Mold costs depe…
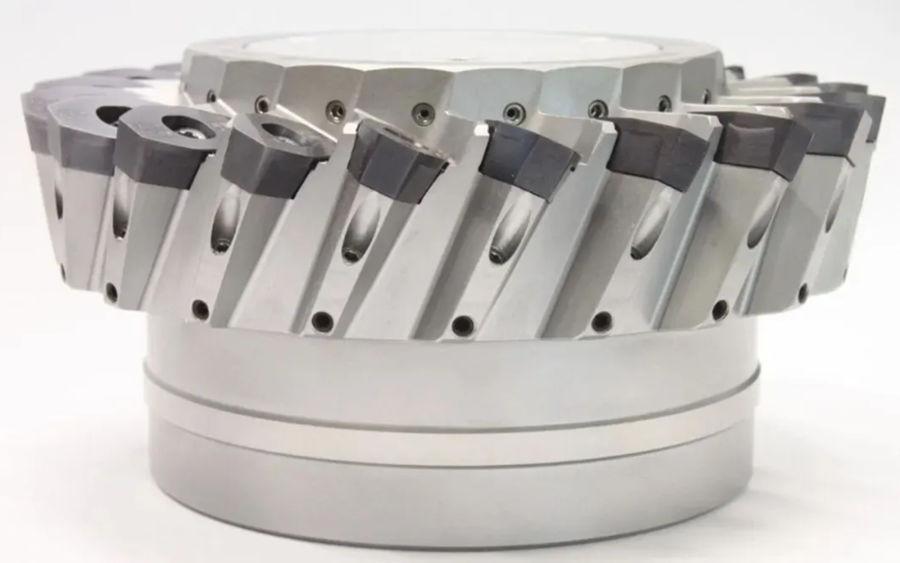
High speed cutting self rolling cutter
In the development process of high-speed cutting technology, high-speed cutting machine tools, high-speed tool systems and high-speed cutting technology are the three main technologies, and tool technology plays a very important role. With the increase of cutting speed, higher requirements are put forward for cutting tool materials, tool geometric parameters, tool body structure and cutting process parameters, which are different from those under the traditional cutting speed. Because the cutting heat and tool wear produced in high-speed cutting are much higher than those at ordinary speeds, the high temperature resistance and wear resistance of tool materials are an important obstacle to the development of high-speed cutting technology. The requirements for tool materials mainly include the following aspects: ① high hardness, high strength and wear resistance; ② Good toughness and impact resistance; ③ High thermal hardness and chemical stability; ④ Strong thermal shock resistance, etc.
Although the current tool materials have developed from early high-speed steel and cemented carbide to ceramics, cubic boron nitride (CBN) and diamond, and the tool coating technology and sintering lamination technology have been developed and applied, it is difficult to meet the above requirements at the same time, and the prices of CBN, diamond and other tools are also high. It can be seen that blindly pursuing the development and progress of tool materials is not the best choice. Starting from the structure of the tool, the self rolling cutter ingeniously adds a movement unit to the tool, improves the working state of the tool, and greatly improves the high-temperature and wear resistance of the tool material.
1. Basic principle of self rolling cutter
The self rolling cutter adopts a circular blade, which is driven to rotate around its axis by the relative movement between the workpiece and the cutter during the cutting process. Taking turning as an example, one way to install the blade is to use the end face of the round blade as the rake face and the circumference as the rake face, which is called Type I self hobbing tool (the former has a positive edge inclination, while the latter has a negative edge inclination); The other is to use the circumference of the round blade as the rake face and the end face as the back face, which is called Type II self hobbing cutter.
Since a cutting movement unit is added to the blade of the self rolling cutter, it not only has the characteristics of bevel cutting, but also has the rolling effect on the workpiece surface from the rib of the back cutter surface, so the cutting feature of the self rolling cutter is the combination of “rolling” and “cutting”. Many of its cutting concepts are different from ordinary tools and must be modified.
2. Two important concepts of self rolling cutter
(1) Edge inclination
The edge inclination of self – hobbing cutter is an important parameter to determine the cutting performance, and it is also a prerequisite to add a motion unit to the cutting motion. The rake angle has a direct influence on the rake angle, back angle, chip flow angle and even the cutting speed.
The inclination of the axis of type I tool in the XZ plane makes the blade have an angle λ, We call it the mounting blade inclination. If the point with zero principal deflection angle on the arc cutting edge is named as the tool tip, install the edge inclination λ That is, the blade inclination of the tool tip. For type II cutting tools, although the installation edge inclination and the tool tip are not intuitive, they can also be obtained through simple derivation.
In fact, the above understanding of the blade inclination is only in the geometric sense, not comprehensive. As the blade inclination is not only a geometric parameter between the tangent line of the blade and the base surface, but also a ‘motion parameter’ that affects the relative speed of the workpiece along the tangent and normal directions of the blade. For hobbing tools, when the cutting process is unstable or the resistance of the blade rotation changes, or even when the blade rotation is driven by external power (this is a driven hobbing tool), the rotation of the blade is different from that driven by the workpiece under ideal conditions, and the true edge inclination of each point on the cutting edge will change. Therefore, some scholars also put forward the concepts of working edge inclination and equivalent edge inclination, which will not be discussed here.
(2) Cutting speed
The concept of cutting speed of self – hobbing cutter is different from that of common cutter. Taking turning with type I tool as an example, V (linear speed of workpiece surface) is called nominal cutting speed, which is an important parameter compared with ordinary tools and the speed of computer bed; Vr is called relative cutting speed, which is the cutting speed component of the hobbing tool equivalent to the ordinary tool, and is the friction speed on the tool flank of the self hobbing tool. When the friction resistance of blade rotation is not considered, Vr = Vcos can be obtained λ。 The above Vr is actually only the relative cutting speed at the tool tip.
Some scholars also put forward the concept of effective cutting speed. They believe that the tool speed Vt and the relative speed Vr are both generated by the nominal cutting speed V. Therefore, V should be divided into two parts. One part is used to generate Vt, that is, the projection of Vt on V; One part is used to generate Vr, that is, the projection of Vr on V, which is called the effective cutting speed Ve.
The feed speed also has an impact on the speed Vt of the blade, which has been discussed in many literatures.
The above two important concepts of self rolling cutter are briefly introduced. It can be seen that there are still differences and different opinions. The purpose of this paper is to make a thorough theoretical study, deepen the understanding of self rolling cutting tools and guide practice.
3. Overall evaluation of self rolling cutter
Both theoretical and experimental studies show that the self rolling cutter has the following advantages:
(1) High tool durability, suitable for high-speed cutting. The literature shows that I type self rolling turning tool with high speed steel blade can cut 50 steel normally at a nominal speed of 150 m/min, which is impossible for ordinary tools; In the test of milling LY12 with Type I self hobbing end milling cutter, the nominal speed is about 1000m/min. The literature shows that the wear of the rear face of the CBN type I self hobbing turning tool is only 0.01 mm after 60 minutes of machining the quenched 55 steel at a nominal cutting speed of 190 m/min.
(2) Good processing quality. The surface roughness of HT200, quenched steel and silicon aluminum alloy machined with self rolling cutter is lower than that of ordinary cutter. For example, silicon aluminum alloy is processed with I-type self rolling end milling cutter. The cutter material is W18Cr4V, the nominal speed is V=1178.1m/min, and the cutting depth is α P=0.1 ~ 0.2mm, feed per tooth α F=0.05mm/z, surface roughness reaches Ra0.1 ~ 0.2 μ m。
(3) High productivity and good economic benefits. The experimental research shows that the self rolling cutting tool can achieve the same machining quality with ordinary tool materials (high-speed steel, hard alloy, etc.) according to higher cutting speed and larger feed rate.
The self rolling cutter also has some obvious shortcomings, mainly including:
(1) The structure is complex and requires high manufacturing accuracy, especially for the rotating part of the tool. If the manufacturing error is large or the adjustment is improper, it is easy to cause vibration and damage the surface quality.
(2) The blade workpiece contact arc is long and the radial force is large, so there is a high requirement for the rigidity of the process system, or only a small cutting depth can be used.
(3) It is not suitable for machining parts with steps on the surface.
4. Conclusion
(1) By adding a movement unit to the blade, the self rolling cutter changes the stress and heat state of the cutter during cutting, so that the common tool material can be used for high-speed cutting;
(2) Many cutting concepts of self – hobbing cutter are different from those of common cutter, so it is necessary to revise them to perfect the theory and guide the rational use of self – hobbing cutter;
(3) Although the self rolling cutter has many advantages, it also has some disadvantages, so we should take advantage of the advantages and avoid the disadvantages when using it.