Mold costs depe…
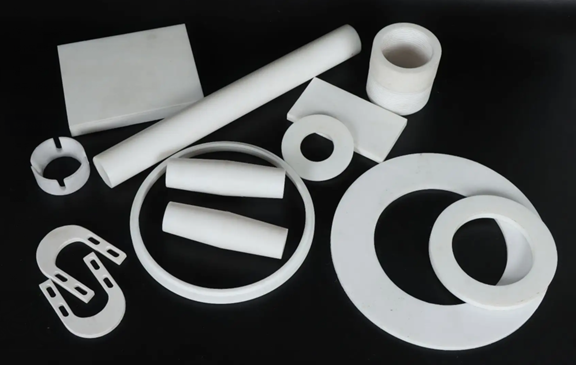
Explanation of terms related to injection molding (5)
1. What is the purpose of inserting inserts into plastic parts?
The purpose of inserting inserts into plastic parts is to improve the local strength, hardness, wear resistance, conductivity and magnetic conductivity of plastic parts, or to increase the stability of the size and shape of plastic parts, or to reduce the consumption of plastic.
2. What is the working principle of single parting surface injection mold?
The single parting surface injection mold is also known as the two plate injection mold. As shown in Fig. 5.4, when closing the mold, the moving mold and the fixed mold are closed under the guidance and positioning of the guide post 8 and the guide sleeve 9. The cavity is composed of the cavity on the fixed template 2 and the core 7 fixed on the moving template 1, and is locked by the mold locking force provided by the mold closing system of the injection machine. Then the injection machine starts to inject, and the plastic melt enters the cavity through the gating system on the fixed mold. The cavity is filled with melt, and the mold is opened after pressure maintaining, plastic replenishing and cooling. When opening the mold, the mold closing system of the injection machine drives the moving mold to retreat, the mold driven mold and the parting surface of the fixed mold are separated, the plastic part is wrapped on the core 7 and retreats with the moving mold. At the same time, the pull rod 15 pulls the main runner condensate of the gating system out of the gate sleeve. When the moving die moves a certain distance, the ejector rod 21 of the injection machine contacts the push plate 13, and the push plate mechanism starts to act, so that the push rod 18 and the pull rod 15 push the plastic part and the pouring system condensate out of the core 7 and the cold material cavity respectively, and the plastic part and the pouring system condensate fall from the die together, thus completing an injection process. When closing the mold, the push out mechanism relies on the reset rod and is ready for the next injection.
3. How is the single parting surface injection mold composed?
According to the composition of the mechanism, the single parting surface injection mold shown in Figure 5.3 can be divided into mold cavity, molding parts, gating system, guiding mechanism, ejector, temperature regulation system and structural parts
4. How is the cavity of single parting surface injection mold composed?
The cavity part of the mold used to form plastic parts. Since the mold cavity is the part that directly forms plastic parts, the shape of the mold cavity should be consistent with the shape of the plastic parts. The mold cavity is generally composed of cavity and core. This figure is composed of cavity 2, core 7, fixed template 1 and push rod 18.
5. How are the parts of single parting surface injection mold formed?
The parts constituting the cavity of plastic mold are collectively referred to as molding parts, which usually include core (internal shape of molded plastic parts) and cavity (external shape of molded plastic parts). This drawing is composed of fixed template 2, core 7 and moving template 1.
6. How is the gating system of single parting surface injection mold composed?
The flow channel that leads the plastic from the nozzle of the injection machine to the mold cavity is called the gating system. The gating system is divided into four parts: main flow channel, shunt channel, gate and cold material cavity. It is composed of gate sleeve 6, pull rod and the flow channel on fixed template 2.
7. How is the guiding mechanism of injection mold with single parting surface composed?
Guide parts are set to ensure the accurate alignment of the moving die and the fixed die when closing the die. Usually, there are guide columns, guide holes or inner and outer conical surfaces that are consistent with each other are set on the moving die and fixed die. This legend is composed of guide post 8 and guide sleeve 9.
8. How is the ejector of injection mold with single parting surface composed?
e for pushing plastic parts out of the mold during mold opening. In order to avoid the deflection of the ejector plate in the ejection process, the ejector device of some injection molds is also equipped with guide parts to keep the ejector plate moving horizontally. It is composed of push rod 18, push plate 13, push rod fixing plate 14, reset rod 19, main channel pull rod 15, support nail 12, push plate guide column 16 and push plate guide sleeve 17.
9. How is the temperature regulation and exhaust system of single parting surface injection mold composed?
In order to meet the requirements of injection process for mold temperature, the mold is equipped with cooling or heating system. The cooling system is generally provided with a cooling water channel in the mold. For heating, heating elements, such as electric heating elements, are installed in or around the mold. This drawing is composed of cooling water channel 3 and water nozzle.
In the process of injection molding, in order to exclude the gas in the cavity from the mold, it is often necessary to set up an exhaust system.
10. How are the structural parts of single parting surface injection mold composed?
It is used to install and fix or support formed parts and parts of the above-mentioned parts and mechanisms. The supporting parts are assembled together to form the basic framework of the injection mold. This drawing is composed of fixed die base plate 4, moving die base plate 10, cushion block 20 and support plate 11.
[express statement] this article is reprinted from the Internet. The purpose of reprinting is to convey more information. It does not mean that this website agrees with its views and is responsible for its authenticity. The copyright of this article belongs to the original author. The content is the author’s personal point of view. Skynet only provides reference and does not constitute any investment and application suggestions. If you need to reprint, please contact the original source. Speednet has the final right to interpret this statement..