Mold costs depe…
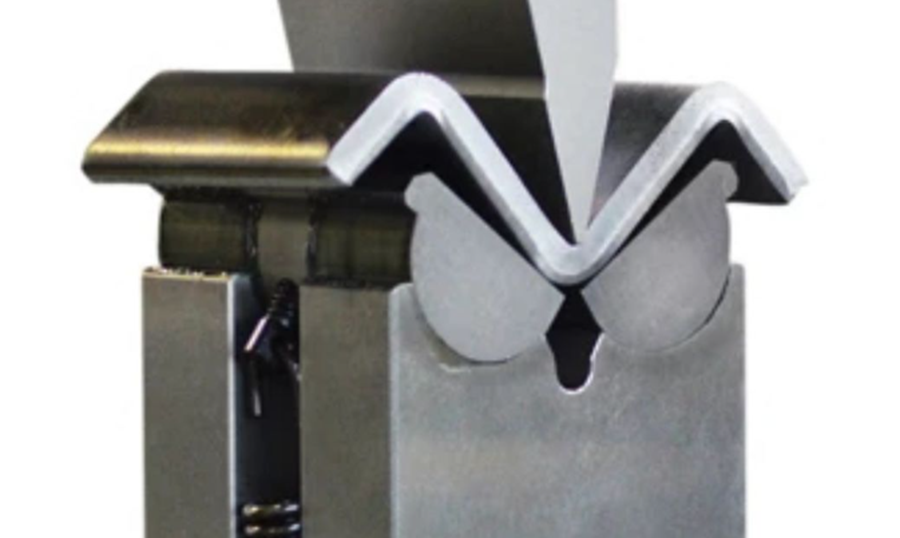
Common problems of sheet metal bending machine and bending die
FAQ of sheet metal bending machine and bending die
Those who are familiar with sheet metal processing engineering know that bending is the most difficult and technical project in sheet metal processing engineering.
(1) What is a sheet metal bend?
Sheet metal bending is the process of turning a flat sheet metal into a solid through a pressure device and a special mold.
Due to different materials, thicknesses, lengths and widths of plates and different shapes and angles to be formed, there are bending machines with different tonnage and size of pressure equipment, which are equipped with upper and lower dies of different heights, shapes and V-amplitude sizes, and special molds with special shapes.
(2) What are the types of bending?
Bending processing is divided into three categories: partial bending, close bending and embossing bending.
① Partial bending is the method of right angle and obtuse angle bending with upper die below 88 ° and lower die of V=12t (V represents slot width and t represents material thickness).
② Close bending is the bending method of right angle and obtuse angle on 90 °. V=6~12t is selected for the closely bent lower die.
③ Embossed bending is to use 90 ° upper die for right angle bending (It is a standard right angle bending) V=5~6t is selected as the lower die of the embossing bending.
(3) How to use the bending machine?
At present, there are many kinds of bending machines for sheet metal processing, which can be divided into mechanical (servo motor) and hydraulic type according to the rotation mode. According to the control system, it can be divided into simple manual bending machine, ordinary domestic digital positioning bending machine, and process control digital full function bending machine. It can be divided into 4-axis, 8-axis, 12 axis bending machines according to the action position.
① Before using the bending machine, check whether the power supply is connected, whether the air pressure is sufficient, whether the hydraulic pressure is sufficient, whether the machine is clean, and whether there are obstacles in the slideway. Follow up procedures can be carried out after confirmation.
② Turn on the power switch of the machine, start the oil pump to align the origin of L axis, D axis, CC axis and Z axis, and complete the starting process.
③ After the mold is installed and selected, place the gear switch of the machine at the cutting position. After the base, lower mold and upper mold are installed, place the switch of the machine at the inching or single action position. Use the foot lift switch to shake the lift handle or knob to combine the upper mold and lower mold, press and align the D-axis zero point, and lock the lower mold to complete the mold installation process.
④ Read the drawing, understand the bending sequence and bending size, and start to program the bending machine. There are two input methods for programming, one is angle input, the other is depth input. We usually use depth input method. First, enter the computer into the memory state, and input the bending dimension L, D, Z, speed, time, times and other values. Then check and confirm the program, and let the computer enter the running state after there is no error, and then use the waste trial folding to modify the program, so that the angle and size can be adjusted to the best state. After that, the products shall be trial folded, and the trial folded products can be mass-produced after being checked to be correct.
⑤ In order to improve the bending speed during the bending process, the gear switch can be in single action or linked action status, but for safety reasons, it is generally only used for single action. When bending long workpieces, the middle angle is often large. You can adjust the CC axis to change the middle angle to be consistent with the left and right angles. During the bending process, attention should also be paid to the central bending principle, which is an important prerequisite to ensure the bending processing accuracy. It is not allowed to bend at one end of both ends of the bending machine. Such an angle is not only bad, but also can damage the machine.
⑥ It is not allowed to turn off the power supply during a short break, just turn off the oil pump, so as to save the electricity cost, avoid the work of re starting the original point at work, save time and improve the efficiency.
⑦ When the product is finished or the machine needs to be shut down after work, first put the lower mold to the lowest position, then turn off the oil pump, and then turn off the power supply. If this batch of products has been completed, the mold must also be removed, put back on the mold rack, and reset to the operation panel.
⑧ It is strictly prohibited to operate the bending machine against rules, so as to avoid unnecessary injury to human body and equipment mold. At ordinary times, pay attention to the cleaning and maintenance of the machine, and develop a good habit of caring for equipment and molds.
(4) How do I use a bending die?
The bending die includes L type, R type, U type and Z type. The upper die mainly has different angles of 90 °, 88 °, 45 °, 30 °, 20 ° and 15 °. The lower die has 4~18V double grooves and single grooves with different groove widths, as well as R lower die, acute angle lower die, flattening die, etc. The upper and lower formworks are divided into sections and the whole: the upper formwork sections are generally 300mm, 200mm, 100mm, 100mm, 50mm, 40mm, 20mm, 15mm and 10mm, and the whole formwork is 835mm. The lower formwork is generally divided into 400mm, 200mm, 100mm, 50mm, 40mm, 20mm, 15mm and 10mm, and the overall formwork is 835mm.
① The bending die is made of high-quality steel by special heat treatment. It has the characteristics of high hardness, not easy to wear and bear large pressure. However, each set of die has its own limit pressure: t/m. Therefore, the length of the die should be correctly selected when using the die, that is, how much pressure should be added per meter, and the pressure should not exceed the pressure marked on the die.
② In order not to damage the mold, we specified that the upper and lower molds with a length of more than 300mm must be used to align the origin The upper mold and lower mold with the same height can be used only after the origin is aligned. It is strictly prohibited to use the split die to align the origin, and the origin must be aligned according to the pressure of the origin inside the AMADA machine.
③ When using molds, because the height of various molds is different, only molds with the same height can be used when selecting molds on one machine, and molds with different heights cannot be used.
④ When using the mold, the appropriate upper and lower molds should be selected according to the material hardness, thickness and length of the metal sheet. Generally, the lower mold should be used according to the standard of 5~6T. The length should be longer than the plate. When the material is harder and the thickness is greater, the lower mold with a wider groove should be used.
⑤ When bending acute angle or dead angle, it shall be selected at 30 degrees, and the acute angle shall be bent first and then the dead edge shall be pressed. When bending R angle, R upper mold and R lower mold shall be selected.
⑥ When bending long workpieces, it is better not to use segmented dies to reduce tool contact indentation, and it is better to use single groove ones, because the outer angle R of V groove of the lower die with single groove is large, it is not easy to produce bending indentation.
⑦ When selecting the upper die, we should know the parameters of all dies and decide which upper die to use according to the shape of the product to be formed.
⑧ When bending products with extremely hard hardness or too thick sheet, it is not allowed to use the mold to bend steel bars or other cylindrical products.
⑨ When using the mold, you should have a clear mind. After the machine has aligned the original point, you should lock the upper and lower molds, and do not let the mold fall down to hurt people or the mold. During the operation, you should pay attention to pressurizing. Do not add too much pressure at a time, and pay attention to the changes in the data displayed on the screen.
⑩ After using the mould, put it back on the mould frame in time and place it according to the marks. Clean the dust on the mould frequently and coat it with anti rust oil to avoid rust and reduce the precision of the mould.