Mold costs depe…
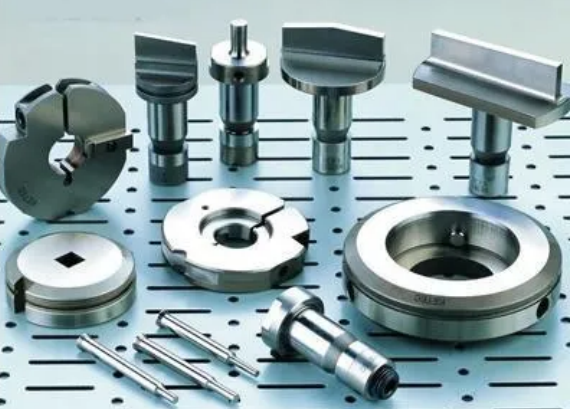
Common technology analysis of ultra precision machining and the development process of key technologies
Based on the cold machining technology of material removal, since the United States used a single point diamond tool to process electrolytic copper in the early 1960s and successfully cut the mirror, qualitative changes have taken place in the machining accuracy, which promoted the emergence and development of ultra precision machining technology. It is generally believed that the machining technology with the size and shape position error of the machined parts less than a few tenths of a micron and the surface roughness between a few nanometers and a dozen nanometers is an ultra precision machining technology. At present, ultra precision machining, from single diamond turning to the comprehensive application of modern ultra precision grinding, grinding, polishing and other methods, has become an important part of modern manufacturing technology. Its products involve national defense, aerospace, metrology and detection, biomedicine, instruments and other fields.
Looking back on the 20th century, every major scientific and technological achievement made by mankind is closely related to manufacturing technology, especially ultra precision machining technology. In a sense, ultra precision machining undertakes the important mission of supporting the latest scientific discoveries and inventions. Ultra precision machining technology plays an extremely important role in the development of space vehicles, weapons and satellites. Some people have studied the relationship between the weapon systems of the United States and its allies and ultra precision processing technology in the Gulf War, and found that it is closely related to ultra precision processing technology in terms of spy satellites, over the horizon air-to-air attack capability, precision guided ground attack capability, night warfare capability and electronic countermeasure technology. It can be said that without high-level ultra precision machining technology, there will be no really strong national defense.
General technology and development of ultra precision machining
Ultra precision machining can be divided into ultra precision cutting, ultra precision grinding, grinding, polishing and ultra precision micro machining. Although they have great differences in principles and methods, they have many inheritable common technologies. Generally speaking, they have common characteristics in the following aspects:
1.1 ultra precision moving parts
Ultra precision machining is a machining process that uses the strictly constrained relative motion between parts and tools to micro cut materials on ultra precision machine tools to obtain high shape accuracy and surface finish. Ultra precision moving parts are the key to the above relative motion. They are divided into rotary moving parts and linear moving parts.
High speed rotary moving parts are usually the spindle of machine tools. At present, Aerostatic Spindle and hydrostatic spindle are widely used. The main feature of Aerostatic Spindle is high rotation accuracy. For example, nanoform250 lathe of pneumo company adopts Aerostatic Spindle, and the rotation accuracy is better than 0.05 μ m。 Its disadvantage is the low stiffness, which is generally less than 100 n/ μ m。 In recent years, there are many researches on improving the stiffness of air floating spindle. For example, Kugler company in Germany has developed a hemispherical air floating spindle with a stiffness of up to 350 n/ μ m ; Japanese scholars use the active control method to increase the spindle stiffness and improve the rotation accuracy at the same time; The static stiffness of the membrane structure passively compensated air bearing developed by Eindhoven University of science and technology in the Netherlands can tend to infinity, and the dynamic stiffness can be greatly improved. Compared with air bearing spindle, hydrostatic spindle has the advantages of large bearing capacity, large damping and good dynamic stiffness, but it is easy to heat and the accuracy is slightly poor.
Linear moving parts refer to machine tool guide rails, which also include aerostatic guide rails and hydrostatic guide rails. Because the bearing capacity of the guide rail is often larger than the spindle of the machine tool and the movement speed is low, the latter is mostly used in ultra precision machine tools. For example, the high-pressure hydrostatic guide rail adopted by lodtm developed by LLNL in the United States has a straightness error of less than 0.025 μ m/1000 mm。 Similarly, the active control method is suitable for improving the static stiffness of air floating guide rail. Mizumoto of Tottori University in Japan applied this technology to the ultra precision lathe designed by them to improve the straightness of guide rail.
1.2 ultra precision motion drive and transmission
In order to obtain high motion accuracy and resolution, ultra precision machine tools have high requirements for motion drive and transmission system, which requires not only stable ultra-low speed motion characteristics, but also large speed regulation range, but also good electromagnetic compatibility.
Generally speaking, there are two ways of ultra precision motion drive: direct drive and indirect drive. Direct drive mainly adopts linear motor, which can reduce the error caused by intermediate links. It has the advantages of good dynamic characteristics, simple mechanical structure and low friction. The main problems are short stroke and small thrust. In addition, due to the small friction, it is easy to oscillate, which needs to be compensated by excellent control strategy. At present, in addition to small stroke motion, the application of linear motor in ultra precision machine tools is still in the experimental stage.
Indirect drive is to generate rotary motion by the motor, and then convert the rotary motion into linear motion through the motion transmission device. It is the mainstream of motion driving mode of ultra precision machine tools at present. The motor usually adopts DC servo motor with good low-speed performance, such as DM and Dr series direct drive servo actuator of American parrk Hannifin company, with large output torque and position control resolution of 1 / 640000. The motion transmission device is usually composed of coupling, lead screw and nut. Their accuracy and performance will directly affect the motion stability and accuracy, and it is also the main error source of indirect driving mode. MIT has designed two kinds of couplings, which adopt ball groove and flexure hinge structure respectively, to eliminate different shaft errors of motor and lead screw. The National University of Defense Science and technology of China has designed a frame floating unit, which is used to connect the nut and the worktable, and can eliminate the motion error in four directions. High precision ball screw is often selected as the lead screw. In addition, air bearing lead screw and magnetic bearing lead screw are also used for the experimental research of ultra precision machine tools. For example, the resolution of air bearing / magnetic bearing lead screw developed in Russia has reached 0.01 μ m。 Fukada of Shinjuku University in Japan converts torque into micro displacement by inserting elastomer between sliding lead screw, nut and worktable, so that the sliding lead screw can achieve nano resolution.
There is also a breakthrough in the traditional innovative research in the driving mode. For example, the torsion wheel friction device developed by Mizumoto of Tottori University in Japan has a resolution of nano; The resolution of the torsion wheel friction device developed by the University of national defense science and technology of China is also close to the nanometer level.
1.3 ultra precision machine tool numerical control technology
Ultra precision machine tool requires its CNC system to have high programming resolution (1 nm) and fast interpolation function (interpolation cycle 0.1 ms). The master-slave hardware structure based on PC and digital signal processing chip (DSP) is the trend of ultra precision numerical control, such as Nan opath and precision’s ultrapath TM in the United States. The development and application of hardware motion control module (PMAC) of NC system is more and more widely, which improves the reliability and reconfigurability of this kind of NC system. YH-1 numerical control system developed by the University of national defense science and technology of China adopts asw-824 industrial integration PC workstation as the host and ADSP2181 signal processor module to form a high-speed lower servo controller.
In terms of NC software, openness is a development direction. Foreign researches on Open CNC systems include OS ACA of the European community, OMAC of the United States and osec of Japan. Based on the development direction of multi degree of freedom of machine tool assembly software in China’s National Defense University, it is proposed that the machine tool can be assembled arbitrarily according to the development direction of multi degree of freedom of software.
1.4 ultra precision motion detection technology
In order to ensure that the ultra precision machine tool has sufficient positioning accuracy and tracking accuracy, the NC system must adopt the full closed-loop structure, and high-precision motion detection is a necessary condition for full closed-loop control. The dual frequency laser interferometer has high resolution (for example, the resolution of Zygo ax10mtm 2 / 20 is 1.25nm) and high stability, and has a large measurement range. It is suitable to be used as the linear displacement sensor of machine tool motion. However, the dual frequency laser interferometer is too demanding for the environment, and it is very difficult to use and adjust. Improper use will greatly reduce the accuracy. According to our experience, the grating ruler produced by Heidenhain company in Germany is more suitable for motion detection of ultra precision machine tools. For example, lip401 of the company has a material length of 220mm and a resolution of 2nm. It is made of zerodur material, almost reaching zero expansion coefficient (0.1 ppm / k), and the gap between dynamic and static ruler is 0.6 ± 0.1mm. It has low environmental requirements and is easy to install and use. For example, Heidenhain grating ruler is used in nanoform2500 and optim2400 ultra precision lathes.
1.5 layout and overall technology of ultra precision machine tools
Modularization and componentization are important technical means for ultra precision machine tools to enter the market. For example, anorad company of the United States produces various spindles, guide rails and turntables. Users can form one-dimensional, two-dimensional and multi-dimensional ultra precision motion control platforms and machine tools according to their own needs. When developing ultra precision machine tools, the layout is very critical. Ultra precision machine tools are often very different from traditional machine tools in structural layout. The popular layout is “t” layout, which makes the overall stiffness of the machine tool high and the control relatively easy. For example, most ultra precision lathes produced by pneumo company adopt this layout. Modularization makes the layout of machine tools more flexible and changeable. For example, the ultra precision grinder developed by Japan super silicon crystal research Co., Ltd. is used to grind super large silicon wafers, and the triangular rhombic pentahedron structure is used to improve the stiffness; Zeiss has developed a 4-axis precision grinder as100 for machining free-form surface. In addition to x, Z and C axes, the machine tool is added with a axis to control the cutting point of the grinding wheel when machining free surface.
In addition, some ultra precision machining machines are designed for special parts. For example, large high-precision astronomical telescopes are processed with stress deformation discs, and some aspheric mirrors are processed with computer-controlled optical surface forming technology (CCOS). These machines have a completely different structure from general-purpose machines. It can be seen that the structure of ultra precision machine tool has its distinct personality, which requires special design considerations and design means.
1.6 other important technologies
Ultra precision environmental control, including constant temperature, constant pressure, vibration isolation, humidity control and cleanliness control. In addition, ultra precision machining is very dependent on cutting tools, and the machining process is also very important. There are special requirements for the material and structure of ultra precision machine tools.
2 ways to improve the precision of ultra precision machining
Generally, the causes of ultra precision diamond cutting errors can be simply divided into the following categories: ① geometric errors in machine tool parts manufacturing and assembly; ② Thermal deformation error caused by external and internal heat sources of the machine tool; ③ Force deformation caused by self weight of machine tool and cutting force; ④ Servo error (following error) of machine tool shafting; ⑤ Other errors, such as NC interpolation algorithm error and environmental errors such as external vibration and humidity change.
The research results show that more than 70% of the errors of ordinary precision machine tools come from the first two items, while ultra precision machine tools have higher accuracy requirements, and each error may become the main contradiction that makes the accuracy of parts out of tolerance. Therefore, the above-mentioned errors should be comprehensively compared and controlled. For ultra precision parts, contour accuracy is an important indicator of comprehensive quality. In the process of ultra precision diamond cutting, the motion accuracy of machine tool mechanical system plays a decisive role in the contour accuracy. Due to the different emphasis of the measures taken to improve the contour accuracy, there are three different methods to solve this problem: open-loop method, closed-loop method and compensation method.
(1) Open loop method: This is a method to improve the motion accuracy of machine tool mechanical system by simply improving the performance of machine tool parts. The guide rail with ideal straightness (such as hydrostatic guide rail and aerostatic guide rail), spindle with higher rotation accuracy (such as hydrostatic spindle and Aerostatic Spindle), high-performance motor (such as dynaserv motor, the minimum output pulse can reach 2.53 angular seconds), and various precision driving modes (such as ball screw, hydrostatic screw, friction drive, linear drive, etc.), Improve the response speed and positioning accuracy of the mechanical system. However, friction and clearance are common in mechanical systems, which will produce stick slip when moving at low speed and backward when moving in reverse. In order to improve the position accuracy, the mechanical transmission system also needs enough connection stiffness to overcome the elastic deformation. To achieve high accuracy with open-loop method means higher cost.
(2) Closed loop method: the full closed loop control method has been widely used in ultra precision machine tools, such as the ultra precision diamond lathe successfully developed by LLNL in the United States, rank pneumo in the United Kingdom and granfield University.
The closed-loop control of the above ultra precision machine tools adopts the feedforward plus PID control method. This traditional control method has good stability and high reliability. PMAC motion control board is the representative of this controller. Ultra precision CNC system requires nanometer motion resolution, so it requires shorter interpolation period (less than 1 ms) and control period (less than 0.1 ms). In addition, according to the characteristics of ultra precision machining, multi axis linkage is required to generate high-order curves and surfaces. Based on the traditional control algorithm, the tracking accuracy can be greatly improved by using cross coupling control, optimal preview control (OPC), inverse compensation filter (IKF) control, sliding mode control, notch and feedforward.
(3) Compensation method: in the 1970s and early 1980s, error compensation technology was successfully applied to coordinate measuring machines (CMM). In the 15 years from 1980 to 1995, due to the use of error compensation, the production cost of CMM has been reduced by nearly 20 times on the basis of improved performance. The operating environment and working conditions of CNC machine tools are more complex than CMM. However, with the development of various measurement and control technologies, the technology of motion error, positioning error and thermal deformation error compensation for ultra precision machine tools has gradually matured. For example, the nano form series ultra precision lathe has the functions of in-situ measurement and error compensation. It can be seen that it is an inevitable trend to compensate the machining accuracy of ultra precision machine tools by computer software in order to improve the accuracy and reduce the cost. The future ultra precision machine tools will not only improve the machining accuracy, but also be more intelligent, such as the ability to detect, diagnose and compensate their own errors.