Mold costs depe…
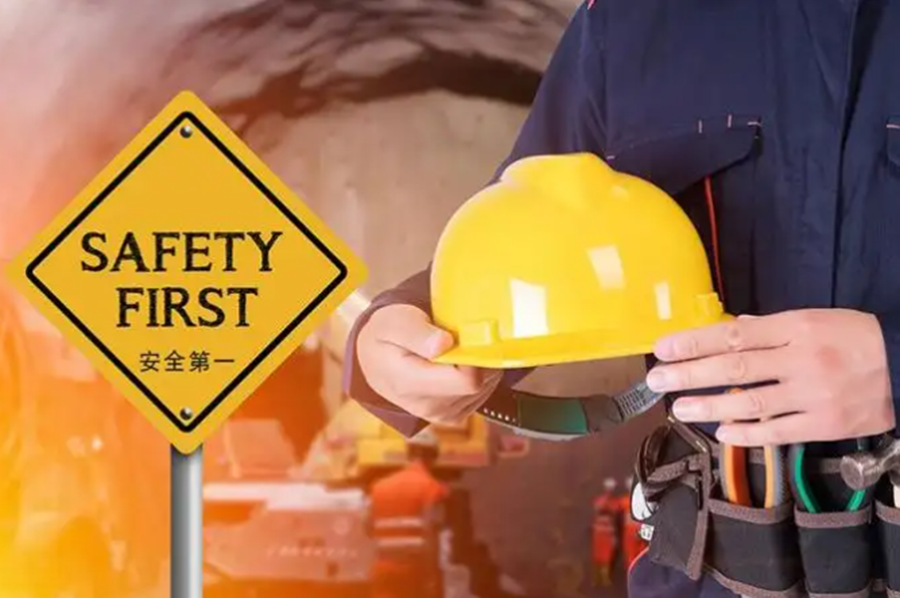
How to protect yourself during machining?
The setting principles of safety protection devices are as follows:
First, based on the plane on which the operator stands, all moving parts with a height of less than 2m shall be protected.
Second, based on the plane on which the operator stands, if the height is more than 2m, there are material transmission devices, belt transmission devices and the lower part of the construction machinery, protection should be provided.
Third, protection shall be provided at the operation position 2m above the falling height datum plane.
Fourth, in order to avoid crushing injury, the distance between linear moving parts or between linear moving parts and static parts shall meet the requirements of safe distance.
Fifth, if the travel distance of moving parts is required, reliable limit devices shall be set to prevent injuries caused by over travel movement.
Sixth, load limiting devices shall be provided for those parts that may be damaged due to overload.
Seventh, the moving parts with inertia must be equipped with reliable buffer devices to prevent injury accidents caused by inertia.
Eighth, effective measures must be taken to tighten the parts that may be loosened during movement to prevent loosening due to startup, braking, impact and vibration.
Ninth, each machine shall be equipped with an emergency stop device to avoid existing or imminent dangers. The identification of the emergency stop device must be clear and easy to identify, and the device can be quickly accessed, so that the dangerous process can be stopped immediately without additional risks.
01
Protective device
Generally, shells, covers, screens, doors, covers, fences, closed devices, etc. are used as object barriers to isolate people from hazards. For example, the protective cover made of metal casting or metal plate welding is generally used for the protection of gear transmission or transmission devices with small transmission distance; The metal frame and the metal mesh are made into a protective mesh, which is often used for the protection of belt drives; Fence type protection is applicable to places with large protection scope or as on-site protection for temporary operation of mobile machinery.
1. Function of protective device
(1) Prevent any part of the human body from entering the dangerous area of the machine and touching various moving parts;
(2) Prevent the impact of flying objects, accidental jet of high-pressure liquid, or prevent human body from burning and corrosion;
(3) It can accept the parts that may be thrown, dropped or fired by machinery and the broken fragments.
In the case of special requirements, the protective device shall also have special functions of blocking, isolating, sealing, absorbing or shielding electricity, high temperature, fire, explosives, vibration, radiation, dust, smoke, noise, etc.
2. Type of protective device
The protective device has a separate protective device (only when the protective device is closed can it play a protective role); And the protective device used in combination with the interlocking device (no matter in any state, the protective device can play a protective role). It can be divided into fixed type and movable type according to the use mode.
(1) Fixed guards. It is a protective device that is kept closed or fixed in the required position, and can not be opened or removed without tools. The common types are closed type, fixed distance type and fixed distance type.
① Closed type: the hazardous area is completely closed, and people cannot enter the hazardous area from anywhere.
② Fixed distance type and fixed distance type: the hazard area is not completely enclosed, and the physical size and safe distance from the hazard area prevent or reduce the opportunity for people to enter the hazard area.
(2) Movable guards. It is a protective device that can be opened without tools by connecting it to the frame of the machine or its adjacent fixed elements through mechanical methods (such as iron chains, slideways, etc.). Adjustable and interlocking protective devices are common.
① Adjustable guards. The whole device is adjustable or some part of the device is adjustable, and the adjusting element remains fixed during a specific operation.
② Interlocking guards. The opening and closing state of the protective device is directly interlocked with the dangerous state of protection. As long as the protective device is not closed, the dangerous machine function “inhibited” by the protective device cannot be executed; Dangerous machine functions that are “inhibited” by the guards are only possible when the guards are closed. In the process of dangerous machine function, as long as the protective device is opened, the stop command will be given.
3. Safety technical requirements for protective devices
(1) The fixed protective device shall be fixed at the required place by means of permanent fixation (by welding, etc.) or by means of fasteners (screws, bolts, nuts, etc.). It cannot be moved or opened without tools.
(2) The opening for feeding and discharging shall be as small as possible, and shall meet the requirements of safe distance, so that people cannot contact the danger from the opening.
(3) When the movable protective device or the movable body of the protective device is opened, it shall be connected to the protective machinery with hinges or guide chains as far as possible to prevent the removed protective device or movable body from being lost or difficult to recover.
(4) When the movable protective device loses its safety function, the dangerous machine function “inhibited” by it cannot be executed or stopped; Failure of interlocks shall not result in accidental actuation.
(5) The protective device shall be the only access to the hazardous area.
(6) The protective device shall be able to effectively prevent the danger of flying objects.
02
Safety devices
Safety devices limit or prevent certain dangers of the machine, or limit movement speed, pressure and other dangerous factors through their own structural functions. Common safety devices include interlocking device, two handed operation device, automatic stop device, limit device, etc.
Technical features of safety devices
(1) The reliability of parts of safety device shall be the basis of its safety function, and the safety device will not lose its main safety function due to the failure of parts within a certain service life.
(2) The safety device shall be able to stop the dangerous process when the dangerous event is about to happen.
(3) The safety device has the function of restart, that is, when the safety device stops for the first time, the machine can start to work only after it is restarted again.
(4) Photoelectric and inductive safety devices shall have self checking function. When the safety device fails, the dangerous machine functions shall not be executed or stopped, and the alarm shall be triggered.
(5) The safety device must operate together with the control system and be integrated with it. The performance level of the safety device shall adapt to it.
(6) The design of components or systems of safety devices shall adopt “directed failure mode”, considering the doubling or redundancy of key components, and automatic monitoring shall be adopted when necessary.
03
Type of safety device
(1) Interlocks. This is a device to prevent machine parts from operating under specific conditions (generally as long as the protective device is not closed). It can be mechanical, electric, hydraulic or pneumatic.
(2) Actuating device. This is an additional manual control device. When the machine is started, only by operating this actuating device can the machine perform the intended functions.
(3) Stop the operating device. This is a manual control device. The machine can be started and kept running only when the hand acts on the manipulator; When the manipulator is released by hand, the operating device can automatically return to the stop position.
(4) Two handed control device. This is a stop control device for simultaneous action of two manual manipulators. Only when both hands act on the manipulator at the same time can the machine or part of the machine be started and kept running.
(5) Automatic stop device. When a person or a part of the human body exceeds the safety limit, the device will stop the machine or its parts (or ensure other safety conditions). The automatic shutdown device can be mechanically driven, such as trigger wire, retractable probe, pressure sensitive device, etc; It can also be non mechanically driven, such as photoelectric device, capacitor device, ultrasonic device, etc.
(6) Mechanical suppression device. This is a mechanical obstacle (such as wedge, strut, stay bar, stop bar, etc.) device. The device is supported in the mechanism by its own strength to prevent some dangerous movement.
(7) Limiting device. This is a device to prevent the machine or machine elements from exceeding the design limit (such as space limit, speed limit, pressure limit, etc.).
(8) A limited motion control device, also known as a travel limiting device. Only machine parts are allowed to operate within a limited range of travel. The machine parts cannot move further until the control device has the next separation action.
(9) Exclude the device. A device that mechanically removes the human body part in danger from the danger zone during the dangerous journey of the machine.
Who invented the super tire? It won’t be punctured when it passes through the nail
04
Selection of safety protection devices
The type of safety protection device shall be selected in consideration of the mechanical hazards and other non mechanical hazards involved, and shall be determined according to the nature of moving parts and the needs of personnel entering the hazardous area. The safety protection of a specific machine shall be selected according to the risk assessment results of the machine.
1. Where the operator does not need to enter the danger area during normal operation of the machine
Where the operator does not need to enter the hazardous area, priority should be given to the selection of fixed protective devices, including feeding and reclaiming devices, auxiliary workbenches, fences of appropriate height and channel protective devices.
2. Places where the machine needs to enter the danger zone during normal operation
When the operator needs to enter the dangerous area for many times and it will be inconvenient to open the fixed protective device frequently, the interlocking device, automatic shutdown device, adjustable protective device, automatic shutdown protective device, two handed control device, controllable protective device, etc. can be considered.
3. For places that need to enter the hazardous area during non operation and other operations
For the setting, teaching, process conversion, fault finding, cleaning or maintenance of the machine, the protective device must be removed or removed, or the function of the safety device is inhibited. Manual control mode, stop stop control device or two hand control device, inching limited movement control device, etc. can be used.
In some cases, several safety protection devices may be used together.