Mold costs depe…
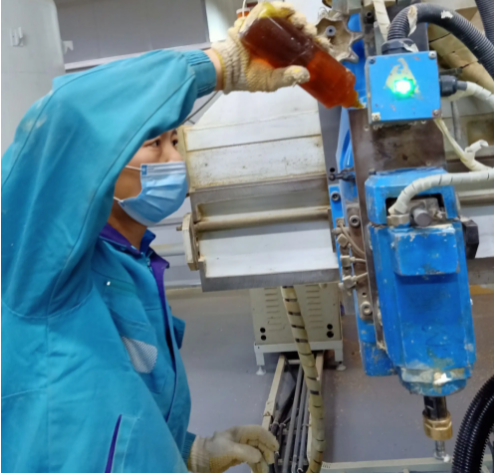
Correct maintenance methods for CNC machine tools
CNC lathe is an automatic machine tool with high precision and efficiency, which can process complex workpieces such as linear cylinder, oblique cylinder and arc. In order to ensure the working accuracy of the lathe and extend its service life, it is necessary to carry out reasonable maintenance.
The common methods for maintenance and repair of CNC machine tools are: oil pouring lubrication, oil splashing lubrication, oil rope guide lubrication, marble oil cup lubrication, grease cup lubrication, oil pump oil delivery lubrication.
The parts in the spindle box are lubricated by oil pump circularly or splash lubrication. The lubricating oil in the box is generally replaced every three months. There is an oil window on the spindle body. If there is no oil output in the oil window, it indicates that the oil pump oil delivery system is faulty. Stop the machine immediately to check the cause of oil cutoff, and start the lathe after repair.
In addition to the gear splash lubrication, the gear and bearing in the feed box are also lubricated with an oil tank lubricated by oil rope guide oil, which shall be oiled once per shift. The intermediate gear shaft bearing of the exchange gear box is lubricated with a grease cup once per shift. The bed guide rail and sliding plate guide rail shall be wiped clean before and after work and oiled with an oil gun.
The daily maintenance requirements of the lathe are as follows:
1、 After working every day, cut off the power supply, and ensure that all surfaces of the lathe, all housings, all guide rail surfaces, lead screws, and smooth screws are free of oil, iron filings, and the lathe surface is clean.
2、 It is required to maintain the cleanness and lubrication of the guide rail surface of the bed and the guide rail surface of the middle slide plate every week. Generally, the first level maintenance is required after the CNC lathe runs for 500 hours. The maintenance work is mainly carried out by operators with the cooperation of maintenance personnel. During maintenance, the power must be cut off first, and then the following sequence and requirements shall be followed: first, the mainshaft shall be maintained. First, clean the oil filter to make it free of impurities. Second, check whether the spindle lock nut is loose and whether the set screw is tightened. Third, adjust the clearance of brake and clutch friction plate. Secondly, the maintenance of the exchange gearbox. First, clean the gear and shaft sleeve, and inject new grease into the oil cup. Second, adjust the meshing clearance of gears. Third, check the shaft sleeve for shaking.
3、 Maintenance of sliding plate and tool rest.
4、 Maintenance of tailstock (wipe the surface and add oil for lubrication).
5、 Maintenance of the lubrication system. First, clean the cooling pump and oil filter. Secondly, ensure smooth oil passage. Third, check the oil quality and keep it in good condition (the oil standard is clear)
6、 Maintenance of electrical appliances. First, clean the dust on the motor and electrical box. Secondly, the electrical devices are fixed neatly.
7、 Appearance maintenance. First of all, clean the surface and cover of the CNC lathe, and keep the inside and outside clean without rust and oil stain. Secondly, check and supplement all screws and handles. After cleaning and wiping, all parts shall be lubricated as necessary.
It is worth noting that the power supply must be cut off during the maintenance of the machine, and then the maintenance can be carried out according to the steps.