Mold costs depe…
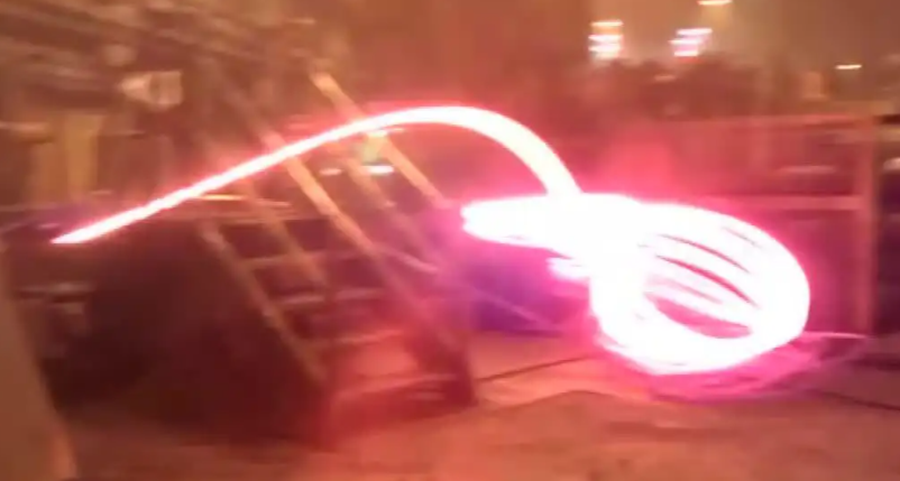
Common Steel Stacking Accidents in Steel Rolling and Treatment Measures
1、 Cause Analysis and Countermeasures of Rough and Medium Rolling Area Accidents
1. Steel stacking between racks after the rolled piece is bitten
Failure cause:
(1) The rolling speed and roll diameter are set incorrectly;
(2) The tension setting after roll (groove) change is too small;
(3) The steel temperature fluctuates too much;
(4) The roll breaks suddenly;
(5) The motor of a rolling mill suddenly speeds up or slows down due to the electric control system.
Treatment measures:
(1) Accurately set the rolling speed, roll diameter and tension;
(2) Hold the temperature and wait for rolling, and notify the flame adjuster of the heating furnace;
(3) Replace the broken roll;
(4) Check the electrical system.
2. Steel stacking at the head of rolled piece when the rack is biting
Failure cause:
(1) The rolled piece size does not meet the requirements;
(2) Foreign matters or slipping in the rolling groove;
(3) The guide is poorly installed, severely worn, or the guide is sandwiched with iron oxide scale and other foreign matters;
(4) “Split” of rolled piece caused by defects such as delamination, inclusion or metallurgical waste in the billet;
(5) The head of the rolled piece is bent due to different upper and lower roll diameters, uneven wear or asynchronous wear;
(6) Biting difficulty or head crack caused by too low head steel temperature;
(7) The rigidity of the rolling mill housing is not good, and there is deviation phenomenon in the rolling process;
(8) The billet is seriously out of square;
(9) After the rolled piece leaves the roughing mill stand, the head can not smoothly bite into the lower frame or the head can impact the guide, which is simply the head.
Treatment measures:
(1) Properly adjust the roll gap of the rolling mill;
(2) Check, clean or grind the rolling groove;
(3) Check, clean, adjust or replace the guide;
(4) Check the blank carefully;
(5) Check the clearance of transmission parts or replace the roll;
(6) Improve tapping conditions;
(7) Turn off the high-pressure water for descaling;
(8) Reinforce the mill stand;
(9) Install a sliding guide in front of 1 # rolling mill.
(10) Carefully check whether the inlet guide of the previous sorty is loose. The loose guide makes the rolled piece bite into the box shaped hole and receive the pressure from the inlet guide, so that the lower part of the rolled piece is under greater pressure, which leads to the extension of the lower part and causes the head warping. Finally, it fails to bite into the rolling mill smoothly and pile up steel.
3. Steel stacking caused by rolled piece stuck in the rack
Failure cause:
(1) Motor overload trip due to too low steel temperature or too high rolling speed;
(2) Emergency shutdown in case of equipment or safety accident.
Treatment measures:
(1) It shall be analyzed and handled according to specific conditions.
2、 Cause Analysis and Countermeasures of Pre finishing Rolling Area Accidents
1. Steel stacking between racks
Failure cause:
(1) The roll diameter and roll gap are set incorrectly;
(2) The guide is not installed accurately, and the guide is blocked or washed off;
(3) The tension of roughing and intermediate rolling is too large, and the rolled piece is “flapping” during pre finishing rolling;
(4) Bearing burning of rolling mill or roll box causes material type change of each frame;
(5) The self-locking performance of the screwdown device is poor, and the shape changes due to vibration during rolling.
Treatment measures:
(1) Reset roll diameter and roll gap;
(2) Check, replace and carefully adjust the centering guide;
(3) Control the incoming material size;
(4) Relieve tension;
(5) Electrical personnel or mechanical personnel shall inspect, repair or replace the equipment.
2. Automatic stop of pre finishing mill
Failure cause:
(1) Lubrication system failure;
(2) The motor trips.
Treatment measures:
(1) Check the lubrication system;
(2) Electrical inspection.
3、 Cause Analysis and Countermeasures of Accidents in Finishing Rolling Area
1. Steel stacking in scrap box after finishing rolling
Failure cause:
(1) There are remains in the guide groove after finishing rolling;
(2) Speed mismatch between finishing mill and double module mill;
(3) Guide at the inlet of finishing mill end stand;
(4) The water-cooled guide groove is seriously worn;
(5) The adjustment of a water tank or a water valve behind the finishing mill is too large, resulting in large water resistance or residual water in the water tank
(6) Problems in the installation or design of the spinning pipe;
(7) The input error of the roll diameter of the finishing mill leads to a large gap between the actual speed of the finishing mill and the feedback, and the speed of the finishing mill does not match the speed of the spinning machine.
Treatment measures:
(1) Check and clean the guide groove and guard;
(2) Correctly adjust the stacking and pulling relationship;
(3) The water valve shall be opened evenly and stably according to the vibration of the steel behind the waste box;
(4) Replace the spinning tube with stable design and mature process;
(5) Confirm the roll diameter of finishing mill.
2. Steel stacking between finishing rolling inner stands
Failure cause:
(1) The guide clamp is blocked, installed poorly, and the rolling guide is damaged;
(2) Roll matching error;
(3) The roll gap is set incorrectly;
(4) There are raw material broken inclusions;
(5) The front unit has tension, leaving tail in the finishing mill;
(6) Punch out the rolled piece.
Treatment measures:
(1) Check and replace the guide;
(2) Re configure roll and set roll gap;
(3) Lengthen the tail of the flying shear head, and the roughing and intermediate rolling workers carefully check whether the semi-finished materials at the 1 # flying shear have inclusions. If so, contact the 2 # platform to break the 2 # flying shear;
(4) Control the incoming material size.
3. Steel stacking at flying shear
Failure cause:
(1) The cutting head (tail) is too long and stuck in the guide groove;
(2) Shear blade and switch are worn, deformed or in incorrect position;
(3) No shearing, no head cutting or elbow cutting affects biting;
(4) Misoperation of flying shear in midway and out of control shearing.
Treatment measures:
(1) Reset the cutting head (tail) length and tension;
(2) Check the front and rear guide grooves of the shear blade and flying shear;
(3) Reset the leading factor of flying shear;
(4) Check photocell, thermal detection and power signal.
4. Steel stacking at looper
Failure cause:
(1) Looper action time is incorrect;
(2) Excessive sleeve quantity or incorrect speed setting;
(3) Looper lifting roller or roll guide plate are seriously worn;
(4) Looper scanner failure or front heat detection signal blocked;
(5) Too much cooling water or water mist affects the detection effect;
(6) Loops suddenly fall due to electrical or mechanical problems.
Treatment measures:
(1) Reset parameters;
(2) Replace relevant spare parts;
(3) Check the above related equipment and its action;
(4) Add baffles and fans at proper positions of thermal detection signals;
(5) Electrical personnel or mechanical personnel shall inspect, repair or replace the equipment.