Mold costs depe…
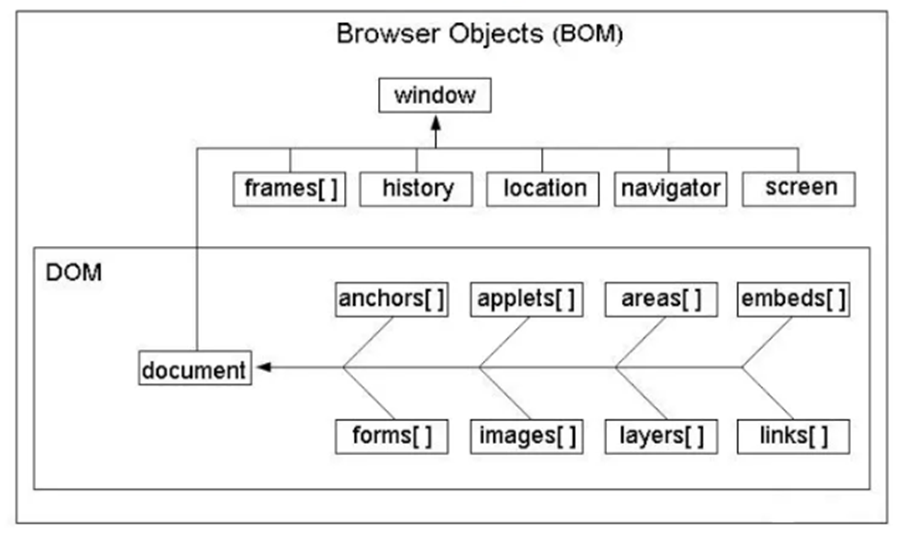
Advantages and disadvantages of BOM modularization
In today’s manufacturing enterprises, many enterprises appear that BOM management lags behind the market requirements for enterprise production efficiency in production management, which makes it necessary to improve the scientific nature of enterprise production management by improving the management mode of BOM to meet the future needs. Through the investigation of manufacturing enterprises, this paper collects the difficulties encountered by BOM in enterprise management at present, puts forward the favorable factors brought to enterprises by using BOM modular management, gives the measures that enterprises need to take in the process of implementing BOM modularization, as well as the principles and division methods of implementing BOM modularization, and demonstrates the risks that need to be avoided when implementing BOM modularization.
Current situation and problems of enterprise production management
1) In the production process, we often encounter the problem that the required parts cannot be supplied on time or the supply is insufficient. In a manufacturing enterprise, the purchase, inventory and production links of the enterprise can not be well coordinated, and the customer’s demand for products is constantly changing, so that the production plan has to change with the customer’s needs. A large number of product processing must be handled in the form of urgent orders, which increases the pressure on the purchasing department, and the supply of raw materials is often not timely, In particularly serious cases, the production line may even be shut down.
2) Manufacturing enterprises often encounter a serious backlog due to the incomplete production of parts, which leads to the unbalanced production schedule of manufacturing enterprises. The poor matching of production parts, coupled with the difficulties in production planning, make the backlog of spare parts serious.
3) The production cycle of the product is too long, and the labor productivity of the product is not ideal. Because the matching of product parts is not ideal, the production activities of products are not standardized, so that the labor productivity decreases, and the production cycle of products is extended.
4) The fund is seriously overstocked and the turnover time is long. In order to ensure that the production process can not stop running and production can not stop, in order to face urgent orders from customers, enterprises usually use the method of increasing inventory to solve the problem, which will cause excessive overstock of parts and finished products and increase the capital turnover time.
The role and significance of implementing BOM modularization
1) The implementation of BOM modularization in manufacturing enterprises can shorten the response cycle of enterprises to customers. After the enterprise realizes BOM modularization, it can form a ready-made modular design scheme according to the existing module composition, quickly form project implementation rules, greatly shorten the delivery lead time, and provide more active and effective measures for maintaining customer relations.
2) Save equipment needs and labor costs. For complex products made of many common parts and with multiple combinations, if an independent BOM is stored for each final product in the computer according to the needs of MRP, the file will be too large, which will cause difficulties due to high storage and maintenance costs, so the BOM has to be reconstructed to solve the problems faced through modular processing. Through BOM modular management, data can be more easily classified, greatly saving equipment needs and labor costs.
3) It is conducive to production planning and prediction. Generally speaking, the whole system requires the final project to be predicted at the level of the master production plan. In order oriented manufacturing enterprises, products are determined, and the final project is the final product. When a product has multiple optional features, it is often impossible to predict and plan a large number of final products. One way to solve this problem is to use optional features instead of final products as the object of prediction and planning, so as to greatly reduce the number of projects predicted and planned. This requires the reconstruction of the BOM, and the BOM modularization is used to divide the parts related to a specific optional feature into a group of modules and assign a material code. If an optional feature module is selected for the products to be sold, relevant parts can be planned according to the correct quantity. In this way, the prediction based on these modules is much more accurate than the direct prediction of the final product, which is more conducive to the implementation of the production plan.
4) It can better meet the requirements of customers, and at the same time, it makes the product upgrade and later maintenance more convenient. Modular products can better meet customer needs by integrating several interacting functional modules. This integration allows products to improve their market value by using more effective components or BOM modules. In addition, different modules can be replaced by customized and more optimized modules to improve product functions and optimize market demand.
5) It is conducive to improving the quality assurance system of final products. BOM modularization Before forming the final product, each module can be tested for quality parameters separately. The product strength, durability and other core data of each module can be tested separately, which will greatly improve the quality coefficient of the final product.
How to implement BOM modularization division
Product BOM module division is the process of dividing the total functional requirements of the product mastered through market research and demand forecasting into several functional units, and then determining the corresponding functional modules. The BOM module can be divided from any level to form the module of this level. However, from different angles of product performance, processing and management, there will be different requirements and different division methods. If the division is reasonable, the types of modules are less, and the generalization degree of modules is improved, the processing batch will increase, the manufacturing will be more convenient, and the production cost will also be reduced.
However, from the perspective of meeting various functional and performance requirements of products and improving system flexibility and product strain capacity, we prefer to divide modules into smaller and more types, so that the management of product manufacturing and assembly becomes complex and difficult. In the design process, we must start from the overall system and conduct a comprehensive analysis according to certain principles to make the determined module types and quantities more reasonable. Principles to follow when dividing modules:
1) Decomposition principle of functional unit. The division of functional units depends on the needs of users for product development, and thorough analysis of functions and structures is carried out with certain scientific methods and evaluation.
2) The principle of functional unit independence. The decomposed functional units shall be structurally independent as much as possible to facilitate collocation and form a variety of demand varieties.
3) The principle of component modularization. Components are relatively independent units formed through long-term experience accumulation in the process of product design and manufacturing. Taking components as module units, it is convenient to exchange modules and learn from previous design results. The modularization of components emphasizes the independence of functions.
4) Shorten the order cycle. The customized products of customers can be obtained through the integration of modular standard parts and customized components, which will allow the preparation of catalog list of standard components and centralize customized products on different components. Standard components can also be combined to form modular products. The same standard parts can be integrated in different ways to form different products to meet different customer needs.
Difficulties encountered in the implementation of BOM modularization
1) After the implementation of BOM modularization, the customer order is directly related to the manufacturing unit by the customer unit, so that the design awareness will be weakened. After the implementation of BOM modularization, a large number of parts in the enterprise will be produced in a standardized way. Different manufactured products have different requirements on the strength and tolerance of parts, which will affect the quality and performance of finished products.
2) The implementation of BOM modularization will greatly affect the production ideology of the current manufacturing industry. The general environment of manufacturing industry is a personalized environment. The purpose of production is to better meet the needs of different consumers. The modularization of BOM will make the personalized environment form a sense of universality. On the one hand, it hinders the enthusiasm of the design department, on the other hand, it also ignores the characteristics of the product that needs to meet the market mechanism.
3) Obstacles from the design engineer. Most of the engineers in charge of design are used to the traditional BOM design management process, lacking the standardized idea and design method of BOM modularization. When enterprises use the BOM modular management mode, designers will have resistance to the standardization of design, forcing enterprises to carry out design standardization training for designers in all aspects.
4) The implementation of BOM modularization will bring great pressure to the purchase department of purchased parts. Because many manufacturing enterprises now adopt the global procurement of parts and components, and many parts of products are purchased externally, the standardization of BOM within the enterprise causes the enterprise to standardize the requirements for purchased parts, which makes the purchased parts adopt uniform standards in terms of installation point, part performance, aperture size, etc., thus exerting great pressure on the suppliers of parts and components, It is required that the spare parts provided by suppliers must be implemented according to unified standards, which makes the design and production links of suppliers need to be completely reformed.
5) Since a large number of parts and components of various modeling enterprises need to be self-made, and the manufacturing drawings of various manufacturing enterprises and the molds of self-made parts are ready-made and traditional, once the BOM modularization is implemented, the standardized system transformation is required for each part, and the molds, processing processes, and jigs and measuring tools required for manufacturing of all parts must be eliminated. All design schemes, manufacturing processes and molds must be rebuilt, which will increase the working pressure of the self-made parts production department and bring new research and development costs.
6) The implementation of BOM modularization will make the design mode of products more mechanical. In the process of designing various modules of products, more consideration will be given to the universality and replicability of modules, but this design mode will greatly reduce the degree of personalization of the final products, and the phenomenon of product homogeneity will become more prominent.
Measures to be taken to implement BOM modularization
1) Strengthen the implementation of enterprise culture and train technicians, especially designers, related to BOM modularization. Among the designers in manufacturing enterprises today, the design standards are not uniform and have not reached the level of standardization. Some front-line design engineers refer to the enterprise standards, some front-line design engineers refer to international standards for research and development, and even some design engineers refer to self-conscious standards for design work. Therefore, enterprises must unify standards, increase the support for BOM modularization, and achieve standardization and unification in ideology.
2) The purchasing department has strengthened the BOM standardization management and supervision of suppliers of purchased parts. Most of the outsourcing parts of enterprises have mature process technology, process flow, process manufacturing equipment and tools, and the parts of different products have different installation points and hole sizes. Therefore, most enterprises have not implemented BOM standardization management. Once the enterprises implement BOM modularization, the design process will overturn the traditional model and carry out unified management, and the outsourcing parts bear the brunt and need to be changed. As a result, suppliers of purchased parts need to re invest in one-time product design. Therefore, it is necessary to coordinate the conflicts between enterprises and suppliers.
3) Increase the investment of the production department of the enterprise in the replacement of related equipment with BOM modularization at one time. The enterprise needs to implement BOM modularization, which means that a large number of design schemes used in the past will change. The molds, processing techniques, and jigs and measuring tools required for manufacturing of all parts must be eliminated, which makes the enterprise have to spend a lot of money to invest in related equipment.
4) Strengthen the management of the enterprise’s internal environment and suppliers, and protect the enterprise’s intellectual property rights. When enterprises implement BOM modularization, it is easier for external enterprises to imitate standardized parts. If the protection of enterprise intellectual property is not strengthened, a large number of counterfeit products will flow into the market.
Support needed to implement BOM modularization
1) Leadership support
When implementing the BOM modular management process, there will be many obstacles, especially the resistance of customary practices. At this time, no matter how good the system is, it is difficult to adhere to it without the support and strong implementation of leaders. In order to win the support of the leaders in charge, we must make great efforts to reconstruct the operation process before and after, and timely analyze and report the advantages of the BOM modular management process to the leaders, so as to gain the leaders’ attention to the project development.
2) System guarantee
The system is to ensure the smooth implementation of BOM modular projects. Through the system, the division of labor, responsibilities and reward and punishment standards shall be clarified to ensure fair, open and rule-based management and effectively ensure the continuity of the effect after the implementation of the project.
3) Strengthen training and assessment
Training is very important for the smooth implementation and promotion of process reengineering. On the one hand, use the training opportunities of various colleges and universities to send core personnel of relevant departments to learn and further study the professional knowledge of industrial engineering, especially BOM modularization; On the other hand, through the assessment mechanism, relevant personnel are encouraged to learn while doing and receive on-the-job training. With the intensification of competition and the development of the company’s product category and brand strategy, BOM management will become increasingly complex. We believe that as long as the ideas and methods of process reengineering are flexibly applied, the data management of materials will be done well with high efficiency, low cost and high quality, and the BOM modular management will play an important role.
Concluding remarks
Through field research and investigation of manufacturing enterprises, relevant data and documents are obtained. At present, some manufacturing enterprises (such as those in the automobile industry) have successfully carried out the BOM modularization program, and achieved good response and expected results. However, according to different industries, a large number of manufacturing enterprises are studying the BOM modular management mode suitable for their own enterprises. BOM modularization will become an important area for enterprises to think about and explore in industrial engineering management, and this research will play a positive role in improving production efficiency and optimizing product marketization.