Mold costs depe…
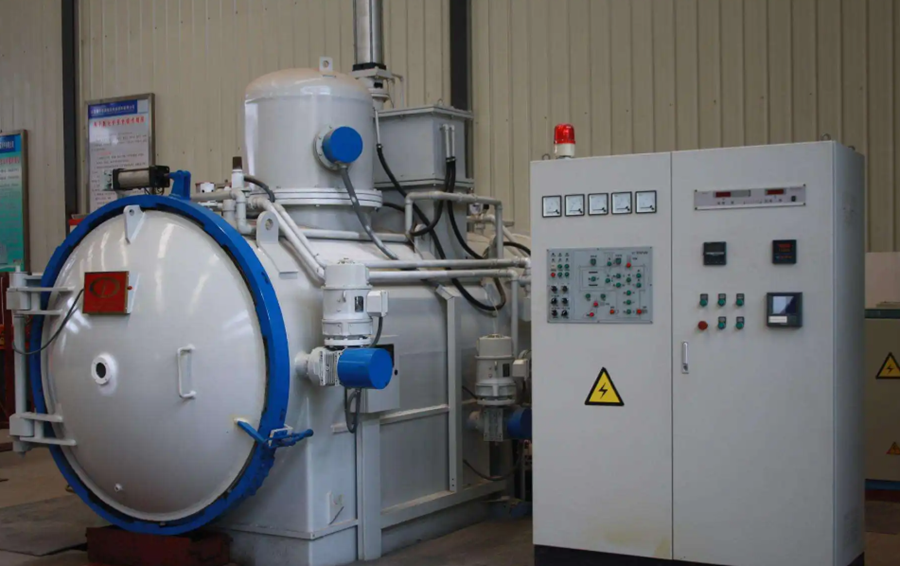
A Brief Analysis of V-Method Casting
1 Salt bath heat treatment
Company A is located in Sendai, Miyagi Prefecture, Japan, about 300 km from Tokyo. The company mainly produces a variety of mechanical blades, the longest of which is more than 5m. Blade materials mainly include high-speed steel, hard alloy and alloy tool steel. Heat treatment heating furnace includes salt bath furnace, vacuum furnace, box type multi-purpose furnace, large protective atmosphere furnace, large gas carburizing furnace, etc.
There are two sets of salt bath furnaces being produced on site: one is Cr12MoV steel tool quenching line, and the other is high-speed steel or base steel quenching line.
1) There are 3 sets of equipment on the production line of Cr12MoV steel tools (large and thin circular saw blades, etc.): ① The salt bath composition of the preheating furnace is BaC12+NaC1, and the indicated temperature is 810 ℃. ② The heating furnace is 100% BaC12, and the heating temperature is 1020-1030 ℃. ③ The cooling furnace is KNO3+NaNO2, and the indicated temperature is 220 ℃.
The salt bath furnace is semi buried and semi inserted, all of which are three-phase; The thermocouple is directly inserted in the furnace to measure temperature, and the temperature is controlled by a digital display recorder.
Cr12MoV steel circular saw blade shall be immediately flattened after isothermal quenching at 220 ℃, clamped and tempered in the basket, and the tempering shall be carried out in nitrate at the tempering temperature of 180~200 ℃.
2) There are 6 sets of equipment in the high-speed steel and base steel cutter salt bath production line: ① the drying resistance furnace, with the drying temperature of 500~600 ℃, is twice as high as that of heating. ② Preheating furnace, salt bath composition is BaC12+NaC1, indicating temperature 850 ℃; Single furnace and double plate preheating, with crane, but the on-site operation is manual. ③ In the heating furnace, the salt bath composition is 100% BaC12, and the quenching heating temperature of M2 steel is 1215 ~ 1220 ℃. There is no metallographic room in the workshop, only Rockwell hardness tester. ④ For the cooling furnace, the salt bath consists of BaC12, CaC12 and SrC12. It is said that the melting point is 430 ℃ and the service temperature is 480~550 ℃. The grading time is the same as the high temperature heating time. ⑤ Isothermal furnace, a mixed salt of KNO3 and NaNO2, with an isothermal temperature of 240~280 ℃ and an isothermal time of 0.5~2 h. After isothermal treatment, the slag shall be removed immediately and straightened at room temperature. The straightened product shall be clamped and tempered immediately. ⑥ The tempering furnace is 100% nitrate bath, and the tempering temperature is 550 ~ 580 ℃. Because the mechanical blade does not require too high hardness, the tempering temperature is relatively high.
The salt bath electrode is also semi buried and semi inserted, and only one side of the electrode is in the salt bath. The transformer is dry type salt furnace transformer, air-cooled. The salt bath temperature measurement does not use a radiation pyrometer or a radiation temperature sensor. Instead, it uses thermocouples for direct measurement, digital display for automatic recording, and alarm when the time comes. The thermocouple inserted in the furnace bath can directly measure temperature with high accuracy, and the product has high stability in heat treatment quality.
It is said that some Japanese high speed steel tools are tempered with SrC12+K2CO3 and KOH deoxidizer.
The method of checking quenching hardness and decarburization with Japanese heat treatment furnace front file can be used for reference. The hardness of the file used for quenching the first piece can judge the quenching quality. If the hardness is too high, it means that the quenching temperature is low, otherwise the temperature is high. If the hardness of the file is suitable (such as 62 ~ 63 HRC), the quenching is correct. Use a triangular file to file the surface of the quenched part. Depending on the depth of the file, estimate whether the salt bath is decarburized. The above must be completed by operators with rich on-site experience, which is difficult for ordinary people to implement.
2 Large controlled atmosphere heat treatment furnace
This furnace is a special furnace designed by the company itself. It is mainly used for the composite heat treatment of brazing → heating → quenching of long brazing blades. The total length of roller dynamic transmission is 18 m, the total power of the equipment is 460 kW, the maximum heating temperature is 1300 ℃, and the charging capacity is about 1.6 t. Holding at quenching temperature for 15-20 min is a rapid heating process. Microcomputer temperature control, automatic printing. Nitrogen filling protection in the furnace. Quenching cooling is also filled with liquid nitrogen. If it is a high-speed steel blade, it shall be cooled to 600 ℃ and then discharged for air cooling.
The tempering furnace is also a special furnace designed by ourselves. The tempering temperature is determined according to the blade material and the required hardness, and generally fluctuates between 460 ℃ and 600 ℃.
3 Box type multipurpose furnace
During the visit, the box type multipurpose furnace was working, and the product in the furnace was Cr12MoV steel circular saw blade or cutter, with a size of about φ 100~ φ 120 mm, thickness of 3~5 mm, heating temperature of 1020 ℃, quenching cooling medium of about 150 ℃ nitrate.
Tempering is carried out in the nitrate tank. It can be found from the site that nitrate is widely used in the Japanese tool industry.
4 Large well type carburizing furnace
The company has several large well type carburizing furnaces with a depth of 6.5 m, and the carburizing agent is methanol+acetone. This kind of furnace is mainly used for carburizing of machine tool guide rail. Section size of guide rail 60~80 mm × 80~100 mm, the length of guide rail varies from 4 to 6 m. The carburizing thickness is about 2 mm. After carburizing, it shall be cooled, quenched and tempered at low temperature, and the hardness shall be 56 ~ 62 HRC.
The company has a strong machine tool manufacturing capacity. Most of them are self-made. According to the characteristics of blade processing, the special machine is refined. Maybe it is one of the factors that make them prosperous and competitive for a hundred years.
5 High temperature press rolling inlay quenching furnace
Some rotary cutters and planer cutters are formed by inlaying. Namely, the blade steel and Q235 steel cutter body are heated to the forging temperature, then rolled to the specified size, air cooled to room temperature, and then boxed for annealing. This kind of cutting edge steel is basically low and medium alloy steel, with annealing temperature of 810-830 ℃, holding time of about 3 hours, furnace cooling to 550 ℃ and air cooling.
The quenching furnace does not have a protective atmosphere. Ordinary sealed box type furnace directly quenches water after heating and holding. The water temperature is strictly controlled. It is unknown whether there are additives in the water. As the 2011 “March 11” earthquake and tsunami caused a fatal wound to the company, the Japanese side was unhappy when asked about the heartache. The author estimated that no other agents would be added to the water, that is, a large flowing tank. Strictly controlling the outlet water temperature is the core technology. Energy conservation and environmental protection depends on your courage and technology.
6. Blade quenching technology
The measures to reduce and avoid the environmental pollution caused by heat treatment include prevention and treatment, and the Japanese have done so. The quenching oil of Cr12MoV steel big blade was on fire first, then smoking, and there was no smoke after a few seconds, and there was no oil smell in the workshop; The quenching water for low and medium alloy steel blades (production line for pressing and rolling blades) is certainly pollution-free; The waste water generated in the heat treatment workshop shall be treated and discharged up to the standard, the waste gas shall be treated by wet adsorption, and the waste residue shall be sent to the special government agency for treatment. It is people’s conscious action to do well in environmental governance.