Mold costs depe…
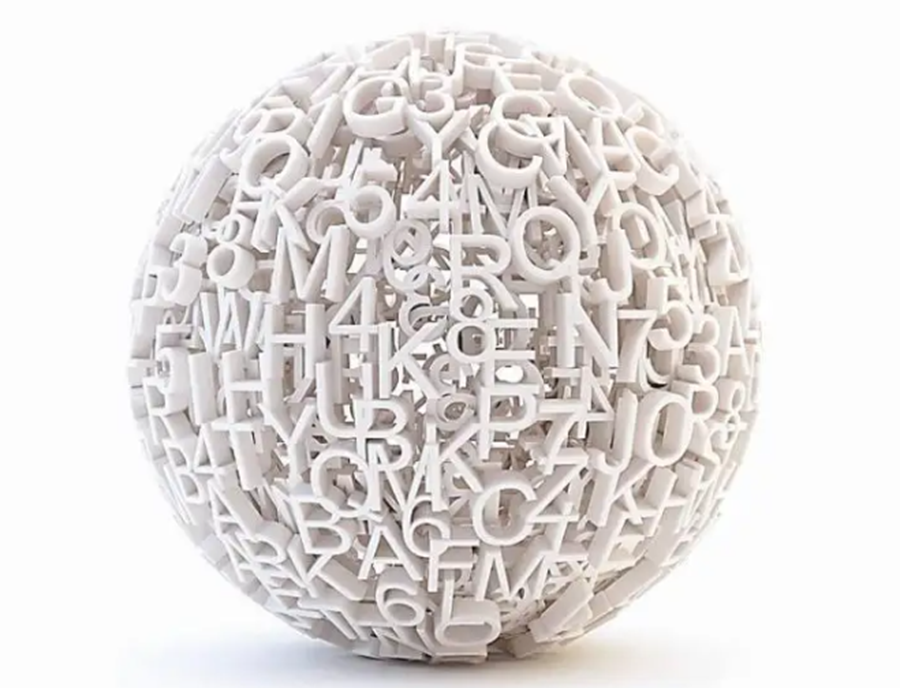
Fillet: when to use, when to lose
Rounded corners are one of those design features that seem to have no middle ground, or at least are not well known. Either the part does not have them and most or all edges are well defined, or the designer of the part decides to adopt the opposite route and each edge and corner is rounded with a certain size of fillet radius.
Fillet is very useful in the design field, especially when the part is to be CNC machined, which will be our main assumption in the following example. This article will reveal that fillets are a bad idea, a good idea, and an absolutely necessary situation (tip: corner fillets), so you can start adjusting your design to make it more cost-effective and easier to manufacture.
Where fillets are not required
Before discussing the use cases of rounded corners, the simplest way is to exclude some places where you do not need them, because too many things are never a good thing.
3D Print Parts
Because 3D printing is an additive process, it is assumed that tools need to move around the part and remove materials, so designers can more freely use complex and unusual geometry without designing the part. Fillets are sometimes used to relieve stress in areas where geometry changes dramatically, but they are rarely needed otherwise. Pockets and internal features on printed materials can be angular or angular, or even have cavities completely surrounded by surrounding materials!
In addition, remember that if you eventually move from 3D printing to another process, such as machining, you must start planning the limitations of the process early to save time and money.
The base
Rounding the bottom edge of a groove, wall, or boss feature can be used to improve the aesthetics of the part or increase the strength of the feature (by reducing stress concentration). However, fillets at these locations require the use of ball end mills, which can make your parts more expensive than square bottom features. This is because programming such geometry usually requires 3D machining operations (dialing in takes longer). In addition, ball end mills are inherently more vulnerable than square end mills and must be processed at a much slower speed.
Another related note is that rounding the bottom edge of the part will require another fixture setup, which will also increase the production price of the part.
Where are fillets useful
The next section will provide some examples where filleting may be convenient, although not required. However, keep in mind that fillets on CNC parts can increase programming and machining time, which can increase costs.
Trim the face edges
When designing parts with decorative surfaces, it is a good method to fillet the edges of these areas, which can make the parts look like their faces are seamlessly blended together, rather than excessive transition.
Edge softening
If parts are often handled, especially when cutting from metal, adding rounded corners can prevent sharp edges from causing damage. It is standard practice for machinists to break all sharp edges by hand, so unless you like perfect rounded edges or your parts have ergonomic features in rounded areas, it is better not to do so to save costs.
Pin/fastener insertion
If the fit is too tight, it may be difficult to engage the locating pin with the press fit hole, or to align the fastener with its internal thread fitting. Typically, a small chamfer (read: chamfer) is added around the edge of the hole to help insert, but fillets can also help insert if needed.
Where rounded corners are absolutely required
The last part discusses three cases that need fillets to enable CNC machining of parts.
Interior edge between vertical walls
To cut by high-speed rotation, all CNC tools are round and axisymmetric, so it is almost impossible to cut a square angle between two vertical walls. In fact, any edge where the intersection angle of two vertical walls is less than 180 ° needs to be filleted. This is the most common DFM feedback. We must give it on VirtualV about CNC parts.
Internal edges between sloping/organic surfaces
Similar to the first case in this section, edges less than 180 ° between angular surfaces or organic surfaces also require fillets. If these edges are not perfectly perpendicular, they will be cut with a ball end mill whose radius is the minimum fillet size that can be retained between surfaces.
Vertical wall+angled/curved/organic surface
In the combination of the first and second cases, when the vertical wall on the part intersects with the inclined, curved or organic surface below, the fillet is required. This may be difficult to explain at first, but if you imagine a square or ball end milling cutter cutting flush along the wall, you can imagine that there is always residual material between the wall and the surface below, unless the surface is completely flat and perpendicular to the tool.
Recommended standards
Now you know the general situation of supporting and opposing the use of fillets. If you are going to produce parts through the rapid machining platform, you need to comply with two main standards.
Minimum fillet size
By default, the minimum milling cutter in our supplier’s inventory is 1/32 inch end milling cutter (square and spherical). This is just below 0.8 mm diameter, which means that the minimum fillet it can create is 0.4 mm.
Fillet size and cutting depth
The length of the end mill is the standard multiple of its diameter, but because the tool vibration and chatter exceed a certain proportion, there is a limit to the length available. Materials also play a role here. It is much easier to cut deep grooves into plastic or CNC aluminum than into harder materials such as steel. This pair of fillets means that they need to be of a certain size, depending on how deep you need to cut to form features that contain fillets.
Key points
Hopefully these tips will help clarify the world of fillets for you. Especially in the case of CNC machining, it is absolutely important to know when and where not to use these functions: it can save you time, increase part functions, and lead to cheaper overall parts. Even if you are not currently designing for machining, it is still a good idea to follow these guidelines in case you decide to do so.