Mold costs depe…
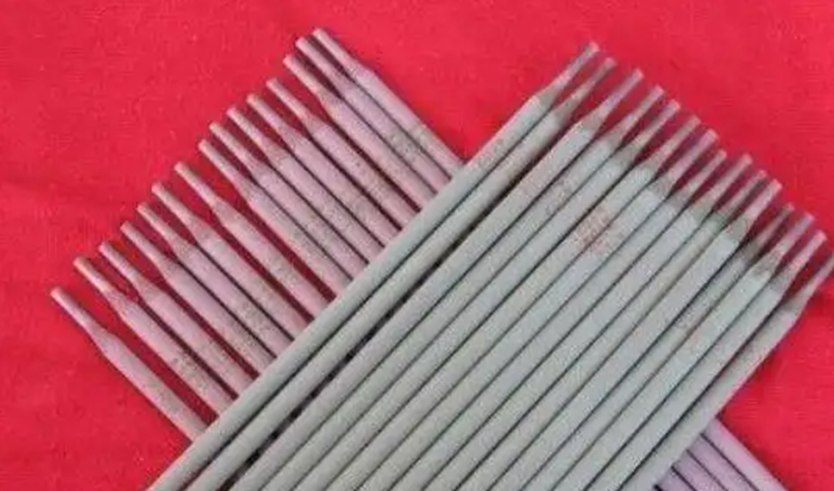
A Simple Method for Quickly Distinguishing between Qualified and Unqualified Electrodes
1. A Simple Method to Check the Quality of Welding Rods
(1) The inspection of actual welds is to inspect the quality of welding rods through the actual welding seams. For high-quality welding rods, the arc burning is extremely stable during welding, the welding core and coating are evenly melted, with little splash, the weld is well formed and easy to deslagging.
(2) Strength inspection of coating: lift the welding rod one meter high and drop it freely on the smooth thick steel plate. If the coating does not fall off, it will prove that the coating strength meets the quality requirements.
(3) The appearance inspection shows that the coating surface shall be smooth and fine, free of pores and mechanical damage, the coating shall not be eccentric, and the welding core shall be free of corrosion.
(4) Physical and chemical inspection: when welding important weldments, the weld metal shall be subject to chemical analysis and mechanical property re inspection to inspect the quality of welding rods.
2. Methods for identifying deterioration of welding rods
⑴ Put several electrodes in the palm of your hand and roll them against each other. If they make a crisp metallic sound, they are dry electrodes. If they make a low rustling sound, they are damp electrodes.
(2) Short circuit the electrode in the welding circuit for several seconds. If there are granular spots on the coating surface, it is a damp electrode.
(3) There are often rust marks on the welding core of the damp electrode.
(4) For electrodes with thick coating, slowly bend to 120 degrees. If large pieces of coating fall off or the coating surface is free of cracks, they are all wet electrodes. After slightly bending, dry electrodes have a small brittle sound, continue to bend to 120 degrees, and small cracks appear on the side of the coating under tension.
(5) If the coating falls off in blocks or a large amount of water vapor is generated during welding, it means that the electrode is affected with moisture. If the coating falls off, the electrode should be scrapped. Although it is affected with moisture, it is not serious. The core of the general electrode can have slight rust spots after drying. The quality can be basically guaranteed during welding, but the low hydrogen electrode used for important projects cannot be used after rusting.