Mold costs depe…
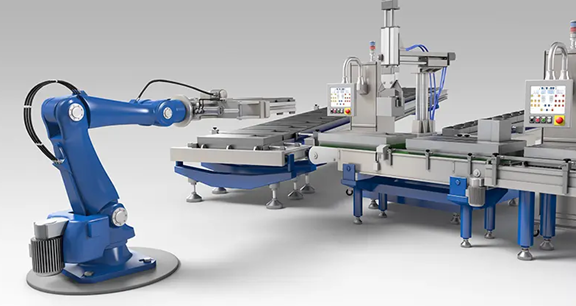
Detailed to the environmental temperature difference, a abnormal form of assembly technical requirements
1. Basic requirements
1.1 the assembly must be carried out in accordance with the design, process requirements, this regulation and relevant standards.
1.2 the assembly environment must be clean. The assembly environment temperature, humidity, dust prevention, lighting and shockproof of high-precision products must comply with relevant regulations.
1.3 all parts (including purchased and outsourced parts) must have inspection certificates before assembly.
1.4 parts must be cleaned and cleaned before assembly, without burr, flash, scale, rust, chips, sand, dust and oil, and shall meet the corresponding cleanliness requirements.
1.5 parts shall not be bumped, scratched or rusted during assembly.
1.6 parts with wet paint shall not be assembled.
1.7 for relatively moving parts, lubricating oil (grease) shall be added between the contact surfaces during assembly.
1.8 the relative position of all parts and components shall be accurate after assembly.
1.9 in principle, it is not allowed to step on the machine during assembly. Special measures shall be taken when special parts must be on the machine. The stepped parts shall be covered with protective covers. The operator must wear flat shoes to prevent damage to the paint film. It is strictly prohibited to step on low strength parts such as batteries and non metals.
2. Requirements for connection method
2.1 screw and bolt connection
2.1.1 when fastening screws, bolts and nuts, it is strictly prohibited to strike or use inappropriate screwdrivers and wrench. After fastening, the screw groove, nut, screw and bolt head shall not be damaged.
2.1.2 fasteners with specified tightening torque requirements shall be tightened with torque wrench according to the specified tightening torque. For bolts without specified tightening torque, the tightening torque can refer to the provisions in Appendix I.
2.1.3 when the same part is fastened with multiple screws or bolts, each screw (bolt) shall be tightened clockwise, staggered and symmetrically step by step. If there is a locating pin, it shall start from the screw or bolt close to the locating pin.
When installing thin nuts, install nuts first and then thin nuts.
2.1.5 after the screws, bolts and nuts are tightened, the screws and bolts shall generally expose 1-2 pitches of the nuts.
2.1.6 after the screws, bolts and nuts are tightened, the bearing surface shall fit with the fastened parts.
2.2 pin connection
2.2.1 generally, the end face of the locating pin shall be slightly higher than the surface of the part. After the conical pin with screw tail is installed into the relevant parts, its big end shall sink into the hole.
2.2.2 after the cotter pin is installed into relevant parts, its tail shall be separated by 60 ° – 90 °.
2.2.3 when assembling important conical pins, they shall be painted with the hole, and their contact length shall not be less than 60% of the working length, and shall be distributed on both sides of the joint surface.
2.3 key connection
2.3.1 the two sides of the keyway of the flat key and the fixed key shall be in uniform contact, and there shall be no gap between their mating surfaces.
2.3.2 after the clearance fit key (or spline) is assembled, when the relatively moving parts move along the axial direction, there shall be no uneven tightness.
2.2.3 after the hook head key and wedge key are assembled, the contact area shall not be less than 70% of the working area, and the non-contact parts shall not be concentrated in one place; The length of the exposed part shall be 10% ~ 15% of the length of the slope.
2.4 . riveting
2.4.1 the materials, specifications and dimensions of riveting must meet the design requirements. The processing of rivet holes shall comply with relevant standards.
2.4.2 during riveting, the surface of riveted parts shall not be damaged or deformed.
2.4.3 except for special requirements, generally, there shall be no looseness after riveting. The head of the rivet must be in close contact with the riveted parts and should be smooth and round.
2.5 assembly of rolling bearing
2.5.1 the bearing must be clean before assembly.
2.5.2 for grease lubricated bearings, after assembly, about half of the cavity shall be filled with lubricating grease that meets the requirements.
2.5.3 when assembling with the press in method, special press tools or rods or sleeves shall be padded on the interference fit ring, and the pressure or striking force shall not be transmitted through the rolling element and cage.
2.5.4 the end face of the bearing inner ring shall generally be close to the shaft shoulder, and shall not be greater than 0.05mm for tapered roller bearing and centripetal thrust bearing, and not greater than 0.1mm for other bearings.
2.5.5 after the bearing outer ring is assembled, the contact between the bearing cover at the positioning end and the washer or outer ring shall be uniform.
2.5.6 when assembling removable bearings, they must be installed according to the inner and outer rings and alignment marks, and shall not be installed reversely or mixed with other inner and outer rings of bearings.
2.5.7 for bearings assembled with adjustable head, the numbered end shall be outward during assembly for easy identification.
2.5.8 for the bearing with eccentric sleeve, the tightening direction of eccentric sleeve shall be consistent with the rotation direction of shaft during assembly.
2.5.9 after the rolling bearing is installed, the rotation relative to the moving parts shall be flexible and light without jamming
2.5.10 the axial clearance of single row tapered roller bearing, thrust angular contact bearing and two-way thrust ball bearing during assembly shall meet the drawing and process requirements.
2.5.11 the outer ring of the bearing shall be in good contact with the open bearing seat and the semicircular hole of the bearing cover. When inspected by the coloring method, it shall be in uniform contact with the bearing seat within 120 ° symmetrical to the center line; Contact with the bearing cover evenly within 90 ° symmetrical to the centerline. Within the above range, when checking with a 0.03mm feeler gauge, one third of the width of the outer ring shall not be inserted.
2.5.12 assemble radial clearance adjustable radial bearings on both sides of the shaft, and when the axial displacement is limited by the end covers at both ends, only one end of the bearing can be close to the end cover, and the other end must have axial clearance C= α △ Tl + 0.15 (L): center distance between two axles (mm) α: Linear expansion coefficient of shaft material △ T: the difference between the maximum working temperature of the shaft and the ambient temperature (℃) 0.15: the remaining gap after thermal expansion of the shaft (mm)).
3. Assembly of sprocket chain
3.1 the fit between sprocket and shaft must meet the design requirements.
3.2 the geometric center plane of the teeth of the driving sprocket and the driven sprocket shall coincide, and the offset shall not exceed the design requirements. If not specified in the design, it shall generally be less than or equal to two thousandths of the center distance between two wheels.
3.3 when the chain is engaged with the sprocket, the working edge must be tightened to ensure stable engagement.
3.4 the sag of the non working edge of the chain shall meet the design requirements. If it is not specified in the design, it shall be adjusted according to 1% ~ 2% of the center distance between the two sprockets.
4. Assembly of belt and pulley
4.1. The position degree of the symmetrical center plane of the pulley groove of the same circuit is: when the center distance is less than 1.2m, it is not greater than 0.3% of the center distance of the pulley; When it is greater than or equal to 1.2m, it shall not be greater than 0.5% of the center distance of the pulley.
4.2 the tension of each transmission belt shall meet the requirements of the inspection card of Futian “Gushen 2” system
5. Assembly of hydraulic system
5.1 the pipelines of the hydraulic system must be derusted and cleaned before assembly. Pay attention to dust and rust prevention during assembly and storage.
5.2. All kinds of pipes shall be free of dents, folds, flattening, cracks and other phenomena. The bending part of the pipeline shall be smooth and free of torsion.
5.3 the arrangement of pipelines shall be neat and convenient for the adjustment and maintenance of the hydraulic system.
5.4 the hydraulic oil injected into the hydraulic system shall meet the design and process requirements.
5.5 after assembly, the hydraulic pipeline and components shall be free of oil leakage. In order to prevent leakage, sealing filler and sealant are allowed to be used during assembly, but they shall not enter the system.
5.6. The hydraulic control system and steering system shall be flexible without jamming.
5.7 after the hydraulic system is installed, the operation test shall be carried out according to relevant standards.
5.8 other requirements for hydraulic system and hydraulic components shall comply with the provisions of GB / t3766.
6. Assembly of electrical system
6.1 electrical components shall be tested and inspected before assembly, and unqualified ones cannot be assembled.
6.2 the numbers and signals displayed by instruments and indicators shall be clear and accurate, and the switch shall work reliably.
6.3 wiring and connection shall be carried out in strict accordance with the requirements of electrical assembly drawings.
6.4 the insulation layer of all wires must be intact, and the fine copper wire at the wire stripping head must be tightened and tinned when necessary.
6.5. The welding spot must be firm, and there shall be no desoldering or false welding. The welding spot shall be smooth and uniform.
7. Balance
7.1 the threshing drum, the belt pulley with stepless speed change and rotating speed exceeding 400R / min and weight greater than 5kg shall be subject to static balance or dynamic balance test, and the balance accuracy shall not be lower than G6 Level 3.
7.2. The unbalanced mass of rotating parts can be corrected by the following methods:
7.2.1. Add weight (counterweight) with repair welding, threaded connection, etc.
7.2.2 remove the mass with drill pin (weight removal).
7.2.3 change the number and position of balance weights.
7.3 when using the method of adding quality for correction, it must be firmly fixed to prevent loosening or flying out in the process of work.
7.4 when correcting by removing the quality, pay attention not to affect the stiffness, strength and appearance of the parts.
7.5 for the combined rotary body, after overall balance, it is not allowed to move or replace parts arbitrarily.
8. Each adjusting mechanism shall ensure convenient operation, flexible and reliable adjustment. The adjustment range of each component shall reach the specified limit position.
9. Each operating mechanism shall ensure light and flexible operation and moderate tightness. All controls requiring automatic return shall be able to return to the original position automatically after the control force is removed.
10. Final assembly
10.1 during the final assembly, the attached accessories shall also be trial assembled, and the design requirements shall be ensured.
10.2 the ground clearance of rigid header shall be consistent, and the allowable difference shall not be greater than 15mm.
10.3. The traveling brake device and parking brake device shall ensure the reliable parking of the harvester.
10.4 the engine shall be started smoothly and stably, and the flameout shall be complete and reliable; It shall be able to start smoothly when the ambient temperature is not lower than – 50 ℃.
10.5 all marks of the whole machine shall be pasted to the designated position according to the design requirements, and shall not be skewed or uneven.
10.6 before leaving the factory, the test machine shall ensure that the main machine has more than 2 hours of operation records.