Mold costs depe…
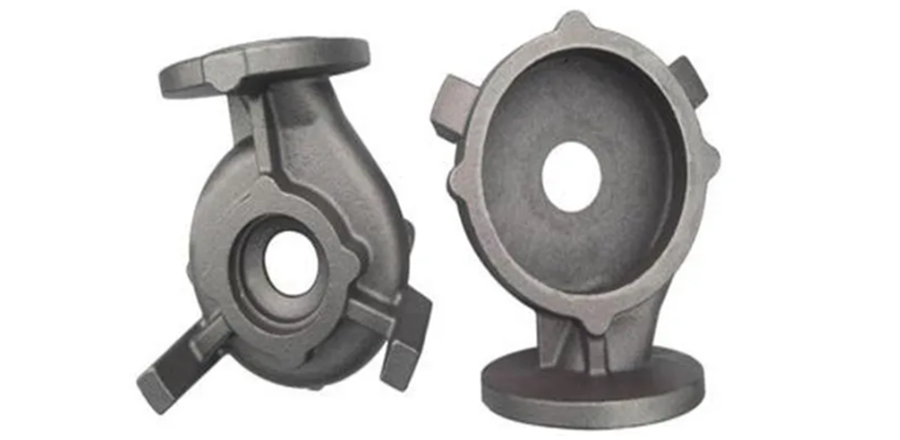
Difficult Problems in Production of Heat resistant Steel Castings
Heat resistant steel is often used to manufacture parts and components working under high temperature in industrial sectors such as boilers, steam turbines, power machinery, industrial furnaces, aviation, petrochemical, etc. In addition to high temperature strength and resistance to high temperature oxidation corrosion, these cast parts also require sufficient toughness, good machinability, weldability and certain structural stability according to different applications.
China began to produce heat-resistant steel in 1952. Later, some new low alloy heat strength steels were developed, so that the working temperature of pearlite heat strength steels was increased to 600 ~ 620 ℃; In addition, some new low chromium nickel oxidation resistant steels have been developed.
Heat resistant steel and stainless acid resistant steel cross each other in the scope of use. Some stainless steels have the characteristics of heat resistant steel and can be used as both stainless acid resistant steel and heat resistant steel.
Chromium, aluminum, silicon, which are elements formed by ferrite, can promote the formation of dense oxide film on the metal surface at high temperature to prevent further oxidation. They are the main elements to improve the oxidation resistance of steel and resistance to high-temperature gas corrosion. However, too high aluminum and silicon content will seriously deteriorate the room temperature plasticity and thermoplasticity. Chromium can significantly increase the recrystallization temperature of low alloy steel. When the content is 2%, the strengthening effect is the best.
Nickel and manganese can form and stabilize austenite. Nickel can improve the high temperature strength and carburization resistance of austenitic steel. Manganese can replace nickel to form austenite, but it damages the oxidation resistance of heat-resistant steel.
Vanadium, titanium and niobium are strong carbide forming elements, which can form fine dispersed carbides and improve the high temperature strength of steel. The combination of titanium, niobium and carbon can also prevent intergranular corrosion of austenitic steel under high temperature or after welding.
Carbon and nitrogen can expand and stabilize austenite, thus improving the high temperature strength of heat-resistant steel. When the steel contains more chromium and manganese, the solubility of nitrogen can be significantly improved, and nitrogen alloying can be used to replace expensive nickel.
Boron and rare earth are trace elements in heat-resistant steel. The boron dissolved in the solid solution will distort the crystal lattice, and the boron on the grain boundary can prevent the element diffusion and grain boundary migration, thus improving the high temperature strength of the steel; Rare earth elements can significantly improve the oxidation resistance of steel and improve the thermoplasticity.
Heat resistant steel is usually smelted in electric arc furnace or induction furnace. Vacuum refining and secondary refining are often used for those with high quality requirements.
It is difficult to process and deform some high alloy heat-resistant steels by casting. It is not only cheaper to produce castings than rolled products, but also has higher lasting strength. Therefore, heat resistant cast steel accounts for a large proportion in heat resistant steel.
In addition to sand casting, precision casting can also be used to obtain products with smooth surface and accurate size. Centrifugal casting is often used for the high-temperature furnace tubes used for the cracking of synthetic ammonia and ethylene.
Heat treated pearlitic high strength steel is usually used after normalizing or quenching and tempering; Martensitic heat-resistant steel is quenched and tempered to stabilize the structure and obtain good comprehensive mechanical properties and high temperature strength.
Ferritic steel in the production line of heat-resistant steel annealing tank cannot be strengthened by heat treatment. In order to eliminate the internal stress caused by cold plastic deformation processing and welding, annealing treatment can be carried out at 650~830 ℃. After annealing, it can be cooled quickly so as to quickly pass the 475 ℃ brittle temperature range.
Austenitic oxidation resistant steels are mostly treated by high temperature solution heat treatment to obtain good cold deformation. Austenitic heat strength steel is first treated by high temperature solution treatment, and then aged at 60~100 ℃ higher than the service temperature to stabilize the structure and precipitate the second phase to strengthen the matrix.
Heat resistant cast steel is mostly used as cast, and corresponding heat treatment is also adopted according to the type of heat resistant steel.