Mold costs depe…
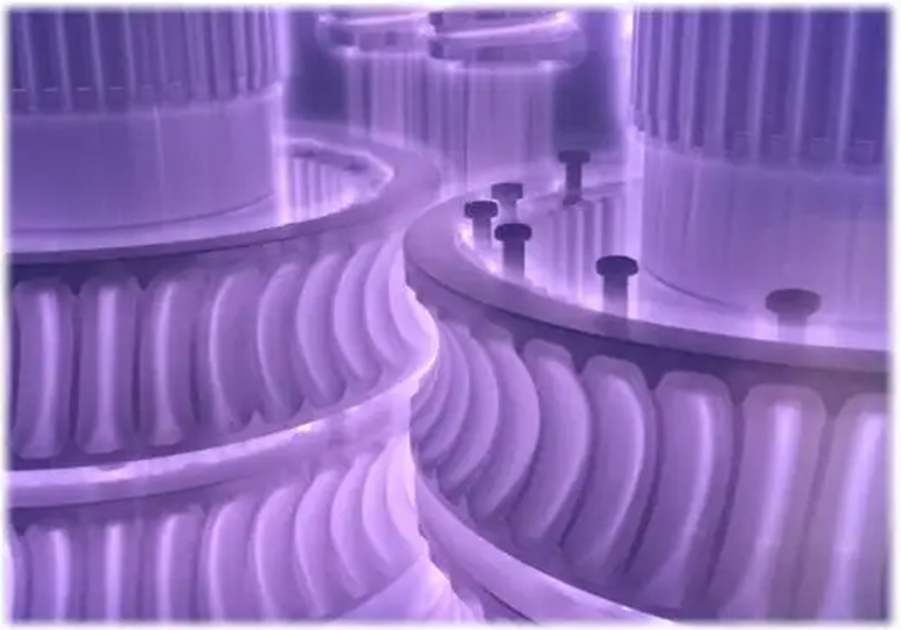
Ion nitriding process
There are many process parameters of ion nitriding. In addition to the common nitriding temperature and time, it is also related to furnace gas pressure, gas source, gas pressure and flow rate, voltage and current, gas extraction rate and other factors.
01 Nitriding temperature and time
1) The nitriding temperature of ion nitriding is basically the same as that of gas nitriding, generally 500~540 ℃. There is an optimal corresponding value between the nitriding hardness and temperature of different materials, generally 450~540 ℃. When the temperature is higher than 590 ℃, the hardness will decrease significantly due to the accumulation of nitride.
The heating rate mainly depends on the current density of the workpiece surface, the ratio of the workpiece volume to the surface area generating glow, the complexity of the workpiece and the heat dissipation conditions. In order to reduce deformation, the heating rate should not be too fast, generally 150~250 ℃/h. The insulation temperature shall be stable and the fluctuation shall be small. The stability of the insulation temperature is closely related to the furnace pressure and voltage. The current density is stabilized by stabilizing the furnace pressure, thereby improving the stability of the insulation temperature; The current density is stabilized by stabilizing the voltage, thereby improving the stability of the insulation temperature.
2) The heat preservation time of nitriding depends on the material of nitriding parts, the thickness and hardness of nitriding layer, and the heat preservation time ranges from tens of minutes to tens of hours. When the nitriding time is less than 20h, the rate of ion nitriding is obviously higher than that of gas nitriding. When the nitriding time is more than 20h, the two nitriding rates are close. It can be seen that ion nitriding is the most appropriate method to treat workpieces with nitriding layer less than 0.5mm. When the nitriding layer depth is 0.2~0.5mm, the heat preservation is generally 8~20h.
02 Boiler gas pressure
Furnace gas pressure is an important parameter of ion nitriding. After the furnace is empty or the workpiece is loaded, the air pressure should be below 6.67Pa. If this value is not reached, it indicates that there is air leakage in the furnace body, and the oxygen in the leaked air will oxidize the metal surface during nitriding, affecting the nitriding quality; Air leakage during cooling will cause oxidation color of the workpiece.
The furnace gas pressure is related to the gas supply flow and the gas extraction rate. Under the condition of a certain air pressure, the greater the pumping rate of the vacuum pump, the greater the gas flow and the greater the ammonia consumption. In ion nitriding, air pressure directly affects the current density. The air pressure is high, the current density is high, and the current density affects the heating rate and insulation temperature. In actual operation, the air pressure should be 133~1066Pa, generally 266~800Pa.
The furnace gas pressure has a certain effect on the structure of the nitriding layer. In the compound layer under high pressure ε High phase content, easy to obtain with low gas pressure γ′ Phase. When the air pressure is 40~2660Pa, the compound layer is not easy to appear.
The pressure also determines the thickness of the glow layer. The higher the pressure, the smaller the dk, and the thinner the glow layer, which is more conducive to temperature rise.
03 Voltage
The voltage required by ion nitriding is related to factors such as furnace gas pressure, current density, workpiece temperature and the distance between cathode and anode. When other factors are constant, the current density increases with the increase of voltage; When the air pressure increases, the voltage decreases. In actual operation, the current is controlled by adjusting the voltage and air pressure to achieve the purpose of temperature rise and insulation. The voltage in the insulation stage is generally 500~700V.
04 Current density
The current density directly affects the amount of heat supplied to the workpiece, which is mainly selected according to the requirements of nitriding temperature. In the heating stage, more heat is needed and the current density is large; In the heat preservation stage, less heat is required and the current density is smaller. The current density is generally 0.5~20mA/cm ² 0.5~3mA/cm ²。
05 Air source
Ammonia gas is generally used as the gas source for ion nitriding, which is directly introduced into the furnace for nitriding. It is simple to operate and convenient to use. Ammonia can also be decomposed into nitrogen and hydrogen at 660~670 ℃ and then passed into the nitriding furnace; The mixed gas of nitrogen and hydrogen can also be used as the gas source. The latter two gas sources can obtain a more uniform temperature distribution and nitriding layer than when ammonia gas is directly used. The desired nitriding layer structure and ε The thickness of the phase layer. The volume ratio of nitrogen and hydrogen can vary from 1:9 to 9:1. The larger the proportion of hydrogen, the more ε The thinner the phase layer is.