Mold costs depe…
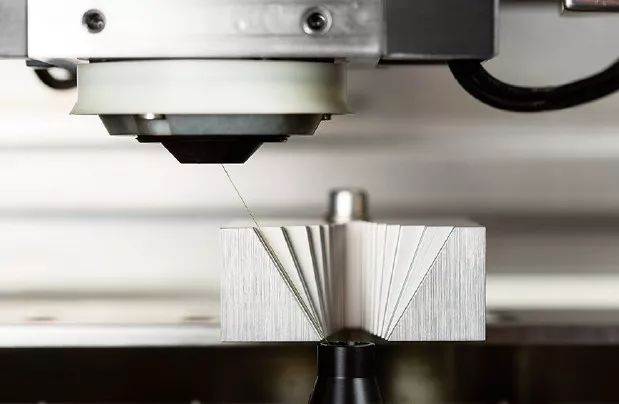
Common Faults and Treatment Methods in Slow Wire Walking Machining
How to achieve no trace at the feed?
(1) Arc in and arc out for profile
(2) Inner bore
1) It can feed from the sharp corner, and the originally closed hole can be changed into an open one
2) Each tool feed line shall be set at different positions, and over cutting shall not be set as far as possible
How to make the corner (clear the corner)? What are the methods?
There are two methods for corner cleaning:
1) Graphic corner cleaning
Graphic corner cleaning is to process the graphics in advance and draw clear corners.
2) Angle clearance of compensation amount
Compensation angle clearing is to pour a small R angle at the concave sharp corner, which is about 0.09mm (0.25mm line). In this way, when wire cutting, because the R angle is too small, it will cause over cutting, which can achieve the purpose of angle clearing.
How to prevent deformation?
(1) To prevent deformation, first of all, the material should have no internal stress, especially the internal stress of quenched material is large, so tempering and stress relief must be carried out.
(2) Prevent from wire cutting process.
1) Select proper cutting position and support position. If it is selected in the wrong place, the supporting part of the material will become fragile after roughening, resulting in deformation. It would be right to choose a place where the supporting part is more solid after roughening.
2) Make more supports. Especially when cutting punch, insert and other shapes, if large or long workpieces are encountered, several supports should be made instead of one, which can effectively prevent deformation.
3) When cutting the shape, if the wire feed is deformed, the wire cutting through the hole will be greatly improved.
How to do chip free machining? What are the methods?
There are two ways of chip free machining:
1) Some wire cutting software has this function, which directly coils in the hole.
2) During programming, cut more knives and use correction to control. This method is flexible, because if the cutting speed is too slow or not ideal, you can change the correction amount at any time to correct.
How to ensure that the upper, middle and lower dimensions of the machined holes or profiles of high thickness materials are consistent?
High workpieces shall have the same upper, middle and lower dimensions:
1) Increase the threading speed and slightly increase the thread tension
2) When repairing the first knife (shaping knife), repair the first knife several times, that is, repair the first knife repeatedly (because this knife is mainly shaped, and the latter one is polished)
3) If it is convex or concave, most machine tools can be adjusted in the electrical parameters (generally the servo voltage SV)
4) If the cut is tapered (one end is larger and the other end is smaller or opposite), the taper compensation can be used for correction, that is, the cutting taper (generally 0.002mm) is added in the program
When cutting precision terminal die, what should be done to ensure accuracy and position?
When cutting precision molds, especially formworks, the overall roughening shall be carried out first, that is, all holes shall be cut without repair. Then carry out plane fine grinding, because the formwork surface will be slightly deformed during roughening, and finally all the formwork will be refined again.
What are the methods of wireless head processing? What should I do with the small punch?
1) When cutting the profile, after the cutter is repaired, plug the copper sheet around, and then drop the glue. Be careful not to drop too much. If too much will cause short circuit, finally cut the support part. This method is generally not recommended for workpieces that are too small or larger. Too small glue drops will short circuit, and too large workpieces will fall after cutting due to their own weight.
2) It is also called secondary clamping. For larger or batch ones, re clamp and cut the support part. For small batches of workpieces, the fixture holes can be cut, which will effectively improve the efficiency.
How to calculate the angle and what should be paid attention to when programming?
Common for male and female die: (one cutter compensation x2 – unilateral clearance)/(plate thickness – male die edge – female die edge) anti sine. It should be noted that in general, it is used to cut the inverted cone.
There are two forms of internal and external sharing:
1) Step ladder type (mostly used)
2) Angle control. This is similar to the male and female mold, but there is no straight body