Mold costs depe…
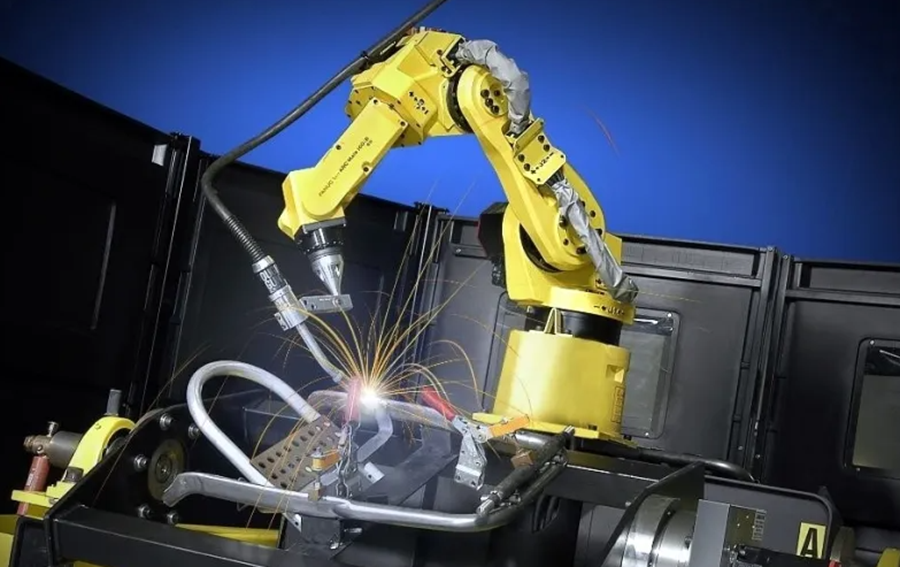
Inspection method and maintenance experience of welding equipment failure
At present, the most widely used welding equipment includes: welding rod arc welding, submerged arc welding, gas tungsten arc welding, plasma arc welding, gas metal arc welding, spot welding, seam welding, projection welding and butt welding.
After a period of use, welding equipment will always fail for various reasons. At this time, the user must refer to the instruction manual of the welding equipment for comparative inspection and maintenance, that is, find and judge the cause according to the fault phenomenon. When the fault location is determined, it shall be repaired and replaced to solve the fault, so that the welding equipment can be put into use as soon as possible, and reduce the economic loss caused by the equipment fault.
1、 Maintenance of welding equipment
1. Ask before moving
For faulty welding equipment, when the truth is unknown, do not rush to start, but first understand the performance of the equipment and ask the operator about the process and phenomenon of the failure. For unfamiliar and complicated welding equipment, it is also necessary to be familiar with the circuit principle and structural characteristics of the equipment and comply with the corresponding regulations. Before disassembly, be fully familiar with the function, location, connection mode of each component and its relationship with other surrounding components. In the absence of wiring diagram and assembly drawing of welding equipment, it is necessary to draw a sketch while disassembling, mark at the same time, and mark the disassembled objects for safety.
2. From outside to inside
Generally, first check whether there are obvious signs of injury on the outside of the welding equipment, whether there are defects in the parts of the electric welding machine, and understand its maintenance history, service life, observe the environment of the use site and welding process, and then check the electric welding machine. The surrounding fault factors, such as wiring, grounding, power distribution capacity and welding process used, shall be eliminated before disassembly. Disassembly can only be carried out after it is determined that it is an internal fault of the welding machine. Otherwise, blind disassembly may make the welding equipment worse and worse, such as shielded metal arc welding, submerged arc welding, tungsten gas shielded arc welding, plasma arc welding and MIG welding.
3. Power before power
Check whether the mechanical components and parts, lubrication, air circuit, water circuit and oil circuit system of the welding equipment have problems. Only after confirming that these systems have no faults can the electrical inspection be carried out. When checking the circuit fault, use detection instruments and meters to find the fault location. After confirming that there is no bad contact fault, check the operation relationship between the line and the machine in a targeted way to avoid misjudgment, such as spot welding, seam welding, projection welding, butt welding and other equipment.
4. Static before dynamic
When the standby is not powered on, judge whether the welding equipment button, contactor, thermal breaker components and fuse are good or bad, so as to determine the fault. Power on test, listen to its sound, measure parameters, judge faults, and finally carry out maintenance. If the article describes the inspection methods and maintenance experience of welding equipment failures When the input phase of the electric welding machine is out of phase, when the three-phase voltage value cannot be measured for discrimination, the sound should be heard and the voltage at each relative location should be measured separately to determine which
One phase defect.
5. Clean before repair
For heavily stained welding equipment, first clean its buttons, wiring points and contact points, and check whether the external control keys are out of order. Many faults are caused by dirt and conductive dust, and they are usually eliminated after cleaning. Especially in the construction site and other places where the environment is relatively harsh.
6. Primary before secondary
Partial failures often account for a high proportion of the total welding equipment failures, so it is often possible to get twice the result with half the effort to repair the power input first. Then check other auxiliary parts of the welding equipment, such as walking, wire feeding and other parts, according to the method of “from outside to inside”, “from engine to electricity”, and “from static to dynamic”.
7. General before special
The failures caused by the quality of components, electrical components, assembly parts or other equipment failures generally account for about 50% of the common failures. The special faults of welding equipment are mostly soft faults, which should be measured and maintained by experience and instruments. If the on-site fault cannot be determined at the moment, you can also consult the technical personnel of the product manufacturer according to the contact information in the product manual. Some internal procedures of such equipment as spot welding, seam welding, projection welding and butt welding should not be adjusted or changed easily without knowing or understanding them, otherwise it will cause more trouble.
8. Control after periphery
It is urgent to replace the damaged electrical components and electrical components. When confirming that the peripheral circuit is normal, it is necessary to consider replacing the damaged electrical components or checking the printed circuit board.
9. DC before AC
When printing the circuit board, you must first check whether there are abnormal heating parts or scorching marks on the printed circuit board and components. Pay attention to the anti-static of the integrated circuit module, and then check the static working point of the input signal and DC circuit, and check the dynamic working point and output signal of the AC circuit for faults, and try to eliminate them.
10. Resolve the fault before debugging
For welding equipment with both commissioning and fault, the fault must be eliminated before commissioning. The commissioning must be carried out on the premise that the electrical circuit is completely free of faults and the wiring is correct (including the grounding wire). If possible, the welding equipment must be tested for insulation resistance before commissioning or welding test.
2、 Inspection method and operation steps
1. Visual inspection
Intuitive method is a method to check and judge faults by looking, smelling, listening and other means according to the external performance of electrical component faults.
(1) Maintenance and inspection steps
① Investigation: ask the operator and the personnel on the scene when the fault occurs, including the external performance of the fault, the general location and the environmental conditions when the fault occurs. If there is any abnormal operation, open flame, heat source, etc., close to electrical components, corrosive gas invasion, water leakage, repair and repair contents, etc.
② Preliminary inspection: according to the investigation, check whether the external parts of relevant electrical components are damaged, whether the wiring is broken or loose, whether the insulation is burnt, whether the fuse indicator of the spiral fuse is out of the beam, whether the electrical components have water and oil dirt, and whether the switch position is correct.
③ Test welding: after preliminary inspection, it is confirmed that there is no possibility to further expand the fault and cause personal and equipment accidents, it can be energized. After it is stable and there is no abnormal condition, further welding test inspection can be carried out. During normal operation of the welding machine, attention should be paid to whether there is serious diving, abnormal smell, abnormal sound, etc. Once found, stop immediately and cut off the power supply. Pay attention to check whether the temperature rise of electrical components and the action procedure of electrical components meet the requirements of the schematic diagram of welding equipment, so as to find the fault location.
(2) Maintenance and inspection methods
① Observe the welding equipment: the contacts of electrical components will produce sparks when they are closed, disconnected or the wire ends are loose, so you can check the failure of electrical components according to the presence and size of sparks.
For example, if sparks or heat are found between a normally solid wire and a screw, the wire head is loose or in poor contact. When the contacts of electrical components and parts are closed and disconnected, there is a fire jump phenomenon, indicating that the circuit is open, and no fire jump indicates that the circuit is not open.
When two phases of the main contact of the contactor controlling the motor have sparks and one phase has no sparks, it indicates that the non sparking phase has poor contact or the circuit is open; The sparks of two phases in three phases are larger than normal, and the sparks of the other phase are smaller than normal, so it can be preliminarily judged that the motor is short circuited or grounded between phases; Three phase sparks are larger than normal, which may be caused by motor overload or mechanical part seizure. In the control circuit, after the circuit is powered on, check the panel indicator light of the welding equipment or check the output signal, and identify the possible fault causes.
After it is normal, press the start button once. If there is a slight spark when the normally open contact of the button is disconnected, it indicates the circuit path. The fault is in the mechanical part of the contactor; If there is no spark between the contacts, it means open circuit.
② Action procedure of welding equipment: the electrical action procedure shall meet the requirements of the welding equipment specification and drawings. If the electrical components on a circuit act too early, too late or do not act, it means that the circuit or electrical components are faulty.
In addition, it can also analyze and judge faults according to the sound, temperature, pressure and smell of electrical components. By using the intuitive method, not only simple faults can be determined, but also more complex faults can be reduced to a smaller range.
2. Voltage measurement method
The voltage measurement method is to measure the voltage and current values and compare them with the normal values according to the power supply mode of electrical components and the working performance of the control circuit board. Specifically, it can be divided into block measurement method, subsection measurement method and spot measurement method to determine the location and cause of the fault.
3. Resistance measurement
The resistance measurement method can be divided into block measurement and subsection measurement. These two methods are applicable to welding equipment with large distribution distance of switches and electrical components (printed circuit board) inside the welding equipment.
4. Comparison, replacement of components, gradual open circuit (or access) method
(1) The comparison method compares the test data with the drawing data and the normal parameters recorded at ordinary times to judge the fault. For electrical components without data or normal records, refer to relevant manuals or product manuals, or compare with intact electrical components of the same model.
When the electrical components and elements in the circuit belong to the same purpose or multiple elements jointly control the same equipment, the action and data of other similar or the same power supply components can be used to judge the fault.
(2) In order to ensure the utilization rate of welding equipment, when the failure cause of some circuits is difficult to determine or the inspection time is too long, use the same component experiment with good performance that can be converted on the same welding equipment to verify whether the failure is caused by the electrical appliance in the components.
When using the conversion element method for inspection, it should be noted that when the original electrical components are removed, they should be carefully checked for damage. Only when it is certain that the electrical components are damaged due to their own factors can new electrical components be replaced, which can prevent the new components from being damaged again.
(3) When multiple branches are connected in parallel in the welding equipment of the stepwise open circuit (or access) method and the circuit with complex control is short circuited or grounded, there are generally obvious external manifestations, such as smoke, burning marks, etc. In case of short circuit and grounding inside the electric welding machine or the circuit with shield, it is not easy to find other external phenomena except for the fuse fusing, which can be checked with the method of gradual open circuit (or access).
① Step by step open circuit method: In case of short circuit or ground fault that is difficult to check, replace the fuse melt again, disconnect multiple branch circuits, one circuit from the circuit step by step or emphatically, and then conduct power on test. If the fuse is repeatedly fused, the fault is on the circuit that has just been disconnected.
Then the branch is divided into several sections and connected to the circuit section by section. When the fuse is connected to a certain section of circuit, it blows again, and the fault lies in this section of circuit and some electrical components. This method is simple, but it is easy to completely burn the electrical components and parts that are not seriously damaged.
② Step by step access method: In case of short circuit or grounding fault in the circuit, replace a new fuse and gradually or emphatically connect each branch to the power supply step by step, and retest. When receiving a certain section, the fuse is blown again, and the fault lies in the circuit just connected and its package. This article describes the inspection method and maintenance experience of welding equipment fault On the electrical components included.
5. Forced closure
When troubleshooting electrical components, they were not found after visual inspection
When there is no proper instrument to measure at the fault point, an insulating rod can be used to forcibly press the relay components, contactors, electromagnets, etc. with an external force to close their normally open contacts, and then observe various phenomena in the electrical components or mechanical parts, such as the motor never rotates, and the corresponding parts of the equipment never move to normal operation.
6. Direct short circuit method
The failures of equipment circuits or electrical components can be roughly classified into seven categories: short circuit, overload, open circuit, grounding, wiring error, electromagnetic and mechanical failures of electrical components, aging of components, etc. The most common faults are open circuit faults, including open circuit, virtual connection, looseness of wires, poor contact of contacts, virtual soldering, false soldering and fuse fusing.
In addition to the resistance method and voltage method, there is a simpler and more reliable way to check such faults, namely the short circuit method. That is, use a well insulated wire to short circuit the suspected open circuit part. If the short circuit is connected to a place, the circuit will work normally, indicating that the place is open circuit. The specific operations can be divided into local short circuit connection and long short connection.
The continuously burnt components shall be replaced after the reason is known; The voltage drop of the conductor shall be considered during voltage measurement; Without violating the principle of equipment performance and the role of electrical components, the repaired welding equipment should be aerated and watered before the initial test energization. The parts that should be oiled should also be oiled, and the surrounding obstacles should be removed. Do not leave the power switch stop button when energized. During the insurance period, use the same amount of current or slightly less than the rated value; Attention must also be paid to the gear selection of measuring instruments.
The above inspection methods shall be applied flexibly according to the situation, but the safety operation rules must be observed to prevent personal and equipment injury accidents during equipment maintenance, and two persons shall operate and monitor as much as possible.
The inspection, maintenance and troubleshooting of welding equipment shall be recorded according to relevant requirements. It is convenient for the accumulation of experience in inspection, daily maintenance and troubleshooting after the occurrence of similar faults in the future, and also serves as the basis for the performance file of qualified suppliers’ products and the selection of products and production units when updating and adding in the future.