Mold costs depe…
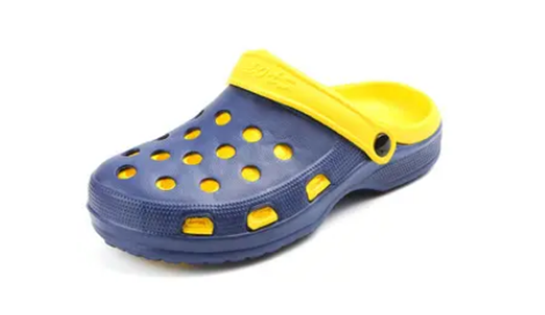
Design Guide for Cladding and Insert Molding
Cladding molding is an injection molding process that allows adding an additional layer of resin to existing molded parts to provide a combination of properties that cannot be provided by a single material. One of the most common applications is to add a layer of soft, functional, hands-on rubber like material, usually TPE (thermoplastic elastomer), to the hard substrate. The other is to change or enhance the appearance of parts or “cosmetics” by coating materials with different colors or surface treatments. Cladding molding materials can be found on everything from medical devices and hand tools to toothbrushes, as well as gaskets and seals in components.
As a manufacturing process, cladding molding can provide excellent adhesion between different materials without manual assembly of materials. Because the process can be automated to varying degrees, it is cost-effective. Moreover, by reducing the complexity of assembly, it can help reduce costs and speed up the launch of products and equipment. But most importantly, it can greatly improve the range of material properties available to product developers.
There are two main methods of cladding molding: secondary molding, secondary spray molding and Pick-n-place molding. The former uses a single production mold, while the latter uses two molds.
Material selection for overmolding can be complex. The base material and the secondary resin can complement each other, but to be effective, they must be compatible. The choice depends not only on the application of the overmolded part, but also on the method used to produce the overmolded part. Since the process and results of secondary molding are more complex than those of single injection molding, it is helpful to seek the opinions of resin experts when selecting materials.
Cladding injection molding and Pick-n-Place overlapping injection molding
Let’s first look at cladding injection molding, which involves molding a substrate with one material and then quickly cladding injection molding with another material. This is usually a highly automated process. The second method is “pick-n-place” molding, in which the whole batch of substrate components are molded; Then, manually place the substrate parts into the second mold one at a time, and inject the coated resin into the mold to produce the finished parts.
There are three main methods for cladding molding:
Transfer wrap molding is a robot program in which a substrate part is mechanically removed from one mold and placed in another, larger mold. The overmolding material is injected to fill the empty space in the second mold, usually when the next substrate is produced in the first mold.
Rotary envelope molding is another robotic process in which the mold itself moves from one injection station to another to allow injection of the base material and envelope molding material.
Core back cladding can only be used for very specific linear geometry. The mold is composed of a sliding section, which is pulled back after the injection of the first material and is set to make room for the second injection material.
All three overmolding methods layer the cladding molding material onto a warm substrate, which facilitates chemical bonding. These three products all require special equipment and expensive molds, but due to their high automation, they are cost-effective in mass production, usually more than 10000 pieces, usually more than 100000 pieces.
Pick-n-place molding uses two completely independent molds. A batch of substrate parts is manufactured and cooled in a mold. They are then placed by hand in a second larger mold that houses the substrate components and leaves room for the overmolding material to inject the cladding molding material onto the substrate. Compared with the secondary injection method, the equipment used in this process is not too complicated, the mold is simpler, and the installation process is simplified and accelerated.
Compare cladding methods
Although the manual placement of the substrate into the secondary mold is slower than the robotic process, it can generally complete the production of medium and low volume parts faster and at significantly lower cost. The biggest challenge of Pick-n-place molding is to reduce the chemical adhesion between the cladding molding material and the cooling substrate. In order to maximize adhesion, the substrate must be treated carefully to prevent contamination of surfaces that may affect adhesion. In addition, proper material selection also helps to ensure good adhesion in pick position applications.
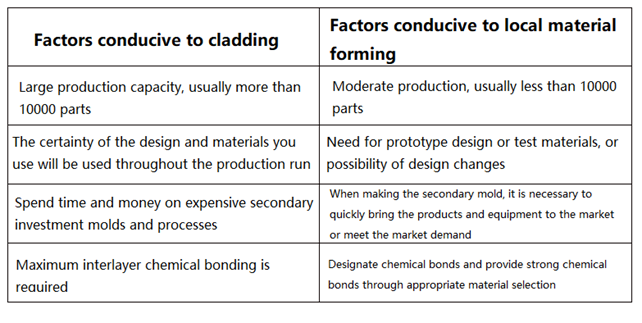
Function of adhesion
Adhesion between the resin layers helps prevent layer separation. Depending on the part geometry, the glue may be subjected to multiple forces that pull the layers apart.
These measures include:
1. Butt joint separation caused by direct tension
2. Shear caused by tension parallel to bonding interface, resulting in separation of lap joint
3. Stripping that usually starts from the edge and propagates along the interface between materials
Bond strength is particularly important when one of the materials is an elastomer, which can bend and pull away from the substrate. This applies to both thermoplastic elastomers (softened when heated) and thermosetting materials (not softened).
There are two main ways to combine layers. One is the actual chemical combination of two resin layer interfaces; The other is mechanical bonding, which depends on the physical geometry of the interface. Acceptable bonding is achieved through the combination of part design, material selection, mold design and molding process.
Chemical bonding compatibility.
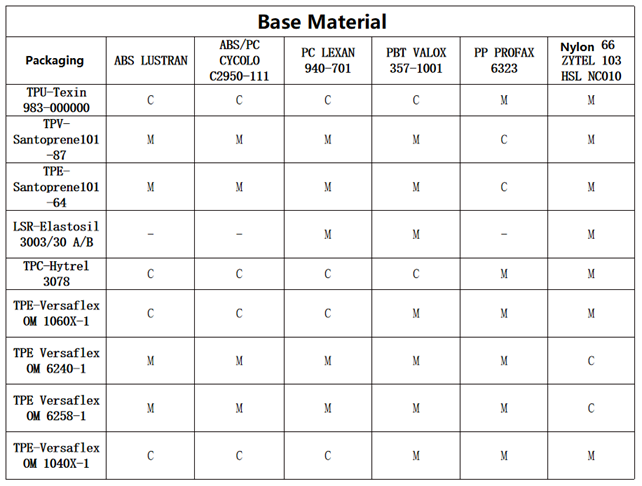
Cladding molding materials
There are thousands of possible combinations of substrate and cladding molding materials. In addition to some common possibilities, if you need special characteristics, the material supplier can identify many other possibilities.
In addition to compatibility and adhesion, there are many factors that affect the choice of coating molding resin. If the goal is cushioning, the thickness of the cladding molding material is as important as the softness of the material itself. Regardless of the material selection, thin layers, usually less than 0.40 inch (10mm), will feel hard. For this reason, many consumer products will have a higher row of ribs to increase the perceived thickness, while reducing the amount of cladding molding materials and increasing their flexibility. The actual flexibility of the material is not directly related to its hardness or hardness tester. A better measurement is the bending modulus, which measures the bending resistance of materials. Materials with lower bending modulus will feel softer. Although there are a variety of resins suitable for cladding, there are also some elastomers, such as Versaflex, that can be specifically used for cladding applications.
If the purpose of the cladding is to enhance grip, the friction coefficient of the material represents its tactility. For example, thermoplastic elastomers (TPE) usually have a high coefficient of friction. In the case of cushioning, the durometer is not a reliable measure of material grip. Since many resins, including thermoplastics and thermosets, have a range of properties, it is useful to consult with experts related to rapid addition when selecting the appropriate resin grade for a particular application.
Like cladding molding, insert molding injects resin into another material, but the other material is usually metal, while the injected plastic material is usually rigid plastic rather than plastic substrate. Metal electrical components or custom machined metal parts are usually embedded in plastic in this way. Similarly, threaded inserts can be molded into plastic parts to assemble plastic parts, such as equipment housings, more securely and durably. Insert molding is an alternative method of inserting metal parts through hot riveting or ultrasonic welding. By this method, molded plastic parts are partially melted to allow insertion of metal parts. Compared with other methods, insert molding is more controllable and allows better packaging. The molded insert also eliminates the need for the secondary insert installation process, saving time and money.
Because the insert is metal, it must be placed in the mold and then sealed with plastic. For mass production, this can be done by robots, but for low to medium mass production of insert molds, pick-n-place is a manual process. There is no chemical bonding between the metal insert and the plastic, so the insert and resin parts must be designed for mechanical bonding.