Mold costs depe…
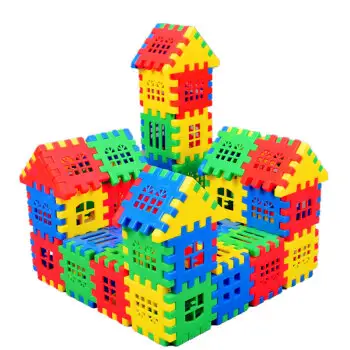
The most complete collection of 60 performance test methods for non-metallic materials in history
1. Density and relative density
Density refers to the mass contained in the unit volume of a substance. The unit is milligram / m3 (mg / m3) or kilogram / m3 (kg / m3) or gram / cm3 (g / cm3).
Relative density refers to the ratio of the density of a substance to the density of a reference substance under their respective specified conditions. The symbol is D, dimensionless. The general reference material is air or water: when air is used as the reference material, the density of dry air under the standard state (0 ℃ and 101.325kpa) is 1.293kg/m3 (or 1.293g / L).
Test methods: buoyancy method, water displacement method, Pycnometer method, gamma ball immersion method, saturated water method, surface coating method, etc
Test instrument:
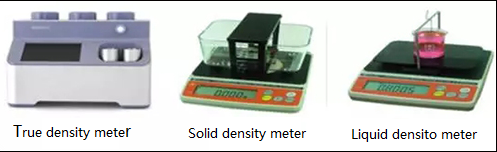
2. Freezing point
The freezing point is the temperature at which a crystalline substance solidifies. It is the temperature at which the vapor pressure of a liquid is equal to that of a solid. Different crystals have different freezing points. At a certain pressure, the freezing point of any crystal is the same as its melting point. Amorphous materials have no freezing point.
Test method: undercooling method
Test instrument:
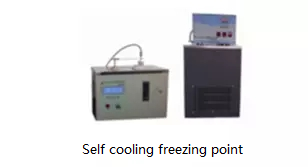
3. Melting point and melting range
The melting point is the temperature at which the solid and liquid of a pure substance are in equilibrium under a certain pressure. The melting point range refers to the temperature range measured by capillary method from the beginning of melting to the whole melting of the material.
Test method: capillary method
Test instrument:
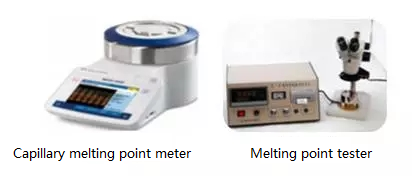
4. Crystal point
It refers to the phase change temperature of liquid from liquid to solid during cooling.
Test method: double casing method
Test instrument:
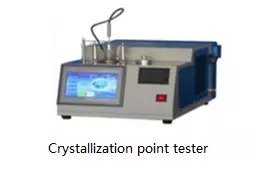
5. Pour point
One of the indicators indicating the properties of liquid petroleum products. It refers to the temperature at which the sample is cooled to stop flowing under standard conditions, that is, the lowest temperature at which the sample can be poured when cooled.
Test methods: inclined test tube method, rotating test method and automatic air pressure pulse test method
Test instrument:
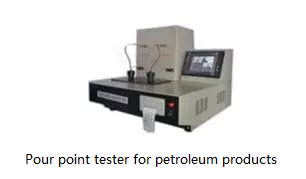
6. Boiling point
The temperature at which a liquid boils and becomes a gas when heated. Or the temperature at which the liquid and its vapor are in equilibrium. Generally speaking, the lower the boiling point, the greater the volatility.
Test method: constant method, micro method
Test instrument:
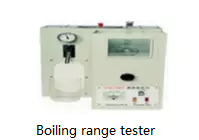
8. Vapor pressure
Vapor pressure is short for saturated vapor pressure. At a certain temperature, the liquid and its vapor reach equilibrium. At this time, the equilibrium pressure changes only due to the nature and temperature of the liquid, which is called the saturated vapor pressure of the liquid at this temperature.
Test methods: static method, dynamic method and saturated air flow method
Test instrument:
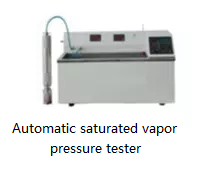
9. Refractive index
Refractive index is a physical quantity that represents the ratio of light speed in two different (isotropic) media. The speed of light varies with different media. When light enters another transparent medium with different density from one transparent medium, it changes in its direction due to the change of speed, so it is called refraction. The ratio of the sine of the incident angle of light to the sine of the refraction angle, or the ratio of the speed of light passing through a vacuum to that passing through a medium, is the refractive index.
Test method: solid angle measurement method; Liquid critical angle method; Gas interference method
Test instrument:
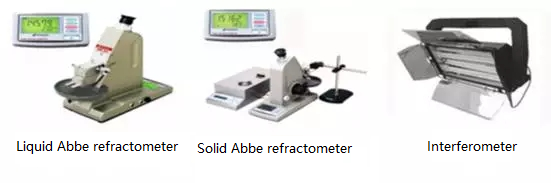
10. Flash point and ignition point
Flash point, also known as flash point, is one of the indicators indicating the properties of combustible liquids. It refers to the lowest temperature when the mixture of vapor pressure and air heated to the liquid surface of combustible liquid contacts with the flame to produce flash fire. Flash is usually a light blue spark, which goes out immediately and cannot continue to burn. Flashover is often the precursor of fire. There are open cup method and closed cup method to determine the flash point. Generally, the former is used to determine the high flash point liquid and the latter is used to determine the low flash point liquid.
Ignition point, also known as ignition point, is one of the indicators indicating the properties of combustible liquid. It refers to the lowest temperature at which the mixture of steam and air heated to the surface of combustible liquid can ignite immediately and continue to burn.
Test method: open flash point and closed flash point
Test instrument:
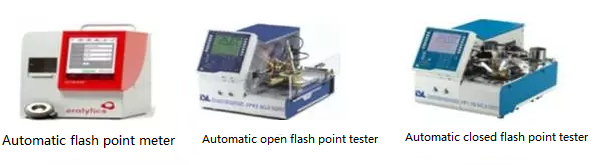
11. Spontaneousignition point
The lowest temperature at which combustible substances can cause ignition without contacting open fire is called the spontaneous combustion point. The lower the spontaneous combustion point, the greater the risk of ignition. The spontaneous combustion point of the same substance varies with pressure, concentration, heat dissipation and other conditions and test methods.
Test instrument:
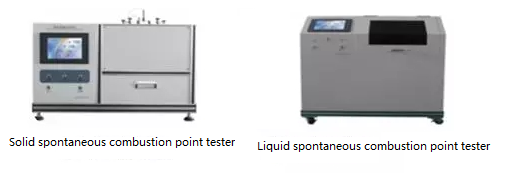
12. Explosive limits
When combustible gas, vapor of combustible liquid or dust of combustible solid are mixed with air or oxygen at a certain temperature and pressure to reach a certain concentration range, it will explode when encountering a fire source. This certain concentration range is called explosion limit or combustion limit. The explosion limit is usually expressed as the volume percentage of vapor in the mixture, that is% (vol); Dust is expressed in mg / m3 concentration. Flammable solvents have a certain explosion range. The wider the explosion range, the greater the risk.
Test instrument:
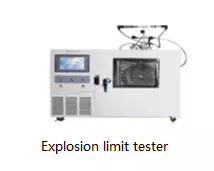
13. Viscosity
Viscosity is the internal friction resistance of fluid (liquid or gas) in the flow, which is determined by the type, temperature, concentration and other factors. It is generally the abbreviation of dynamic viscosity, and its unit is pa · s or millipa · s. Viscosity is divided into dynamic viscosity, kinematic viscosity and relative viscosity. The three are different and cannot be confused.
Test methods: capillary method, falling ball method, rotation method and vibration method
Test instrument:
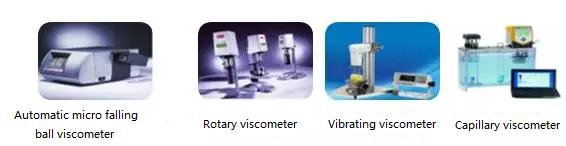
14. Mooney viscosity
Mooney viscosity, also known as rotational (Mooney) viscosity, is the value measured by Mooney viscometer, which can basically reflect the degree of polymerization and molecular weight of synthetic rubber. According to the provisions of GB 1232 standard, the rotational (Mooney) viscosity is represented by the symbol Z100 ℃ 1 + 4. Where Z – rotational viscosity value; 1 – preheating time: 1min; 4 – rotation time is 4min; 100 ℃ – the test temperature is 100 ℃. Traditionally, ml100 ℃ 1 + 4 is used to represent Mooney viscosity.
Test method: rotation method
Test instrument:
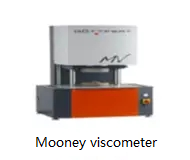
15. Solubility
At a certain temperature and pressure, the maximum amount of a substance dissolved in a certain amount of a given solvent is called solubility. The solubility of solid or liquid substances is generally expressed in grams of substances that can be dissolved in 100g solvent. The solubility of gas solute is usually expressed in milliliters of gas dissolved in each liter of solvent.
Test methods: commonly used chromatography, spectrophotometry, chemical titration, etc
Test instrument:
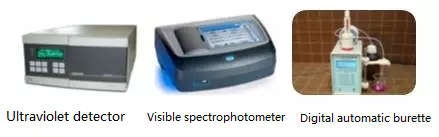
16. Surface tension
The attraction of the molecules inside the liquid makes the molecules on the surface under an inward force. This force makes the liquid minimize its surface area and form a force parallel to the surface, which is called surface tension. In other words, it is the mutual traction force per unit length between two adjacent parts of the liquid surface, which is a manifestation of molecular force. The unit of surface tension is n / m.
Test methods: maximum bubble pressure method, hanging ring method, hanging drop method (capillary phenomenon), rotating drop method, etc
Test instrument:
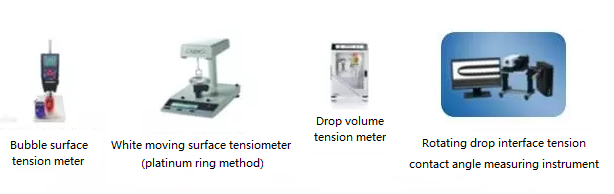
17. Specific heat capacity
The heat required to be absorbed when the temperature of each kilogram of material increases by 1K is called the specific heat capacity, and the unit is kJ / (kg · K). Under the condition of constant pressure, the heat absorbed when the temperature increases by 1K is called the specific heat capacity at constant pressure.
Test methods: mixing method (solid), electrothermal method (liquid), cooling method and comparison method
Test instrument:
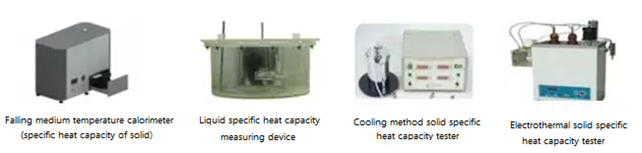
18. Thermal conductivity
In the past, thermal conductivity was called thermal conductivity or thermal conductivity, which reflects the thermal conductivity of materials. That is, two parallel planes with an area of 1cm2 and a distance of 1cm are taken in the interior of the object perpendicular to the heat conduction direction. If the temperature difference between the two planes is 1K, the heat transmitted from one plane to the other within 1s is specified as the thermal conductivity of the material, and its unit is w / (m · K).
Test methods: steady state method – heat flow meter method and heat protection plate method; Dynamic method – hot wire method, laser flash method
Test instrument:
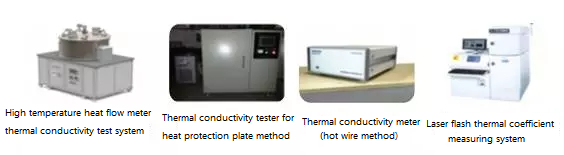
19. Water content
Water contained in a substance, but excluding crystalline water and connective water. It is usually expressed by the percentage of the original mass of the sample and the mass of the sample after water loss.
Test methods: physical method – weight loss method, distillation stratification method, gas chromatography, etc; Chemical method – Karl Fischer method, toluene method, etc
Test instrument:
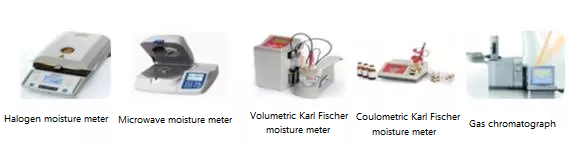
20. Ash (ash)
Ash, also known as burning residue, refers to the residue of oxides and salts formed by its mineral components after evaporation and burning, expressed in percent.
Test instrument:
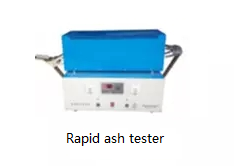
21. Needlepenetration
Penetration is expressed by the depth of the standard needle vertically penetrating the asphalt sample under certain load, time and temperature conditions, and the unit is 1 / 10mm. Unless otherwise specified, the combined weight of standard needle, needle connecting rod and additional weight is 100 ± 0.1g, the temperature is 25 ℃, and the time is 5S. The greater the penetration, the softer, that is, the smaller the consistency; On the contrary, it means that the harder it is, the greater the consistency.
Test method:—
Test instrument:
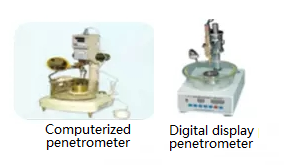
22. Hardness
Hardness is the resistance of a material to external forces such as embossing and scratches. According to different test methods, there are shore hardness, Brinell hardness, Rockwell hardness, Mohs hardness, Barcol hardness, vichers hardness, etc. The value of hardness is related to the type of hardness tester. Among the commonly used hardness testers, shore hardness tester has simple structure and is suitable for production inspection.
Test method: common methods include shore hardness, ball indentation hardness, Rockwell hardness, etc
Test instrument:
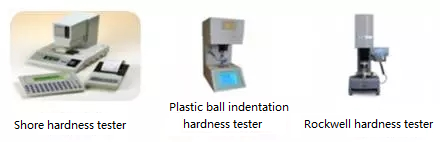
23. Anilinepoint (A.P.)
Aniline point is the lowest temperature when equal volume petroleum alkanes and aniline are dissolved with each other, which is used to express the content of alkane saturated hydrocarbons. The higher the aniline point is, the more alkanes are; The lower the aniline point, the more aromatic hydrocarbon content.
Test method: aniline point method
Test instrument:
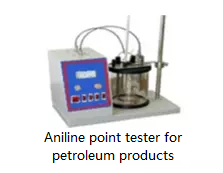
24. Volume resistivity
Also known as volume resistance and volume resistance coefficient, it is an important index to characterize the electrical properties of dielectric or insulating materials. Represents the resistance of 1cm3 dielectric to leakage current, in Ω· m or Ω· cm. The larger the volume resistivity, the better the insulation performance.
Test instrument:
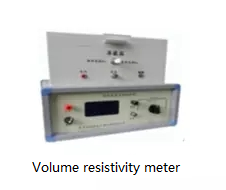
25. Acid value
Acid value is an indicator of organic matter. It is the milligram of potassium hydroxide (KOH) required to neutralize free acid in the nonvolatile matter of 1G organic matter, that is, mg KOH / g.
Test methods: photometric titrator method and potentiometric titrator method
Test instrument:
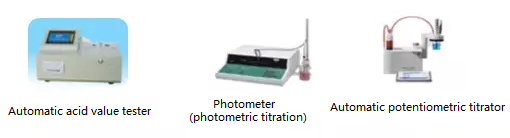
26. Hydroxyl value
Mg of potassium hydroxide (KOH) equivalent to hydroxyl in 1g sample, expressed in mg KOH / g.
Test instrument:
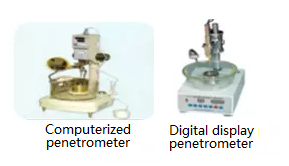
27. Iodine value
An indicator of the degree of unsaturation of organic matter. Is the mass percentage of iodine absorbed by 1g sample. The higher the degree of unsaturation, the greater the iodine value.
Test method: Wechsler method
Test instrument: Wechsler reagent
28. Epoxy value
Epoxy value refers to the equivalent number of epoxy group contained in 100g epoxy resin, that is, the greater the epoxy value, the smaller the molecular weight and the lower the viscosity.
Test method: hydrochloric acid acetone method
29. Epoxy equivalent
Epoxy equivalent represents the molecular weight of the resin corresponding to each epoxy group.
Test methods: hydrochloric acid acetone method, hydrogen bromide glacial acetic acid method and perchloric acid method
Test instrument:
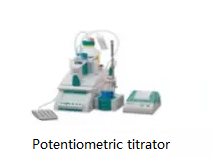
30. HLB value
HLB is the abbreviation of hydrophile lipophile balance, which is used to measure the relative strength of polar and nonpolar groups in surfactant molecules. If the polar group is stronger, its HLB value is larger and its hydrophilicity is stronger; The longer the nonpolar group, the smaller the HLB value and the worse the hydrophilicity.
Test methods: emulsification method, cloud point method, turbidity number method, critical micelle concentration method, partition coefficient method, solubility method, heat of hydration method, nuclear magnetic resonance method and gas chromatography
Test instrument:
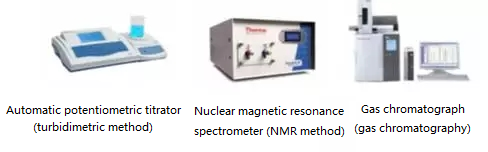
31. Critical micelle concentration
Critical micelle concentration, also known as critical micelle concentration, CMC for short. The concentration range in which the properties of emulsifier solution change is called the critical micelle concentration of emulsifier. When the emulsion system reaches critical micelle concentration, many emulsifier molecules aggregate to form micelles. The unit of CMC is mol / L.
Test methods: surface tension method, conductivity method, dye method, turbidity method, single point ultrafiltration method, fluorescent probe method
32. Degreebaum ′ e
The value given by the Baume meter, which adopts a special division method in the glass tube float meter, is called Baume degree and the symbol is ° B ′ E. Used to indirectly give the density of the liquid.
33. Solid content
Solid content, also known as nonvolatile content and total solid content (TS), refers to the ratio of the mass of the residue and the mass of the sample after heating at a certain temperature, expressed as a percentage.
Test methods: refractometer method, drying loss method and evaporation method
34. Relative humidity
A method of expressing humidity is the ratio of absolute humidity to saturated absolute humidity under the same conditions (same temperature and pressure), that is, the ratio of the mass of water vapor actually contained in air (or other gases) to the mass of saturated water vapor under the same conditions. Generally expressed as a percentage.
Test methods: dew point method, dry wet ball method, moisture absorption method, dynamic method (double pressure method, double temperature method, shunt method), static method (saturated salt method, sulfuric acid method)
35. Apparent density
It was once called bulk density, bulk density, pseudo density and apparent density, which represents the mass of material per unit volume (including voids).
36. Number average molecular weight
Polymers are composed of homologous mixtures with the same chemical composition but different degrees of polymerization, that is, they are composed of polymers with different molecular chain lengths. The average molecular weight is usually used to characterize the size of molecules. The statistical average according to the number of molecules is called number average molecular weight, and the symbol is (MN).
Test methods: freezing point drop method, boiling point rise method, vapor pressure drop method, osmotic pressure method and end group titration method
37. Degree of polymerization
The number of links constituting the polymer molecular chain is called the degree of polymerization, code named n or DP, which can be used as a measure of the molecular weight of the polymer.
Methods of test: end group titration, nuclear magnetic resonance, viscosity, gel chromatography, ion chromatography, light scattering, paper chromatography, thin layer chromatography, gel permeation chromatography.
38. Molecular weight distribution
Due to the different sizes of polymers, in addition to the statistical characteristics of molecular weight, they also have polydispersity, that is, molecular weight distribution. The same average molecular weight will have different molecular weight distribution and show different properties.
Test methods: sedimentation fractionation, ultracentrifugation sedimentation, gel permeation chromatography
39. Glass transition temperature
The approximate midpoint of the narrow temperature range for the transition of amorphous or semi crystalline polymers from viscous flow state or high elastic state to glass state (or the opposite transition) is called the glass transition temperature, which is usually expressed in TG and is an index of heat resistance.
Test methods: thermomechanical analysis (TMA), differential thermal analysis (DTA), differential scanning calorimetry (DSC), etc
40. Brittletemperature
A measure of the low-temperature performance of polymers. When the sample is impacted by a hammer with certain energy, the temperature when the cracking probability of the sample reaches 50% is called the embrittlement temperature, also known as the brittle fracture point.
Test method: impact method
41. Heat deflection temperature under load
A measure of polymer heat resistance is to immerse the polymer sample in a suitable heat transfer medium with constant temperature rise, and measure the temperature when the bending deformation of the sample reaches the specified value under the action of simply supported beam static bending load, which is the thermal deformation temperature, referred to as HDT.
Test method: load thermal deformation temperature test method
42. Minimum film forming temperature
The minimum temperature of the continuous emulsion film formed by the synthetic emulsion system is called the minimum film forming temperature (MFT).
43. Softening point
Heat the sample to a certain temperature in the form of softening at a specified rate, that is, heat the sample to a certain deformation point according to the specified load.
Test methods: global method, wire drawing method (glass), etc
44. Marten’s test
A method to evaluate the deformation trend of materials at high temperature. In the heating furnace, make the sample bear a certain bending stress and raise the temperature at a certain rate. The temperature at which the heating free end of the sample produces the specified deflection is called Martin temperature.
45. Vicat softening point test
A method to evaluate the deformation trend of thermoplastic at high temperature. Under the condition of constant temperature rise, place a flat top needle with specified load and cross-sectional area of 1mm2 on the sample. The temperature when the flat top needle enters the sample for 1mm is the measured Vicat softening temperature.
46. Melt index
Melt index, abbreviated as MI, is an index reflecting the melt flow characteristics and molecular weight of thermoplastic resin. Under certain temperature and load, the mass value of its melt passing through the standard capillary in 10 minutes is expressed in g / 10min.
47. Creep
When the stress remains constant, the phenomenon of deformation changing with time is called creep.
48. Shrinkage
It is defined as the percentage of the ratio of shrinkage to the size before shrinkage, and the shrinkage is the difference between the size before and after shrinkage.
49. Internal stress
In the absence of external force, the stress caused by defects, temperature changes, solvent action and other reasons in the adhesive layer (material).
Test method: solvent method – acetic acid immersion, methyl ethyl ketone + acetone immersion method; Polarized light method; Temperature sudden change method
50. Tensile strength
Tensile strength is the maximum tensile stress when the specimen is stretched to fracture. In the past, this common term was very inconsistent. It was called breaking force, breaking strength, tensile strength and tensile strength. According to GB 6039-85 standard, it is uniformly called tensile strength, and the unit is MPa.
51. Shear strength
Once known as shear strength, it refers to the maximum load that can bear parallel to the bonding area per unit bonding area. The commonly used unit is MPa.
52. Peel strength
Once known as peel strength, it refers to the maximum failure load that can be borne per unit width. It is a measure of line stress capacity, and the unit is kn / m.
53. Elongation
The increase in the length of the specimen under tension is expressed as a percentage of the original length.
54. Compatibility
The ability of mixing two or more substances without repulsion and separation.
Test methods: glass transition temperature method, infrared method, electron microscope method, cloud point method and reverse phase chromatography
55. Chemical resistance
Resistance to acids, alkalis, salts, solvents and other chemicals.
Test method: chemical resistance test (ESCR) method for environmental stress fragmentation
56. Water resistance
The ability of a material to maintain its physicochemical properties after the action of water or moisture.
Test methods: normal temperature immersion method, boiling water immersion method and accelerated water resistance method, etc
57. Flame resistance
The ability of a material to resist combustion when it comes into contact with a flame or to hinder continued combustion when it leaves the flame.
Test method: UL94 fire resistance grade test
58. Weatherability
The resistance of materials to exposure to sunlight, cold and hot weather, wind and rain and other climatic conditions.
Test method: natural climate, outdoor intensification and laboratory simulation
59. Aging
In the process of processing, storage and use, due to the action of external factors (heat, light, oxygen, water, ray, mechanical force and chemical medium, etc.), a series of physical or chemical changes occur, which makes the polymer materials cross-linked and brittle, cracked and sticky, discolored and cracked, rough and foamed, surface powdered, layered peeling, performance gradually deteriorated, so that they lose their mechanical properties and can not be used. This change phenomenon is called aging.
Test methods: artificial accelerated aging test, natural environment aging test and outdoor natural accelerated exposure test
60. Maximum allowable concentration
In order to prevent acute or chronic poisoning caused by chemical substances, governments all over the world have stipulated that the toxic vapor or dust contained in the air of the workplace should not exceed the value, which is called the maximum allowable concentration (MAC), usually expressed in mg / m3 or ppm. Conversion relationship between ppm and Mg / m3: mg / m3 = mg / m3 = m / 22.4 * [273 / (273 + T)] * (BA / 101325) ppm.
Test method: according to the current atmospheric monitoring and inspection method.