Mold costs depe…
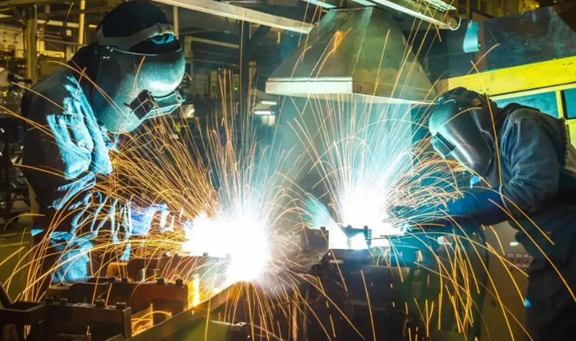
Application of welding boss in process welding spot
If no measures are taken after the door cover is welded, assembled and adjusted to be qualified, the flatness and clearance of the door cover will be greatly changed under the influence of external force and internal stress release during transportation and coating. This phenomenon is common in the automobile industry, especially the impact on flatness is obvious. In view of this problem, this paper introduces the concept of welding boss applied to the welding spot of the door cover, and proposes a new process method – using the welding boss to realize welding, so as to improve the rigidity of the door cover and reduce the surface deformation. This paper describes the classification, working principle and characteristics of the welding points of the door cover process, and focuses on the application of the boss welding process in Chery automobile.
The working principle of realizing the process welding point of the door cover
The process solder joint can be understood as a process that is not required from the perspective of product definition, but is adopted from the perspective of process and process manufacturing to improve the stability of process quality. The methods to realize the process welding points of the door cover include double-sided spot welding, single-sided single spot welding, single-sided double spot welding and single-sided double spot welding of the boss.
1. Spot welding on both sides
Double sided spot welding adopts the principle of resistance welding and uses fixed or movable welding equipment for welding. Since there is no special requirement for the strength of the process welding spot products, the effect of nugget and surface deformation can be reduced by reducing the pressure and current during double-sided spot welding, and a copper backing plate can be added outside the outer plate to reduce the deformation of the outer plate. The principle of ordinary pressure resistance spot welding is shown in Fig. 1, and the temperature curve of current line is shown in Fig. 2.
Double sided spot welding has the following advantages: low cost and convenient operation; Suitable for welding in areas with decorative parts on the outside. Its disadvantages are: long commissioning period, in order to reduce surface deformation, various parameters need to be constantly verified; The surface deformation is large and needs to be polished; The subsequent maintenance cost of surface parts is high and the quality is unstable.
2. Single side single point welding
The electrode is placed on the inner side of the plate, and the single-sided spot welding conforms to the basic principle of pressure resistance spot welding mentioned above, which is to form a welding spot by forming a current circuit and using resistance heat. Different from ordinary pressure resistance spot welding, the pressure electrode of single-sided spot welding uses the outer plate as the ground wire at the inner side to lead back the current. The working principle of single side spot welding is shown in Fig. 3.
The advantages of single-sided single point welding are that the cost is relatively low and it is mostly used for fixed equipment or robot welding; Suitable for welding in areas with decorative parts on the outside. Its disadvantages are: surface deformation still exists, and there is a certain amount of grinding; The subsequent maintenance cost of surface parts is high and the quality is unstable.
3. Single side double point welding
The single-sided double spot welding conforms to the basic principle of the above-mentioned double-sided spot welding. Unlike the ordinary pressure resistance spot welding, the two electrodes are placed inside the door cover. Therefore, the nugget of the single-sided spot welding is eccentric relative to the nugget formed by the ordinary pressure resistance spot welding, that is, most of its nuggets are on the side of the weldment in contact with the pressure electrode, which is helpful to improve the surface quality of the part. Its working principle is shown in Fig. 4.
On the door cover parts with strict appearance requirements, the application of single-sided two-point welding can effectively improve the rigidity of the door cover and reduce the surface deformation. As shown in Fig. 5, this process is adopted by Chery airyzer 7 and airy 5. The single-sided two-point welding process uses two cylinders to push the electrode placed on the inner plate side of the door, and the insulating chuck in contact with the outer plate forms a force, so as to ensure that the pressure meets the welding requirements, and then conduct current welding to form a nugget. Even where the visible area is weak, the variation amount of the workpiece is acceptable.
Single side double spot welding has the following advantages: relatively low cost, mostly used for fixed equipment or robot welding; It is suitable for welding in areas with decorative parts on the outer surface. Its disadvantages are: the surface still has a certain degree of deformation and a certain amount of grinding; The subsequent maintenance cost of surface parts is high and the quality is unstable.
4. Single side double point welding of boss
Based on the above analysis, there is a pair of contradictions in further reducing the influence on the surface deformation. From the perspective of deformation, it is proved that the welding current and pressure should be reduced as much as possible. However, if the connection strength between the inner and outer plates of the door cover with large size change and angle needs to be increased, the nugget needs to be added.
By studying the welding principle and referring to the practice of a foreign enterprise, Chery company has developed a process method to realize welding by using the plate boss, which not only greatly improves the rigidity of the assembly, solves the subsequent deformation problem, but also greatly reduces the surface deformation of the outer plate. The specific method is to form a convex hull on the corresponding inner plate at the position to be welded (the mold shall avoid the convex hull when wrapping), and realize welding by using the principle that the resistance becomes larger when the contact surface of resistance welding is small, and the heat generated is relatively large. At this time, the nugget will be greatly biased toward the inner plate and the edge wrapping side, while the outer surface of the outer plate and the inner plate will produce a small nugget, so that the deformation of the outer plate is extremely slight. This method can effectively reduce the external surface deformation caused by single side spot welding. The principle of single-sided two-point welding of boss is shown in Fig. 6.
Single side double spot welding of boss has the following advantages: relatively low cost, multi-purpose fixed equipment or robot welding; Slight surface deformation and relatively stable quality; The welding efficiency is high, and the welding work of two welds can be completed at one time. The disadvantage is that there is a certain amount of grinding from time to time.
Physical comparison after welding boss process
After the manual verification method was confirmed to be effective, the welding boss process was applied to the T15 model newly developed by Chery. Compare and analyze the physical quality before and after the welding boss is added, and compare and analyze the deformation amount after the process welding and the general assembly without treatment. The analysis data are summarized in Fig. 7, FIG. 8, FIG. 9 and FIG. 10. Through verification, although there is still some grinding amount from time to time, it has made great progress compared with the previous process welding.
epilogue
Since the connection performance of the folding adhesive and vibration isolation adhesive of the inner and outer plates has not occurred before the body enters the coating heating, the clamping force of the inner and outer plates after pressing by the pressing mold is not enough to overcome the external impact, the internal force of the plate and the heating deformation of the coating. With the increasingly high requirements on the quality of the car body, the necessity of corresponding process treatment in the welding assembly is also increasingly prominent. Due to the pressure of cost, many enterprises have not adopted high-frequency curing at present. In contrast, the single-sided double spot welding process using plate bosses has certain economy and is very worthy of promotion and application. For the vehicle with low rigidity designed for the junction, it is also a work to determine whether it is necessary to use the single side double spot welding and high-frequency curing of the boss at the same time during the trial production and verification of the early products and processes.