Mold costs depe…
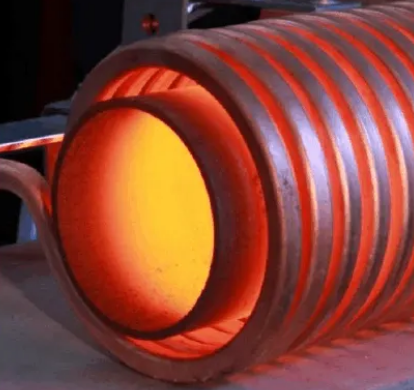
Explanation of terms such as metal and heat treatment
Metal: a material with good thermal conductivity and conductivity, which is opaque and metallic luster, and whose conductivity decreases with the increase of temperature, and is rich in ductility and expansibility. A solid (i.e., a crystal) in which atoms in a metal are arranged regularly.
Alloy: a substance with metallic properties composed of two or more metals or the fusion of metals and nonmetals.
Phase: refers to the independent and uniform components in the metal or alloy with the same chemical composition, the same lattice structure, or the same atomic aggregation state, and a clear interface with other parts.
Organization: the organization refers to the internal microscopic appearance image of the material that can be directly observed with the naked eye or observed and resolved with a magnifying glass and a microscope.
Solid solution: a solid solution is a solid metal crystal in which atoms (compounds) of one (or several) component are dissolved into the lattice of another component while still maintaining the lattice type of the other component. There are two types of solid solution: interstitial solid solution and displacement solid solution.
Solid solution strengthening: since the solute atoms enter the gap or node of the solvent lattice, the lattice will be distorted and the hardness and strength of the solid solution will be increased. This phenomenon is called solid solution strengthening phenomenon.
Compound: a new crystalline solid structure with metallic properties is formed by the combination of alloy components.
Mixture: mechanical mixture: the structure composed of pure metal, solid solution, metal compound and other basic phases of the alloy in a fixed proportion is called mechanical mixture.
Ferrite: carbon in α- Interstitial solid solution (f) in Fe (iron with body centered cubic structure).
Austenite: carbon in γ- Interstitial solid solution (a) in Fe (iron with face centered cubic structure).
Cementite: a stable compound (Fe3C) formed by carbon and iron.
Pearlite: the organic combination of ferrite and cementite decomposed by eutectoid undercooled austenite.
Martensite: martensite is a kind of organization name of ferrous metal materials. Martensite (m) is carbon dissolved in α- The supersaturated solid solution of Fe is a metastable phase transformed from austenite through non diffusion phase transformation.
Troostite: pearlite (T) with a sheet spacing of about 300 ~ 800nm formed by isothermal or slow cooling of undercooled austenite after cooling to about 600 ~ 550 ℃.
Sorbite: mechanical mixture of ferrite and cementite obtained by normalizing or isothermal transformation of steel. Sorbite belongs to pearlite type, but its structure is finer than pearlite. Sorbite has good comprehensive mechanical properties (s).
Bainite: the metastable structure formed by ferrite and dispersed carbides distributed in the medium temperature range (so-called “bainite transformation temperature range”) from which the steel is undercooled to below the pearlite transformation temperature range and above the martensite transformation temperature range after austenitizing, that is, the product of bainite transformation. There are upper bainite and lower bainite (b).
Heat treatment:
1. Normalize: heat treatment process of heating steel or steel parts to an appropriate temperature above the critical point AC3 or ACM for a certain time and then cooling in air to obtain pearlite like structure.
2. Anneal: heat the hypoeutectoid steel workpiece to 20-40 ° C above AC3, keep it for a period of time, and then slowly cool it with the furnace (or bury it in sand or lime) to below 500 ° C and cool it in air.
3. Solution heat treatment: heat the alloy to the high-temperature single-phase region and keep it at a constant temperature, so that the excess phase is fully dissolved in the solid solution, and then quickly cooled to obtain the heat treatment process of supersaturated solid solution.
4. Aging: the phenomenon that the properties of the alloy change with time when it is placed at or slightly higher than room temperature after solution heat treatment or cold plastic deformation.
5. Solution treatment: fully dissolve various phases in the alloy, strengthen the solid solution, improve the toughness and corrosion resistance, eliminate stress and softening, so as to continue processing and forming.
6. Aging treatment: heat and keep warm at the temperature where the strengthening phase precipitates, so that the strengthening phase precipitates, hardens and improves the strength.
7. Quench: a heat treatment process for austenitizing the steel and cooling it at an appropriate cooling rate to make the workpiece undergo martensite and other unstable structural transformation in the whole or a certain range of the cross section.
8. Tempering: a heat treatment process that heats the quenched workpiece to an appropriate temperature below the critical point AC1 for a certain time, and then cools it with a satisfactory method to obtain the required structure and properties.
9. Steel carbonitriding: carbonitriding is a process of simultaneously infiltrating carbon and nitrogen into the surface layer of steel. Carbonitriding is also known as cyaniding, and medium temperature gas carbonitriding and low temperature gas carbonitriding (i.e. gas soft nitriding) are widely used. The main purpose of medium temperature gas carbonitriding is to improve the hardness, wear resistance and fatigue strength of steel. Low temperature gas carbonitriding is mainly nitriding, and its main purpose is to improve the wear resistance and bite resistance of steel.
10. Quenching and tempering treatment: generally, the heat treatment combining quenching and high temperature tempering is called quenching and tempering treatment. Quenching and tempering treatment is widely used in various important structural parts, especially those connecting rods, bolts, gears and shafts working under alternating loads. The mechanical properties of tempered sorbite obtained after quenching and tempering treatment are better than those of normalized sorbite with the same hardness. Its hardness depends on the high temperature tempering temperature and is related to the tempering stability of the steel and the cross-sectional dimension of the workpiece, generally between hb200-350.
11. Brazing: a heat treatment process in which two kinds of workpieces are heated, melted and bonded together with brazing filler metal.