in the traditional processing technology, individual components were made first and then combined into components. When using MIM technology, it can be considered to integrate into a complete single part, greatly reducing steps and simplifying processing procedures. Compared with other metal processing methods, MIM has high dimensional accuracy, requiring no secondary processing or only a small amount of finishing.
The injection molding process can directly form thin-walled and complex structural parts. The product shape has approached the ultimate product requirements, and the dimensional tolerance of parts is generally maintained at ± 0.1 – ± 0.3. In particular, it is of great significance to reduce the processing cost of cemented carbides that are difficult to machine, and to reduce the processing loss of precious metals.
The product has uniform microstructure, high density and good performance
During the pressing process, the friction between the mold wall and the powder, as well as between the powder and the powder, makes the pressing pressure distribution very uneven, which leads to the uneven microstructure of the pressed blank. This will cause uneven shrinkage of the pressed P/M parts during the sintering process. Therefore, the sintering temperature has to be reduced to reduce this effect, so that the porosity of the products is large, the density of the materials is poor, and the density is low, It seriously affects the mechanical properties of products. On the contrary, the injection molding process is a fluid molding process. The existence of the adhesive ensures the uniform distribution of the powder, which can eliminate the inhomogeneity in the blank microstructure, and then make the sintered product density reach the theoretical density of its material. Generally, the maximum density of pressed products can only reach 85% of the theoretical density. The high compactness of the products can increase the strength and toughness, improve the ductility, conductivity and thermal conductivity, and improve the magnetic properties. High efficiency, easy to achieve mass production and large-scale production.
The life of the metal mould used in MIM technology is equivalent to that of the engineering plastic injection mould. Because of the use of metal dies, MIM is suitable for mass production of parts. Because the injection molding machine is used to shape the product blank, the production efficiency is greatly improved, the production cost is reduced, and the consistency and repeatability of the injection molding products are good, thus providing a guarantee for mass and large-scale industrial production. Wide range of applicable materials,
Wide application fields (iron base, low alloy, high-speed steel, stainless steel, gram valve alloy, hard alloy)
The materials that can be used for injection molding are very wide. In principle, any powder materials that can be cast at high temperature can be made into parts by the MIM process, including the difficult to machine materials and high melting point materials in the traditional manufacturing process. In addition, MIM can also research the material formula according to the user’s requirements, manufacture any combination of alloy materials, and shape the composite materials into parts. The application fields of injection molded products have spread throughout all fields of the national economy and have broad market prospects.
Performance and cost analysis of injection molded products:
The MIM process uses micron fine powder, which can not only accelerate the sintering shrinkage, help improve the mechanical properties of materials, extend the fatigue life of materials, but also improve the stress corrosion resistance and magnetic properties.
Note: * For hard and brittle materials that are difficult to cut, or parts with complex geometric shape and segregation or pollution of raw materials during casting, MIM process can greatly save costs. Take the processing of the guide rod of the printing element of the typewriter as an example, it usually requires 14 processes that can go up and down; The MIM process only requires 6 processes, which can save about half of the cost. When the ratio of material cost/manufacturing cost increases, the latent cost can be reduced even more. Therefore, the smaller and more complex the parts are, the better the economic benefits will be. From the above analysis, we can see that the potential of MIM molding is great.
Application fields of MIM technology:
1. Computer and its auxiliary facilities: such as printer parts, magnetic core, striker shaft pin, drive parts.
2. Tools: such as drill bit, cutter head, nozzle, gun drill, spiral milling cutter, punch, socket, wrench, electrical tools, hand tools, etc.
3. Household appliances: such as watch case, watch chain, electric toothbrush, scissors, fan, golf ball head, jewelry chain ring, ball pen clamp, cutting tool head and other parts.
4. Medical machinery parts: such as dental orthopedic frame, scissors, tweezers.
5. Military parts: missile tail, gun parts, warheads, shaped charge covers, fuse parts.
6. Electrical parts: electronic package, micro motor, electronic parts, sensor parts.
7. Mechanical parts: such as cotton loosening machine, textile machine, crimping machine, office machinery, etc.
8. Automobile and marine parts: such as clutch inner ring, fork sleeve, distributor sleeve, valve guide, synchronizing hub, airbag parts, etc.