Mold costs depe…
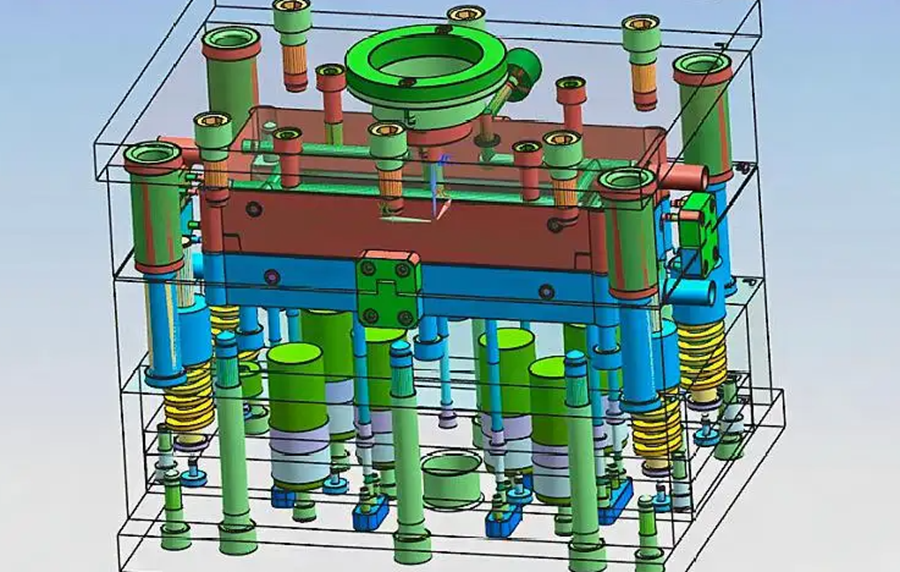
Important Process Conditions of Injection Molding in Plastic Mold Design
Injection molding is an engineering technology, which involves transforming plastics into useful products that can maintain their original properties. The important process conditions of injection molding are the temperature, pressure and corresponding action time that affect the plasticizing flow and cooling.
1、 Temperature control
1. Barrel temperature: the temperature to be controlled during the injection molding process includes the barrel temperature, nozzle temperature and mold temperature. The first two temperatures mainly affect the plasticization and flow of plastics, while the second temperature mainly affects the flow and cooling of plastics. Each kind of plastic has different flow temperature. The flow temperature and decomposition temperature of the same kind of plastic are different due to different sources or brands. This is due to different average molecular weight and molecular weight distribution. The plasticizing process of plastic in different types of injection machines is also different, so the selection of barrel temperature is also different.
2. Nozzle temperature: The nozzle temperature is usually slightly lower than the maximum temperature of the barrel, which is to prevent the “salivation” of molten materials that may occur in the straight through nozzle. The nozzle temperature shall not be too low, otherwise, the nozzle will be blocked due to the early setting of the melted material, or the performance of the product will be affected due to the early setting material being injected into the mold cavity
3. Mold temperature: Mold temperature has a great impact on the internal performance and apparent quality of products. The mold temperature depends on the crystallinity of the plastic, the size and structure of the product, performance requirements, and other process conditions (melt temperature, injection speed, injection pressure, molding cycle, etc.).
2、 Pressure control: The pressure in the injection molding process includes plasticizing pressure and injection pressure, and directly affects the plasticization of plastics and the quality of products.
1. Plasticizing pressure: (back pressure) When the screw injection machine is used, the pressure on the molten material at the top of the screw when the screw rotates backward is called plasticizing pressure, also called back pressure. The pressure can be adjusted through the relief valve in the hydraulic system. In injection, the plasticizing pressure is constant with the screw speed, so increasing the plasticizing pressure will increase the melt temperature, but will reduce the plasticizing speed. In addition, increasing the plasticizing pressure can often make the temperature of the melt uniform, the color mixture uniform and the gas in the melt discharged. In general operation, the plasticizing pressure shall be determined as low as possible on the premise of ensuring good product quality. The specific value varies with the type of plastic used, but it rarely exceeds 20kg/cm2.
2. Injection pressure: In current production, the injection pressure of almost all injection machines is based on the pressure applied on the plastic by the top of the plunger or screw (converted from the oil pressure). The role of injection pressure in injection molding is to overcome the flow resistance of plastic from the barrel to the cavity, give the molten material the speed of mold filling and compact the molten material.
3、 Molding cycle
The time required to complete an injection molding process is called the molding cycle, also known as the molding cycle. It actually includes the following parts:
Molding cycle: The molding cycle directly affects labor productivity and equipment utilization. Therefore, in the production process, the relevant time in the molding cycle should be shortened as much as possible on the premise of ensuring the quality. In the whole molding cycle, injection time and cooling time are the most important, which have a decisive impact on the quality of products. The filling time in the injection time is directly inversely proportional to the filling rate, and the filling time in production is generally about 3-5 seconds.
The pressure holding time in the injection time is the pressure time for the plastic in the mold cavity, which accounts for a large proportion in the entire injection time, generally about 20-120 seconds (up to 5-10 minutes for extra thick parts). Before the melt at the gate is frozen, the holding time has an impact on the dimensional accuracy of the product. If it is later, it has no impact. The holding time also has the most favorable value. It is known that it depends on the material temperature, mold temperature, and the size of the sprue and gate. If the dimensions of the sprue and gate and the process conditions are normal, the pressure value with the lowest fluctuation range of the shrinkage of the product is usually taken as the criterion. The cooling time mainly depends on the thickness of the product, the thermal and crystalline properties of the plastic, and the mold temperature. The end point of cooling time shall be based on the principle of ensuring that the products will not be changed during demoulding. The cooling time is generally about 30~120 seconds. It is unnecessary to have too long cooling time, which will not only reduce production efficiency, but also cause difficulty in demoulding for complex parts, and even produce demoulding stress when forced demoulding. Other times in the molding cycle are related to whether the production process is continuous and automatic, and the degree of continuity and automation.
General injection molding machines can be adjusted according to the following procedures:
Adjust the barrel temperature to the middle of the range according to the temperature range provided by the raw material supplier, and adjust the mold temperature.
Estimate the required injection volume, and adjust the injection molding machine to two-thirds of the estimated maximum injection volume. Adjust the stroke of the backstop (rubber extraction). Estimate and adjust the secondary injection time, and adjust the secondary injection pressure to zero.
Adjust the primary injection pressure to half (50%) of the limit of the injection molding machine; Set the injection speed to the highest. Estimate and adjust the cooling time required. Adjust the back pressure to 3.5 bar. Remove the degraded resin in the barrel. Adopt semi-automatic injection molding mode; Start the injection molding procedure and observe the action of the screw.
It is necessary to properly adjust the injection speed and pressure. To shorten the filling time, the injection pressure can be increased. As mentioned above, since there will be a process before full filling, the final filling pressure can be adjusted to 100% of the primary injection pressure. Finally, the pressure should be adjusted high enough so that the maximum speed that can be reached is not limited by the set pressure. If there is overflow, the speed can be reduced.