Mold costs depe…
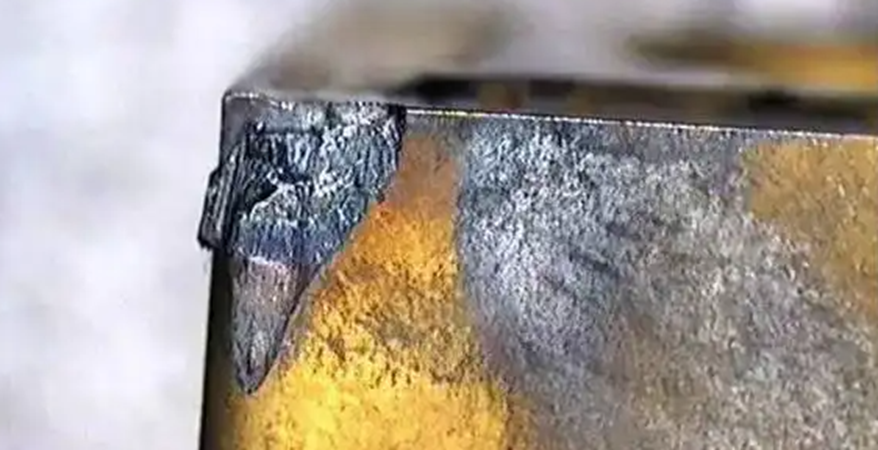
Analysis and Countermeasure of Tool Failure Mode
Performance of tool breakage
1) Slight chipping of cutting edge
When the structure, hardness and allowance of the workpiece material are uneven, and the front angle is too large, which leads to the low strength of the cutting edge, the insufficient rigidity of the process system generates vibration, or intermittent cutting, and the grinding quality is poor, the cutting edge is prone to micro collapse, that is, there is a small collapse, notch or peeling in the edge area. In this case, the tool will lose some of its cutting ability, but it can continue to work. During continuous cutting, the damaged part of the edge area may expand rapidly, leading to greater damage.
2) Chipping of cutting edge or tip
This kind of damage often occurs under worse cutting conditions than the micro collapse of cutting edge, or it is the further development of micro collapse. The size and scope of chipping are larger than that of micro chipping, which makes the tool completely lose its cutting ability and have to stop working. The condition that the blade tip breaks is often called tip drop.
3) Broken blade or tool
When the cutting conditions are extremely bad, the cutting amount is too large, there is an impact load, and there are microcracks in the blade or tool material, the blade or tool may be broken due to welding, grinding, and other factors such as careless operation. After this kind of damage occurs, the tool cannot be used any longer, so it is scrapped.
4) Blade surface peeling
For materials with high brittleness, such as cemented carbide, ceramics, PCBN, etc. with high TiC content, due to defects or potential cracks in the surface structure, or residual stress in the surface due to welding and grinding, surface peeling is easy to occur when the cutting process is not stable enough or the tool surface is subject to alternating contact stress. Spalling may occur on the front knife surface, and the knife may occur on the rear knife surface. The flakes are in the form of sheets, and the peeling area is large. The coated tool is likely to peel off. The blade can still work after slight peeling, and will lose cutting ability after severe peeling.
5) Plastic deformation of cutting position
Plastic deformation may occur at the cutting position of tool steel and high-speed steel due to their small strength and low hardness. When cemented carbide works directly under high temperature and triaxial compressive stress, it will also produce plastic flow in the surface layer, and even cause the plastic deformation surface of the cutting edge or tool tip to collapse. Collapse generally occurs in the case of large cutting amount and hard material processing. The elastic modulus of TiC based cemented carbides is smaller than that of WC based cemented carbides, so the plastic deformation resistance of TiC based cemented carbides is accelerated, or the former fails rapidly. PCD and PCBN are basically free of plastic deformation.
6) Hot cracking of blade
When the tool bears alternating mechanical load and thermal load, the cutting surface will inevitably generate alternating thermal stress due to repeated thermal expansion and contraction, which will lead to fatigue and cracking of the blade. For example, when the carbide milling cutter is used for high-speed milling, the cutter teeth are constantly subjected to periodic impact and alternating thermal stress, and comb cracks are generated on the front face of the cutter. Although some tools do not have obvious alternating load and stress, thermal stress will also be generated due to the inconsistent temperature of the surface layer and the inner layer. In addition, there are inevitably defects in the tool material, so the blade may also have cracks. After the crack is formed, the tool can sometimes continue to work for a period of time. Sometimes, the crack rapidly expands, causing the blade to break or the tool face to peel off seriously.