Mold costs depe…
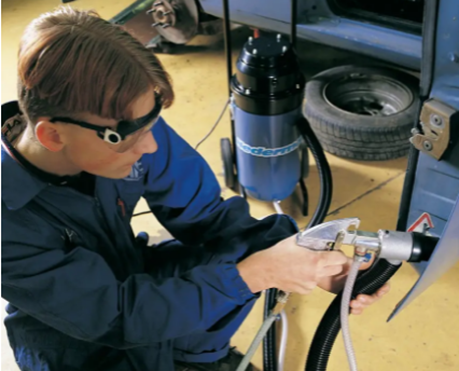
Introduction to sand blasting rust removal technology
◆ common sense of sand blasting and rust removal
Sand blasting and rust removal is to use compressed air as power to form a high-speed jet beam to spray materials (copper ore sand, quartz sand, carborundum, iron sand and Hainan sand) onto the surface of the workpiece to be treated at high speed, so that the appearance or shape of the outer surface of the workpiece surface changes. Due to the impact and cutting effect of the abrasive on the workpiece surface, the surface of the workpiece can obtain a certain degree of cleanliness and different roughness, The mechanical properties of the workpiece surface are improved, so the fatigue resistance of the workpiece is improved, the adhesion between the workpiece and the coating is increased, the durability of the coating is prolonged, and it is also conducive to the leveling and decoration of the coating.
◆ sand blasting application range
1. Workpiece coating, pretreatment and sandblasting before workpiece bonding can remove all dirt such as rust on the surface of workpiece, and establish a very important basic pattern (commonly called rough surface) on the surface of workpiece. Moreover, it can achieve different degrees of roughness by changing abrasives with different particle sizes, such as those of flying abrasives, which greatly improves the binding force of workpiece with coating and plating. Or the adhesive can be bonded more firmly and have better quality.
2. Cleaning and polishing of rough surface of castings and workpieces after heat treatment: sand blasting can clean all dirt (such as oxide scale, oil stain and other residues) on the surface of castings, forgings and workpieces after heat treatment, and polish the surface of workpieces to improve the smoothness of workpieces, so that the workpieces can expose uniform metal color and make the appearance of workpieces more beautiful.
3. Burr cleaning and surface beautification of machined parts: sand blasting can clean the micro burr on the surface of the workpiece, make the surface of the workpiece more flat, eliminate the harm of burr, and improve the grade of the workpiece. And the sand blasting can make a small round corner at the junction of the workpiece surface, making the workpiece more beautiful and more precise.
4. Improve the mechanical performance of parts. After sandblasting, mechanical parts can produce uniform and fine concave and convex surfaces on the surface of parts, so that the lubricating oil can be stored, thus improving the lubrication conditions, reducing noise and improving the service life of machinery.
5. Polishing effect for some special purpose workpieces, sandblasting can achieve different reflection or matte at will. For example, the polishing of stainless steel workpieces and plastics, the polishing of jade, the matte finish of wooden furniture, the pattern pattern on the surface of frosted glass, and the texturing process on the surface of cloth.
◆ sand blasting precautions
1. Wear protective articles before work, and do not work with bare arms. No less than two persons shall work.
2. The air tank, pressure gauge and safety valve shall be calibrated regularly. The dust is discharged from the air tank once every two weeks, and the filter in the sand tank is checked once a month.
3. Check whether the ventilation pipe and the door of the sand blasting machine are sealed. Five minutes before work, the ventilation and dust removal equipment must be started. When the ventilation and dust removal equipment fails, the sand blasting machine is prohibited to work.
4. The compressed air valve shall be opened slowly and the air pressure shall not exceed 0.8MPa.
5. The sand blasting particle size shall adapt to the work requirements, generally between 10 and 20, and the sand shall be kept dry.
6. When the sand blasting machine is working, irrelevant personnel are prohibited from approaching. When cleaning and adjusting the operating parts, stop the machine.
7. Do not use compressed air to blow dust or make jokes.
8. After the work is completed, the ventilation and dust removal equipment shall continue to operate for five minutes and then shut down to discharge the indoor dust and keep the site clean.
9. In case of personal and equipment accidents, keep the site and report to relevant departments.
◆ sand blasting process flow
Pre treatment stage of sand blasting process: the pre-treatment stage of sand blasting process refers to the treatment of the workpiece surface before the workpiece is sprayed and sprayed with protective layer.
The quality of sand blasting pretreatment affects the adhesion, appearance, moisture resistance and corrosion resistance of the coating. If the pretreatment is not done well, the corrosion will continue to spread under the coating, causing the coating to fall off in pieces. After careful cleaning of the surface and generally simple cleaning of the workpiece, the coating life can be 4-5 times different by using the exposure method. There are many methods for surface cleaning, but the most common accepted methods are solvent cleaning, pickling, manual tools and power tools.
◆ sand blasting process stage
The sandblasting process uses compressed air as power to form a high-speed jet beam and spray the sprayed material to the surface of the workpiece to be treated at high speed, so that the appearance of the outer surface of the workpiece changes. Due to the impact and cutting effect of the abrasive on the surface of the workpiece, the surface of the workpiece obtains a certain degree of cleanliness and different roughness, and the mechanical performance of the workpiece surface is improved.
◆ cleaning level
I.e. cleanliness, there are two representative international standards: one is “SSPC -” formulated by the United States in 1985; The second is the “SA -” formulated by Sweden in 1976. It is divided into four levels, namely, SA1, SA2, Sa2.5 and SA3. It is a common international standard. Details are as follows:
SA1 – equivalent to sspc-sp7 in the United States. The general simple manual brushing and abrasive cloth polishing methods are adopted, which is the lowest level of cleanliness among the four types. The protection of the coating is only slightly better than that of the untreated workpiece. Technical standard for SA1 treatment: the surface of the workpiece shall be free of oil, grease, residual oxide scale, rust, and residual paint. Grade SA1 is also called manual brushing and cleaning grade. (or cleaning level)
SA2 – equivalent to SSPC-SP6 in the United States. Sand blast cleaning is adopted, which is the lowest level of sand blast treatment, i.e. general requirements. However, the protection of coating is much better than manual brushing cleaning. Technical standard for SA2 treatment: the surface of the workpiece shall be free of oil, dirt, scale, rust, paint, oxide, corrosion and other foreign substances (except for defects), but the defects shall not exceed 33% of the surface per square meter, including slight shadows; A small amount of slight discoloration caused by defects and corrosion; Scale and paint defects. If there are dents on the original surface of the workpiece, slight rust and paint will remain at the bottom of the dents. SA2 grade is also called commodity cleaning grade (or industrial grade).
Sa2.5 level is the level commonly used in industry and can be used as the acceptance technical requirements and standards. Sa2.5 level is also called near white cleaning level (near white level or white level). The technical standard of Sa2.5 level treatment: the same as the first half of SA2 requirements, but the defect is limited to not more than 5% of the surface per square meter, including slight shadows; A small amount of slight discoloration caused by defects and corrosion; Scale and paint defects.
SA3 grade is equivalent to sspc-sp5 grade in the United States. It is the highest treatment grade in the industry, also known as white cleaning grade (or white grade). The technical standard of SA3 treatment: it is the same as Sa2.5, but 5% of shadows, defects and rust have to exist.
◆ classification of sand blasting machine
Sandblasting machine is the most widely used product of abrasive jet. Sandblasting machine is generally divided into dry sandblasting machine and liquid sandblasting machine, and dry sandblasting machine can be divided into suction type and pressure type.
1、 Suction dry sand blasting machine
1. General composition: a complete suction dry sand blasting machine is generally composed of six systems, namely, structural system, medium power system, pipeline system, dust removal system, control system and auxiliary system.
2. Working principle: the suction dry sand blasting machine is powered by compressed air, and through the negative pressure formed in the spray gun by the high-speed movement of the air flow, the abrasive will pass through the sand conveying pipe. It is sucked into the spray gun and ejected through the nozzle, and sprayed onto the surface to be processed to achieve the expected processing purpose. In the suction type dry sand blasting machine, compressed air is both a supply.
2、 Press in dry sand blasting machine
1. General composition: a complete press in dry sand blasting machine working unit is generally composed of four systems, namely, pressure tank, medium power system, pipeline system and control system.
2. Working principle: the press in dry sand blasting machine is powered by compressed air, and the abrasive is passed through the sand valve through the working pressure established in the pressure tank by the compressed air. It is pressed into the sand conveying pipe and ejected through the nozzle to the surface to be processed to achieve the expected processing purpose. In the press in dry sand blasting machine, compressed air is both a supply.
3、 Liquid sandblasting machine
Compared with the dry sand blasting machine, the biggest feature of the liquid sand blasting machine is that it can control the dust pollution in the sand blasting process and improve the working environment of the sand blasting operation.
1. General composition: a complete liquid sandblasting machine is generally composed of five systems, namely, structural system, medium power system, pipeline system, control system and auxiliary system.
2. Working principle: the liquid sandblasting machine uses the grinding liquid pump as the feeding power of the grinding liquid, and the evenly stirred grinding liquid (the mixture of abrasive and water) is sent to the spray gun through the grinding liquid pump. Compressed air, as the accelerating power of grinding liquid, enters the spray gun through the gas pipe. In the spray gun, the compressed air accelerates the grinding liquid entering the spray gun, and then is ejected through the nozzle to the surface to be processed to achieve the expected processing purpose. In the liquid sandblasting machine, the grinding liquid pump is the feeding power and the compressed air is the accelerating power.