Mold costs depe…
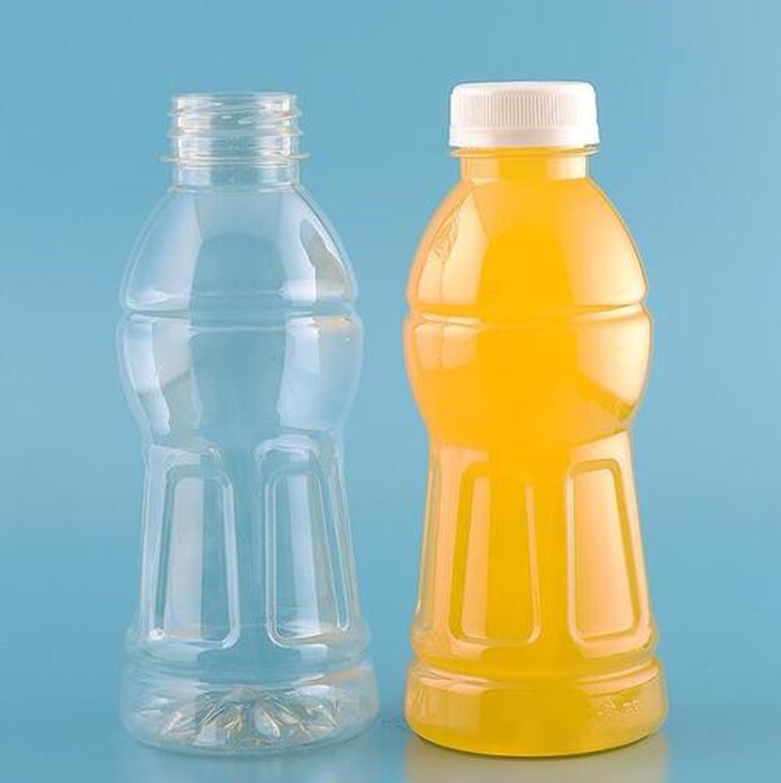
Forming process of PET blow molding bottle
The production of PET blow molding bottles can be divided into injection stretch blow molding (injection stretch blow molding for short) and extrusion stretch blow molding (extrusion stretch blow molding for short) according to the different preforms of parison. The process of injection, drawing and blowing is that the preform with bottom is injected first, and then it is continuously sent to the heating furnace (infrared or electric heating) by the conveyor belt after cooling, and then it is heated to the stretching temperature, and then it is brought into the blowing mold for axial stretching with the help of a stretching rod, and finally it is formed by blowing and blowing.
As the bundled glass beer bottles have repeatedly exploded and injured people, foreign countries have intentionally turned to PET bottle packaging. In addition, PET blow molding bottles are widely used for beverage packaging because of their light weight (1/10 of the same glass bottles), high strength, transparency, non-toxic and other advantages, especially for the packaging of carbonated beverages (such as Coke). Therefore, the market prospect of PET blow molding bottle is broad. In the following, the influence factors of preform preform reheating, stretch blow molding process are discussed.
1. Equipment
At present, most of the two-step blow molding machines used in China are made in Germany, France and other countries, which are more advanced in the world. This kind of equipment has a high degree of automation, large output, low rate of defective products, and easy process control. Each equipment can hold 4-40 molds, with more than 60 molds. The output per hour is about several thousand, and some can reach 20000. This kind of equipment is generally composed of five parts: billet supply system, heating system, main machine, control system and auxiliary machine. The most important part is the main machine, which is fully computer controlled, including the opening and closing of the main machine, the opening and closing of the oven lamp and the adjustment of the molding process.
2. Influencing factors
The influencing factors in the process include: preform and its heating, pre blowing (position, pressure and flow), stretching rod, high-pressure blowing (pressure and position), and mold.
① Preform
Bottle preform, also known as parison, is made of PET granules by injection molding. It requires that the proportion of recycled materials should not exceed 10% and the number of recoveries should not exceed two. Bottle preforms after injection molding or reused after heating must be cooled for more than 48h, and the used bottle preforms cannot be stored for more than 6 months. Bottle preforms with different production dates, especially those with long intervals, cannot be mixed. The main reason is that the model of raw materials used for bottle preforms, the proportion of mixed secondary materials, and the residual stress in the bottle preforms are different. These factors have a significant impact on the bottle blowing molding process, and should be treated according to the actual situation.
② Heating
The preform is heated by the heating furnace, manually set and automatically adjusted. The height of the heating furnace should be about 25 mm and about 19.6 mm from the conveying wheel. The preform runs continuously on the conveying wheel through the whole oven, so that the preform is heated more evenly and can be formed better. The disadvantage of uneven heating caused by static heating and manual rotation of preform before is overcome. However, if the heating furnace is not adjusted properly, the wall thickness of the blown bottle will be unevenly distributed up and down (as above, light and heavy), the bottle mouth will become larger and exceed the standard, the hard neck and other product defects will be caused, and even the torque failure of the mechanical parts will be caused.
The heating temperature of preform is generally set at 85-120 ℃. The colorless preform should be higher and the colored preform should be lower. If the temperature is set too high or too low, it will cause product defects, such as tear, white fog, etc. The temperature of each area can be adjusted according to the molding of the products, and the opening of the oven lamp shall be considered. In addition, the setting of the oven output power also has a great impact on the heating of the preform, which controls the heat output of the entire oven. When the machine is not started for a long time and is started again, the initial output power should be set higher accordingly, and then gradually reduced to the normal state during the normal production process. The output power is generally about 80%, especially when the ambient temperature is below 5 ℃, the effect is more significant.
The bottle blowing production process is also related to the production environment temperature, which is generally at room temperature (about 22 ℃). If the temperature is too high, the products are easy to agglomerate; The temperature is too low, and the product performance is unstable when the machine starts. The specific operation should be adjusted according to the actual situation and experience.
③ Preblowing
The role of pre blowing in the blowing process is to make the preform take shape initially, and at the same time, the longitudinal strength of the preform is increased by longitudinal stretching of the stretching bar. The whole process is that the pre blowing cam pushes the three-way valve to the pre blowing position in the process of bottle blowing, which is completed by the cooperation of the one-way valve. Pre blowing position, pressure and flow can affect the quality of bottles.
(1) Location
If the pre blowing position is advanced, the bottle bottom center point will deflect and become thinner, the foot wall thickness will be uneven and white, the upper weight will be light, the neck will be hard, and even the bottom will penetrate; If the pre blowing position is wrong, defects such as light upper and heavy lower, thickened central point, and dents will appear.
(2) Air flow
The pre blowing flow is controlled by a one-way valve, and it is generally advisable to open it for 3-4 turns. The air flow is large, the bottom is heavy, the center point is thin and partial, the feet are white, and the wall thickness is uneven; The air flow is small, the center point is thickened, and the sectional pieces are overweight.
(3) Pressure
The pre blowing pressure should be 0.8-1MPa. When the pressure is high, it may cause the upper part to be heavy and the lower part to be light, the center point to be skewed, the foot wall thickness to be uneven, and the foot to be white; When the pressure is low, it cannot be fully stretched, the bottom is heavy, and the center point is thick. The molding of the bottle foot and the center point has the greatest impact on the bottle quality, and improper adjustment often leads to bottle bursting (under normal experimental conditions), leakage and other fatal defects.
④ Stretching rod
The stretching rod is a device that stretches the heated preform with the cooperation of pre blowing while pre blowing. It is reset after high-pressure blowing and before exhausting. The stretching rod must be able to move vertically and steadily up and down during the bottle blowing process. The driving pressure is 0.55-0.8MPa, and the gap between the stretching rod and the bottom mold is 2.3-2.5mm, that is, the thickness of the preform is 1/3-1/2. If the gap is too large, the center point of the bottle bottom will shift; The clearance is too small, and the center point becomes thinner.
⑤ High pressure blowing
The function of high-pressure blowing is to make the molten material fully extend and cling to the mold wall to fully shape the bottle.