Mold costs depe…
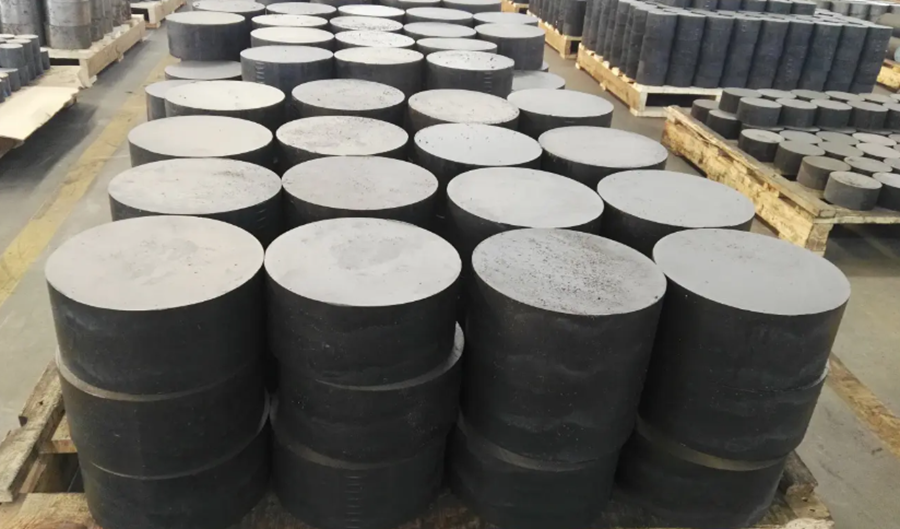
Melting Technique of High Grade Grey Cast Iron
High grade gray cast iron generally refers to gray cast iron above HT250. In the production process, it can be roughly divided into the following forms: one is inoculation cast iron; The other is alloy cast iron (rare earth gray cast iron is mainly introduced here). Now let’s talk about my own views and understanding on the two kinds of high grade gray cast iron casting.
1、 Inoculated cast iron
In gray cast iron, graphite exists in the form of flake, which seriously damages the properties of iron matrix. In order to improve the mechanical properties, the number of graphite flakes must be reduced. Inoculated cast iron essentially obtains higher mechanical properties by reducing the number of graphite flakes and adding an appropriate amount of inoculant to refine eutectic.
In grey cast iron, the main elements are C, Si, Mn, S and P. C, Si and P are elements that promote graphitization, while Mn and S are elements that hinder graphitization. In order to reduce the number of graphite flakes, it is necessary to reduce the content of C, Si and P, and increase the content of Mn and S. Therefore, the carbon equivalent CE=C+1/3 (Si+P) is generally low and belongs to hypoeutectic cast iron Sc<1. However, carbon exists in cast iron in two forms, one is free graphite; The other is the cementite in the combined state. If the carbon equivalent is too low, all the carbon in the cast iron will form cementite during the cooling process, making the cast iron a white cast iron with poor mechanical properties. Therefore, in the process of producing inoculant cast iron, chemical composition analysis should be carried out first to select appropriate carbon equivalent, so that a small amount of graphite exists in addition to forming cementite during the solidification process of carbon element, so that pearlite can appear in the internal structure of cast iron and high mechanical properties can be obtained.
In the actual production of inoculant cast iron, since silicon based inoculant is also added to the primary molten iron, the carbon equivalent CE of the primary molten iron is generally selected to be near the edge of the white cast iron zone or the pockmarked cast iron zone when selecting the composition of the primary molten iron, which depends on the brand of the inoculant cast iron produced, and then a small amount of inoculant will make the gray cast iron matrix present fine pearlite.
For Mn and S elements, they are both elements conducive to the formation of pearlite. Mn and S elements will also react in molten iron to form MnS dregs. Therefore, it is necessary to increase the content of Mn element in the production of inoculation cast iron. For S element, depending on the actual structure of the casting, the control range can be broadened when the casting does not produce cracks. In some cases, the content of S element can even be artificially increased.
As for the way of adding inoculant, one way is to add inoculant at the time of tapping, and the other way is to add inoculant with flow or in mold during pouring, which should be flexibly controlled according to the specific situation. Due to different inoculation methods, the addition amount of inoculant will also change.
The inoculation process is a short time effect on the original molten iron, so the pouring time of molten iron must be limited. If the pouring time is too long, the inoculation effect will be lost and the mechanical properties of the casting will be reduced.
2、 Rare earth alloy cast iron
When producing inoculant cast iron, a large amount of scrap steel needs to be added. If cupola is used for smelting, it may sometimes be difficult. Moreover, due to the development of casting industry, the supply of scrap steel falls short of demand, sometimes directly affecting production. Therefore, we must consider a new production plan to produce high grade gray cast iron without or with less scrap steel. This process is to use rare earth alloy to smelt high grade gray cast iron. First, let’s understand the role of rare earth alloys:
(1) Rare earth elements are strong desulfurizers.
(2) The residual rare earth elements in molten iron will change the graphite morphology of gray cast iron.
(3) Rare earth can increase the undercooling of cast iron crystallization, hinder the graphitization in the solidification process, and increase the white tendency.
Inoculated cast iron has low carbon equivalent, which belongs to hypoeutectic cast iron, but rare earth gray iron is not, which belongs to eutectic or hypereutectic cast iron. Because rare earth elements are added to hypoeutectic cast iron, eutectic graphite will precipitate between austenite dendrites during solidification. Because rare earth has a great effect on undercooling of cast iron during crystallization, this interdendritic graphite is often precipitated as undercooled graphite, so the mechanical properties are deteriorated. For eutectic or hypereutectic cast iron, the situation is different, and the structure of cast iron will change obviously after adding rare earth elements. When a small amount of rare earth alloy is added, the graphite is still flake, but the distribution is slightly uniform. When the rare earth alloy continues to increase to a certain value, the graphite shape will change dramatically. It becomes short and thick vermicular graphite with a small amount of pellet graphite. If rare earth elements continue to increase, the proportion of vermicular graphite will decrease, while the pellet graphite will gradually increase. When it reaches a certain extent, due to its strong supercooling effect, part of the ledeburite structure will appear in the matrix, and this change in structure will inevitably lead to changes in mechanical properties. If the amount of rare earth is increased on this basis, the amount of ledeburite in the matrix will increase and the mechanical properties will decline.
To sum up, in order to use rare earth elements to smelt high-grade gray cast iron, the two necessary conditions are:
First, the molten iron must be eutectic or hypereutectic, and its carbon equivalent CE=4.3% – 4.8%.
Secondly, a certain amount of rare earth elements must remain in the molten iron after being treated with rare earth alloys. After several determinations, the residual Re=0.06% – 0.1%.
Because rare earth is a strong desulfurizer, the content of S in molten iron treated with rare earth alloy is generally low, about 0.01% – 0.02%.
In addition, when smelting rare earth gray iron, in order to increase the pearlite content in the matrix, it is usually necessary to add a certain amount of Mn, which is generally 0.5% – 1.5%.
In actual production, in order to ensure the quality of rare earth gray iron, it is necessary to sample and inspect the treated molten iron before furnace, usually using triangular test block. The best one is that the top and both sides of the sample fracture are slightly shrunk, the fracture is silver gray, the structure is dense, the center is slightly shrunk, and the sample tip has a certain white mouth width. If the top and both sides of the triangular test block have large shrinkage dents, obvious central shrinkage porosity, silver gray fracture, and large white mouth width, it indicates that the rare earth alloy is added too much, and its addition amount should be reduced, and the inoculation should be strengthened; On the contrary, it indicates that the rare earth alloy addition is insufficient, and the rare earth alloy addition should be appropriately increased to make the white mouth width of the fracture reach a certain value.
After many tests, it is completely feasible to melt high grade gray cast iron with rare earth alloy, and its tensile strength is generally ≥ 350MPa.
The above are two methods for producing high-grade gray cast iron. Of course, there are other methods for smelting high-grade gray cast iron, such as adding a certain amount of Cu, Ni, Cr and other alloy elements to alloying the cast iron. In any case, only by constantly exploring and understanding new things in our work can we improve our professional knowledge and better serve production.