Mold costs depe…
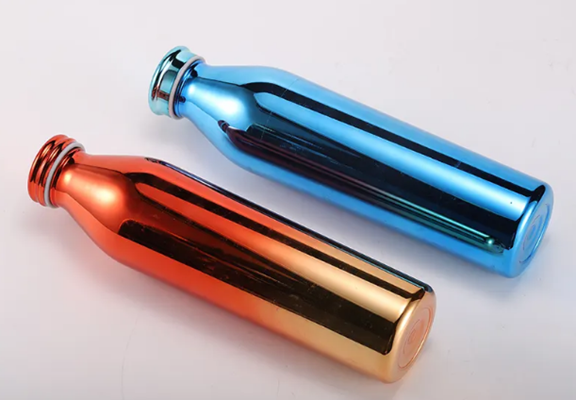
Hand board surface treatment process ①: Electroplating
Electroplating is often mentioned in the production process of hand board. It is a commonly used surface treatment technology in hand board production. Then, what is the role of electroplating technology in hand board manufacturing?
Electroplating is the process of plating a thin layer of other metals or alloys on the metal surface using the principle of electrolysis. The purpose of electroplating is to coat the metal coating on the substrate and change the surface properties or dimensions of the substrate Electroplating can enhance the corrosion resistance of metal (the coating metal mostly adopts corrosion-resistant metal), increase hardness, prevent abrasion, improve conductivity, lubricity, heat resistance and beautiful surface.
Although both plastic and metal hand boards can use electroplating technology, they are still different in electroplating because of their different characteristics. The plastic hand plate has strong adsorption and can be electroplated directly on the surface of the hand plate. If the metal hand plate is electroplated directly, it will be easy to fall. Therefore, the metal hand plate needs to be sprayed with a layer of primer before electroplating, so the effect of electroplating will be very good and the anti-corrosion time will be longer.
According to different coating materials, it has different effects in practical application, such as:
Gold plating: improve conductive contact impedance and enhance signal transmission. (gold is the most stable and expensive.)
Silver plating: improve conductive contact impedance and enhance signal transmission. (silver has the best performance, is easy to oxidize, and is also conductive after oxidation)
Copper plating: used for backing to improve the adhesion and corrosion resistance of electroplating layer. (copper is easy to oxidize. After oxidation, copper green is no longer conductive, so copper plated products must be protected)
Nickel plating: used for priming or appearance to improve corrosion resistance and wear resistance (among which chemical nickel is more wear-resistant than chromium plating in modern technology). (note that many electronic products, such as DIN head and N head, no longer use nickel backing, mainly because nickel is magnetic, which will affect the passive intermodulation in the electrical performance)
Palladium nickel plating: improve conductive contact impedance, enhance signal transmission, and the wear resistance is higher than that of gold.
It is replaced by tin and other lead plating (now replaced by tin fog).