Mold costs depe…
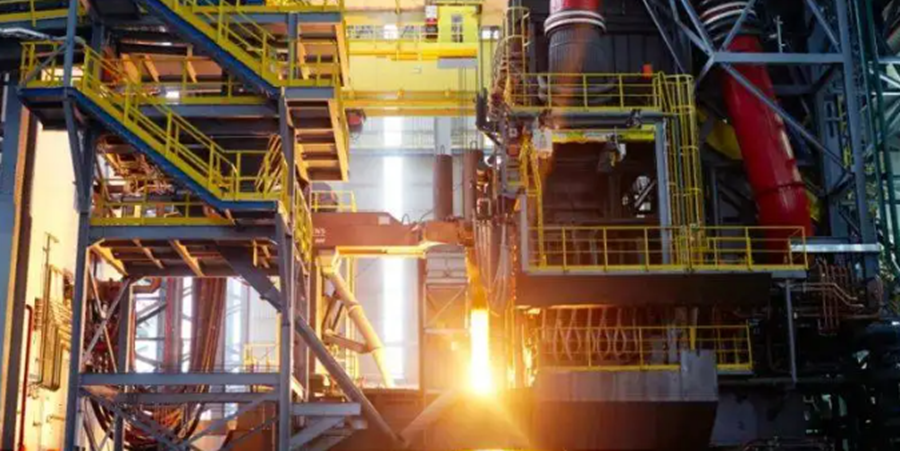
Advantages and disadvantages of induction furnace steelmaking
In the past 30 years, the application of induction furnace in the casting steel industry has developed rapidly, of course, because it has many advantages, but on the other hand, it also has many disadvantages. When selecting it as smelting equipment, we must conduct comprehensive analysis and research, strive to develop its strengths and avoid its weaknesses, and must not join in the excitement and catch up with the trend. After the equipment is selected, we should have a comprehensive understanding of its characteristics, and strive to continuously improve the quality of casting products on the basis of energy conservation and emission reduction.
The following is a brief analysis of the advantages and disadvantages of induction furnace smelting of cast steel for reference.
1. Advantages
In terms of cast steel smelting, compared with electric arc furnace smelting, crucible induction furnace has many advantages, such as:
(1) Although induction furnace is also a high power consumer, its interference to the power grid is much smaller than that of electric arc furnace;
(2) In terms of the impact on the environment, the smelting process has low noise, less smoke, gas, dust and waste slag;
(3) In terms of resource utilization, charging materials (including various alloy elements added) have less burning loss and higher yield. The amount of slagging material is much smaller, and no electrode is used;
(4) In terms of metallurgical function, due to the electromagnetic stirring effect, the composition of molten steel is relatively uniform, the temperature of molten steel is relatively uniform, and the temperature control is relatively convenient. There is no carbon increase problem caused by electrodes. Because there is no high temperature effect of electric arc, and there is no problem that nitrogen is easily absorbed by molten steel due to dissociation at high temperature;
(5) The investment in equipment is small, and the area occupied by the site is also small;
(6) It is easier to automate the job.
2. Shortcomings
Due to the above advantages, since the 1980s, the application of crucible induction furnace in steel casting has developed rapidly. However, the crucible induction furnace also has its unique disadvantages, which restricts its development‘ How to avoid weaknesses? ‘ It is a subject that process technicians must face. To avoid weaknesses, we should have a full understanding of these weaknesses.
(1) Problems in refractory lining
Refractory lining is an important part of the crucible induction furnace. Ensuring its normal operation is crucial to the reliability, economic benefits, safety of equipment operation and even the metallurgical quality of steel casting products.
The energy used for smelting in the crucible induction furnace is transmitted to the metal in the furnace through the refractory lining by the magnetic flux generated by the induction coil. As the thickness of refractory lining increases, the magnetic flux leakage increases, and the output power, power factor and electrical efficiency of the inductor decrease. In order to minimize the compensation of reactive power by balance capacitor and improve electrical efficiency, it is necessary to minimize the thickness of refractory lining. As a result, the thickness of the refractory lining of induction electric furnace is much smaller than that of any furnace type in various furnaces used for steelmaking, but its operating conditions are much stricter than those of other furnace types.
1) The inner surface of the furnace lining is in contact with molten steel, and the temperature is very high. The outer surface is connected with water-cooled induction coil. The temperature gradient in the thin furnace lining is very large.
2) The molten steel in the furnace is continuously stirred due to the electromagnetic effect, which enhances the flushing of the molten steel on the furnace lining and the corrosion of the suspended oxides on the furnace lining, and the stirring effect also increases the possibility of the molten steel absorbing gas.
3) If the compactness of the furnace lining is not enough or the sintering is not good, there are cracks where molten steel seeps into the furnace lining during the furnace process. The molten steel will not solidify in the cracks because of its induction heating effect, but will continue to penetrate into the cracks until it contacts the coil, causing short circuit, and even causing major safety accidents.
Therefore, the performance, grain size distribution, lining construction and lining sintering of refractory materials for furnace lining must be strictly required without any carelessness.
(2) Problems in metallurgical function
The metallurgical function of crucible induction furnace smelting cast steel is much worse than that of electric arc furnace smelting. Therefore, it can only be used to smelt steel grades with general metallurgical quality requirements in the early stage to manufacture small steel castings. Since the 1980s, with the continuous improvement of equipment and refractory materials, mild oxidation boiling can be carried out in the smelting process to enhance its metallurgical function, and the scope of application has gradually expanded to high-quality low-alloy steel, high alloy steel, and even ultra-low carbon stainless steel and various high-temperature alloys. However, the low metallurgical function of induction furnace smelting cannot be ignored.
1) For induction furnace smelting, the slag is melted by the heat conducted by the molten steel. The temperature of the slag is lower than the temperature of the molten steel. As for electric arc furnace smelting, oxidation refining and diffusion deoxidation can not be carried out through various metallurgical reactions between the molten steel and slag.
2) For electric arc furnace smelting, the molten pool is of shallow basin type, and the diameter of slag line is about 4-5 times of the depth of the molten pool; In the crucible type induction furnace smelting, the molten pool is cylindrical, and the diameter of the molten pool is less than its depth. The ratio of the two is about 0.6~0.75. It can be seen that the interface between molten steel and slag in induction furnace smelting is much smaller than that in electric arc furnace smelting, so it is impossible to use the metallurgical reaction between molten steel and slag for smelting.
Therefore, when the steel casting enterprise adopts induction furnace smelting, the requirements for the furnace charge must be very strict: the chemical composition of various raw materials must be confirmed; The amount of charging materials shall be determined by calculation; Scrap steel and recycled materials must be dry, free of sediment and oil stain; The maximum size of charging materials shall not be greater than 1/2 of the size of the crucible cavity.